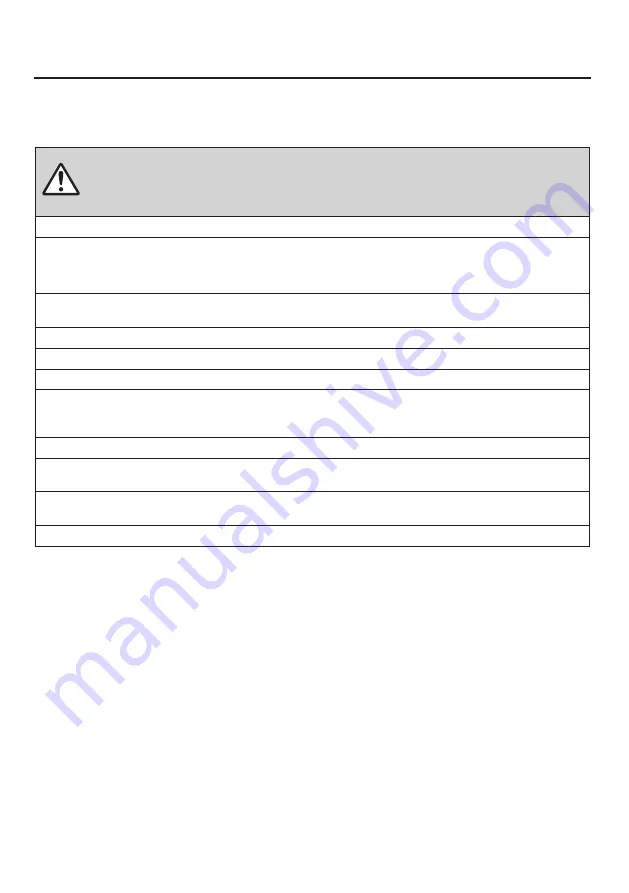
3
Safety information
This document describes the safety instructions for the operation of this unit. Before operating the product, read this document care-
fully to familiarize yourself with the unit.
WARNING
Follow the instructions below to avoid risk of serious
personal injury and death.
Never use beyond the rated specifications as there is the danger of property damage, injury, fire or electrical shock.
Never use in flammable gaseous environments including the following locations as there is the danger of explosion.
o
Locations containing corrosive or flammable gases
o
Locations near water, oil or subject to chemical splash
If this product malfunctions (smells strange or becomes hot), stop using it immediately and unplug the power cord as there is
danger of fire or electrical shock.
Never attempt to disassemble the product.
Carefully check connections and wiring before applying power.
Be sure to ground the product (with ground resistance of 100 Ω or less).
To allow the operator to immediately shut off the power to the product, install a switch or circuit breaker that complies with both
IEC60947-1 and IEC60947-3 requirements near the product. The switch or breaker installed must also indicate that it functions to
shut off the power to the unit.
Do not allow foreign objects such as metal fragments that result from cutting panels, wires or other materials to enter this unit.
If the unit is dropped or subject to strong impacts, it could break. If this occurs, stop using it and contact the seller from which
you purchased it.
Overvoltage category: I
Pollution degree: 2
If the unit is used in a manner not specified by the manufacturer, the protection provided by the unit may be impaired.