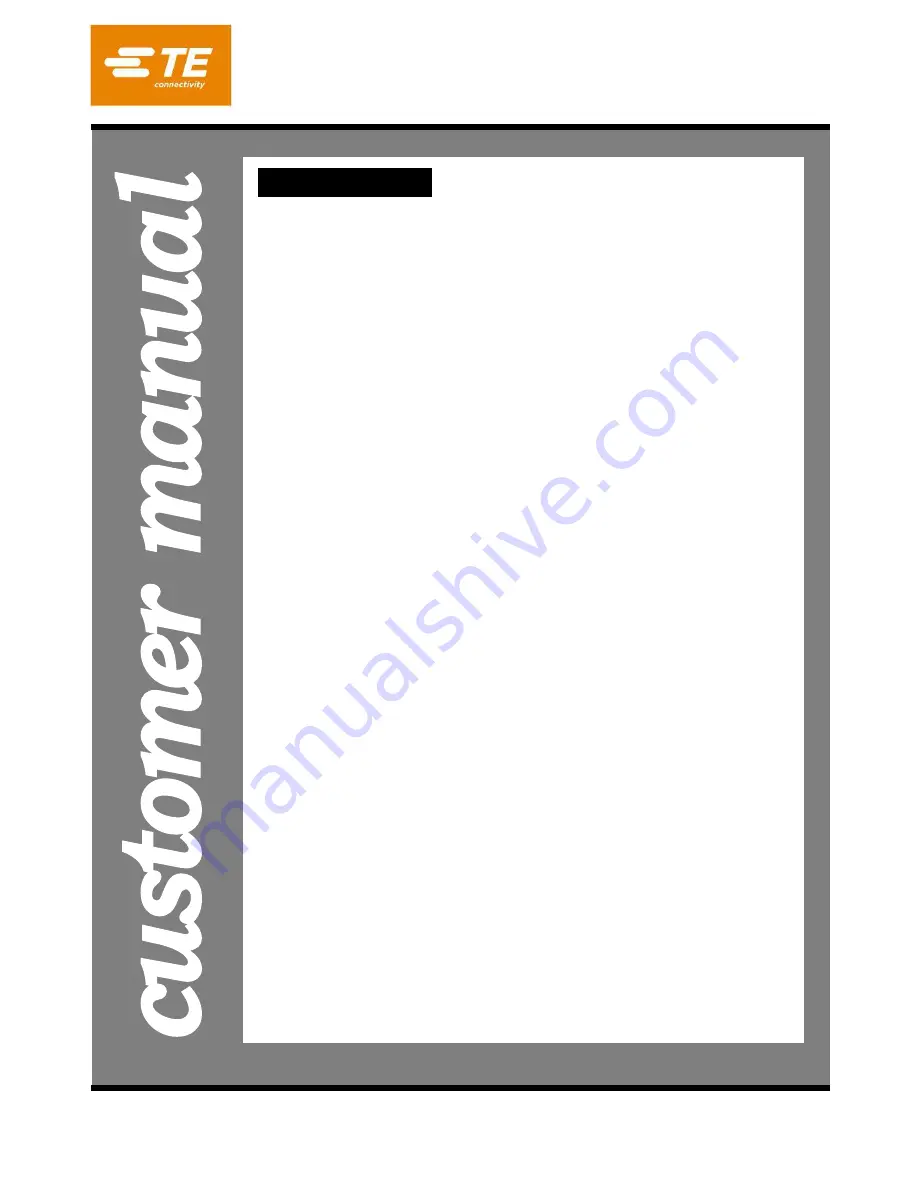
1
of 31
© 2016 TE Connectivity family of companies
All Rights Reserved
*Trademark
TE Connectivity, TE connectivity (logo), and TE (logo) are trademarks. Other logos, product, and/or company names may be trademarks of their respective owners.
TOOLING ASSISTANCE CENTER 1-800-722-1111
This controlled document is subject to change.
For latest revision and Regional Customer Service,
visit our website at
www.te.com
.
Customer Manual
409-32034
16 SEP 16 Rev D
SAFETY PRECAUTIONS
READ THIS FIRST! ............................................................. 2
1.
INTRODUCTION .................................................................................................................. 3
2.
DESCRIPTION ..................................................................................................................... 4
2.1.
Functional Description ................................................................................................. 5
2.2.
Electrical Description ................................................................................................... 6
2.3.
Machine Guard (Figure 7) ........................................................................................... 8
3.
RECEIVING INSPECTION AND INSTALLATION ............................................................... 9
3.1.
Receiving Inspection ................................................................................................... 9
3.2.
Installation ................................................................................................................... 9
3.3.
Considerations Affecting Placement of Bench Machines .......................................... 10
4.
OPERATION ...................................................................................................................... 11
4.1.
Machine Operation .................................................................................................... 11
4.2.
Crimp Quality Monitor II (CQM II) .............................................................................. 11
4.3.
Applicator Installation ................................................................................................ 14
4.4.
Setup ......................................................................................................................... 14
4.5.
Mode Selection and Operation .................................................................................. 15
4.6.
Crimp Height Adjustment .......................................................................................... 17
4.7.
End-Feed/Side-Feed Applicator Conversion ............................................................. 17
5.
MACHINE FAULT CODES ................................................................................................ 17
6.
PREVENTIVE MAINTENANCE ......................................................................................... 18
6.1.
Cleaning .................................................................................................................... 18
6.2.
Lubrication ................................................................................................................. 18
7.
ADJUSTMENTS ................................................................................................................. 19
7.1.
Measuring the Shut Height ........................................................................................ 19
7.2.
Shut-Height Adjustment ............................................................................................ 20
7.3.
Crimp Height Adjustment Using Precision Adjustment Mechanism .......................... 21
7.4.
Guard Insert Adjustment ........................................................................................... 22
8.
MACHINE OPTIONS AND INSTALLATION ...................................................................... 24
8.1.
Installation of Work Light Assembly Kit ..................................................................... 24
8.2.
Installation of the Work Light Assembly Kit ............................................................... 26
8.3.
Installation of Batch Counter Kit 1424267-1 .............................................................. 27
8.4.
Installation of Air Feed Kit 1424266-1 ....................................................................... 28
9.
TROUBLESHOOTING ....................................................................................................... 31
10.
RoHS INFORMATION ........................................................................................................ 31
11.
REVISION SUMMARY ....................................................................................................... 31
AMP 3K* Terminating Machine 1725950-[ ] and
AMP 5K* Terminating Machine 1725900-[ ]
O
R
IG
IN
A
L
IN
S
TR
U
C
TIONS