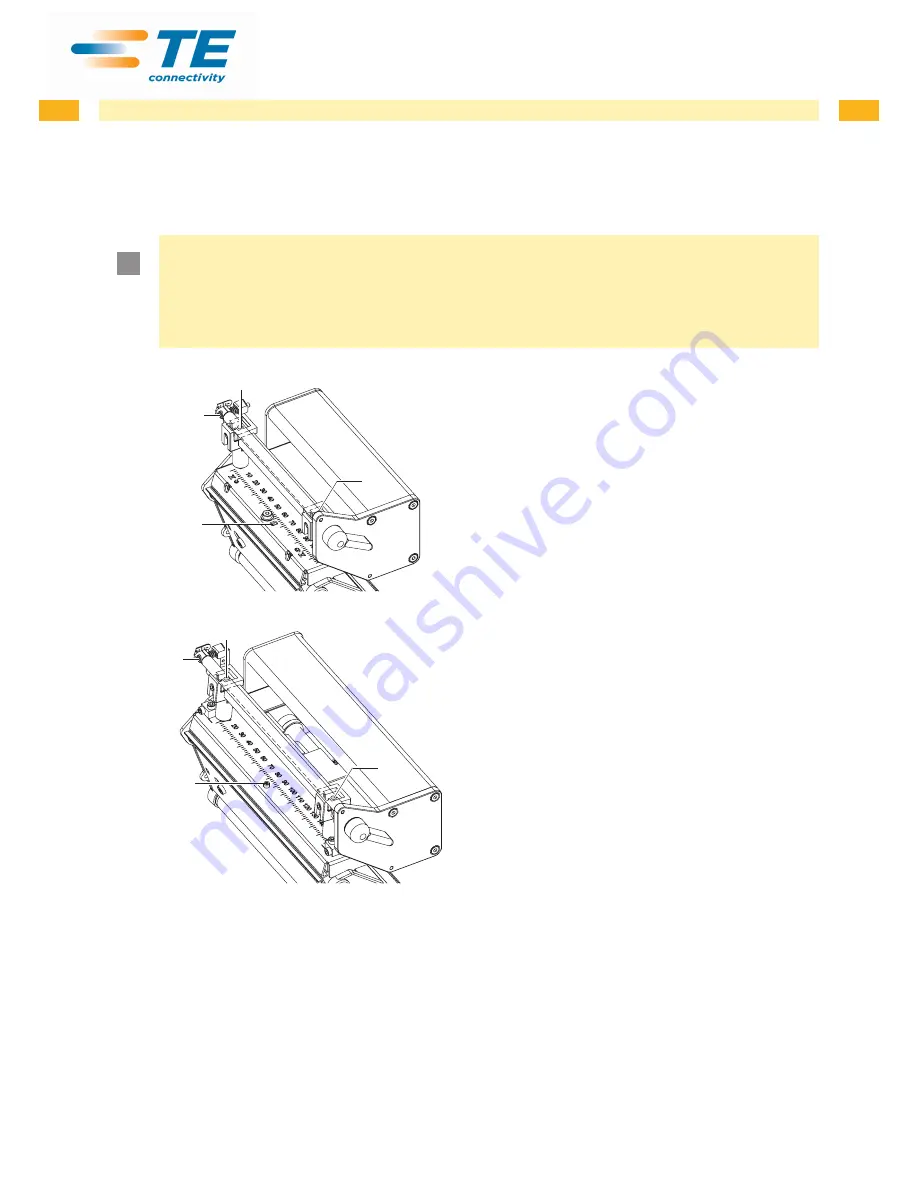
24
24
4 Adjustments
4.2.4 Adjusting the Transfer Ribbon Feed Path
You can adjust the transfer ribbon feed path by changing the head contact pressure and adjusting the transfer ribbon
deflection. Increasing the head contact pressure with the screws (3a) and (3b) shifts the ribbon feed path in the
corresponding direction. The skew of the transfer ribbon deflection is used to suppress wrinkles in the transfer ribbon
feed path. Wrinkles which cannot be remedied with the skew of the transfer ribbon deflection can be suppressed by
bowing the printhead.
!
Attention!
The printhead assembly can be damaged when bowing the printhead.
Turning the adjustment screw (1) too hard can cause damage to the printhead assembly.
X
As soon as you perceive clear resistance when turning the adjustment screw (1), you may only continue
turning the screw in very small increments, but no more than one eighth of a turn.
X
Only turn the adjustment screw (1) as far as is absolutely necessary.
2
1
3a
3b
3a
2
1
3b
1. Check the transfer ribbon feed path.
The wound up ribbon should be the same distance
from the disk of the winder as the supply roll is from
the disk of the supply hub.
2. If the ribbon runs inward or outward, turn the corre-
sponding screw (3a) or (3b) clockwise in small
increments.
3. Wait until the ribbon feed path has stabilized after
each step of the adjustment.
4. Check the ribbon feed path for wrinkles.
5. If wrinkles arise on the inside, turn the screw (2)
counterclockwise.
6. If wrinkles arise on the outside, turn the screw (2)
clockwise.
7. If the wrinkles cannot be remedied (e.g. wrinkles in
the center), turn the adjustment screw (1) clockwise
with extreme care
using an Allen key (1.5 mm) and
observe the ribbon feed path.
When the adjustment screw (1) is tightened, the
printhead is bent downward slightly in the center. It is
possible that a slight lightening at the edge areas of
the print image could occur here.
8. If bowing is not necessary, turn the screw (2)
clockwise until the screw is just barely clamping.
9. When the transfer ribbon feed path is set, continue
with the final test.
Fig. 20
Adjusting the transfer ribbon feed path
4.2.5 Final Test
X
Reset the
Heat level
to +5 in the printer configuration
X
Recheck the setting with the test function
Test grid
or a similar print pattern.
When using standard media, the test printout must show lines with sharp contours and black areas without any parts
missing.