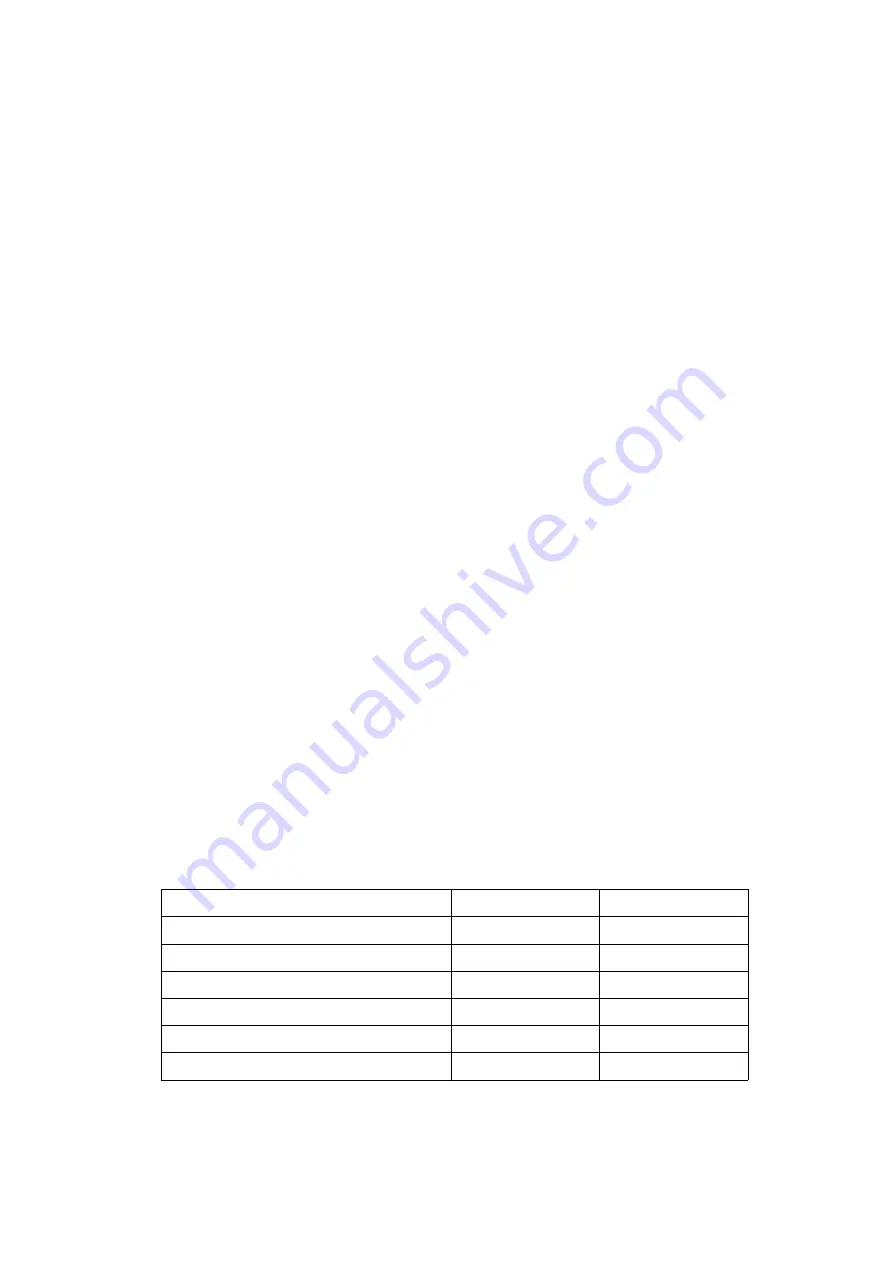
21
9.5 Removal of manifold to clean pilot orifice
With reference to Section 10.1, firstly disconnect the 2 electrical connectors from the coils.
With a 5mm Allen Key
remove the 2 socket head cap screws retaining the manifold assembly onto the valve body.
The pilot orifice (item 6) can now be inspected for contamination and cleaned.
Refit the O rings in the correct position. Assemble the manifold back onto the valve. The 2 socket head cap
screws should be refitted with a thread locking liquid applied to the thread and tightened to a torque of 20.3 Nm
(15 lbft).
9.6 Removal of pressure relief valve and bypass valve from flow control slice
With reference to Section 10.2, remove the bypass valve unscrew cap (6) and remove along with the bonded seal
(9) and spring (7). Using long nose pliers remove the spool (4) and bypass valve body complete with “O” rings.
Clean and rebuild.
To remove the Pressure Relief Valve unscrew the complete valve from the slice and inspect the seat for
contamination, clean and replace.
9.7 Adjusting the pressure relief valve.
To check the relief valve setting place an in line pressure gauge in the supply hose to the valve. Remove both
hoses from the bed chain hydraulic motor and blank both hose ends. ( 3/8” BSP blanking plug for the hose fitting).
Start the tractor and operate the bed chain with the bed chain speed control in its mid position. The pressure
shown on the gauge should be 120 bar. The pressure setting should remain the same throughout the whole
range of bed chain speed.
To adjust the bed chain pressure remove the cap (item 21 Section 10.2) over the relief valve. To increase the bed
chain pressure setting, turn the grub screw (item 20) clockwise until the desired setting is achieved. Replace the
cap.
9.8 Pressurising valve maintenance.
To check the operation of the pressurizing valve. Unscrew the valve assembly form the Outlet Cap (item 2
Section 10.5) and check the ball is seated correctly and free to move.
9.9 Leaks – seal replacement
Remove the hoses and electrical connections from the valve. Remove the valve on its mounting plate from the
machine. Take the mounting plate off the valve and thoroughly clean the valve of dirt and debris before stripping
the valve.
To split the valve to replace interface seals undo the long studs through the valve and separate individual slices.
Replace the damaged seals and reassemble the valve. Fitting of O rings not obtained from manufacturer may
lead to repeated failures as specific high quality grade O rings are used to seal the valve
The studs should be tightened to a torque of 13.5 Nm (10 lb ft).
9.10 Specific torque settings
Torque Setting (Nm) Torque Setting (lb ft)
Long studs through valve
13.5
10
Closure plate socket head cap screws
13.5
10
Manifold socket head cap screws
20.3
15
Cartridge valve assemblies
27.1
20
End cap unions (Inlet/Outlet) 1/2” BSP
70-75
52-55
Slice port unions
70-75
52-55
Table 9.10
Torque Settings