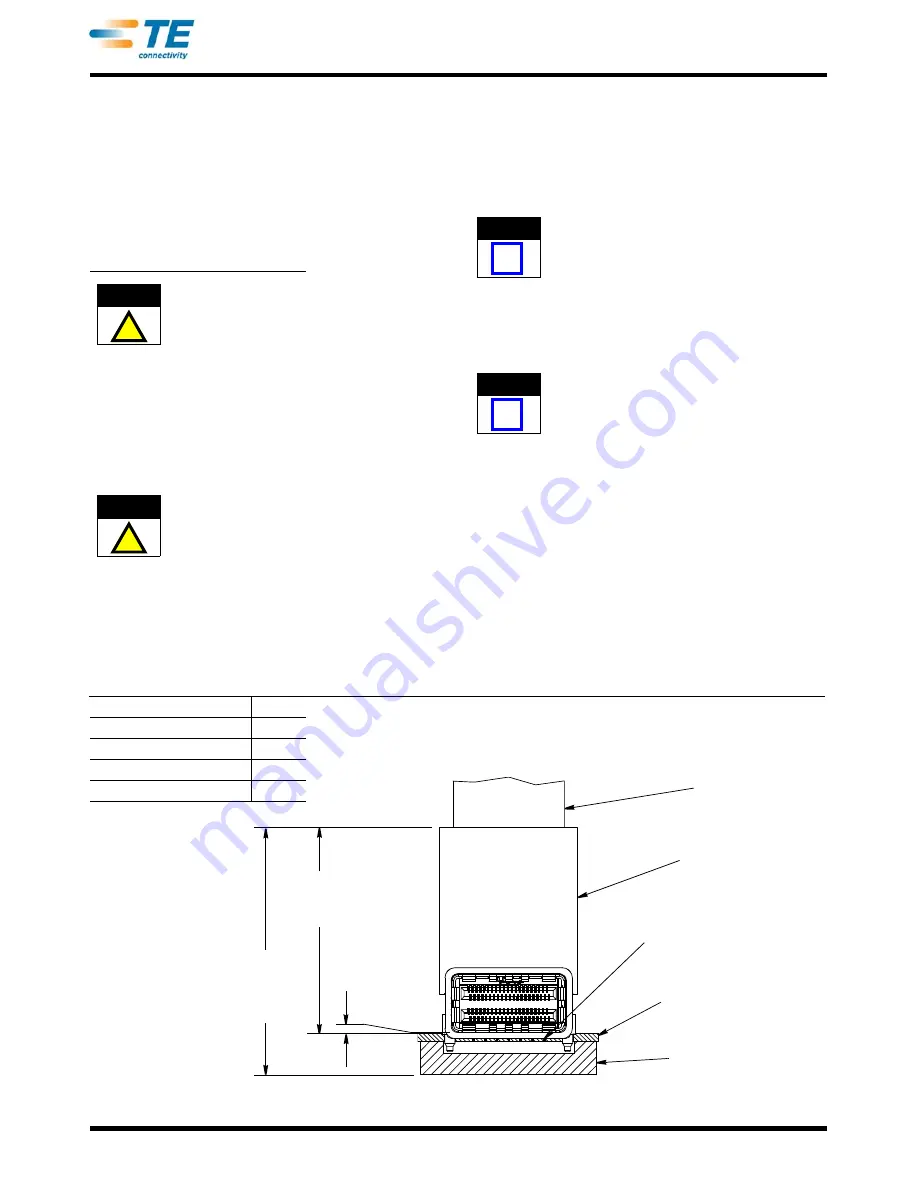
408-10380
2
of 3
Rev
C
3.2. Application Tool
Power for the seating tool must be provided by
application tools (with a ram) capable of supplying a
downward force of 24.5 N [5.5 lb] per contact.
Manual Electric Servo Press (MEP 6T) 2-1399500-5
and Bench Top Electric Servo Presses (BMEP 3T)
1-1399400-5 and (BMEP 5T) 2-1399401-4 are
available for this seating tool. For press information,
visit the press-fit assembly equipment website at
http://tooling.te.com/pressfit.asp.
Over-driving of the cage assembly will deform
parts critical to the quality of the connection.
Maximum force occurs prior to the cage assembly
bottoming on the pc board.
4. SETUP
When setting up equipment to seat the cage
assembly, pay particular attention to the following:
•
the seating tool must be matched to the cage
assembly
If the seating tool and cage assembly are
mismatched or are improperly aligned, damage
could occur to the tooling, cage assembly, or both
•
light pipes and/or heatsinks MUST NOT be
assembled onto the cage assembly.
•
the wall support must be properly installed, and
the seating tool, cage assembly, and application
tool ram must be properly aligned before cycling
the application tool
1. Set the tool seating height to the dimension
shown in Figure 2 (application tool shut height
will equal the tool seating height PLUS the
combined thicknesses of the pc board and
support fixture). After seating, a gap of no more
than 0.10 mm between the cage assembly
standoffs and the pc board is allowed.
Use the tool seating height as a reference starting
point. This height may need to be adjusted to
obtain the amount allowed (maximum of 0.10 mm)
between the standoffs of the cage assembly and
the pc board.
2. Slide the wall support into the ports of the
cage assembly until the wall support is secure.
5. SEATING
(See Figure 2)
The connector must be mounted on the pc board
BEFORE seating the cage assembly.
1. Place the pc board on the support fixture.
2. Orient the seating tool over the cage
assembly so that the back is aligned with the
back of the cage assembly. Then lower the
seating tool onto the cage assembly, making
sure that the cutouts slide over the protruding
components of the cage assembly, until the
seating tool bottoms on the top of the cage
assembly.
3. Place the cage assembly on the pc board so
that the contacts and alignment posts are
aligned and started into the matching holes in
the pc board.
Figure 2
CAUTION
!
CAUTION
!
NOTE
i
NOTE
i
PC Board Support Fixture
Customer Supplied)
Printed Circuit (PC) Board
Ram of Application
Tool (Fully Down)
Seating Tool
Compliant Pin Contacts (and
Any Protruding Components)
Inserted Into Holes in PC Board
and PC Board Support Fixture
Tool Seating Height
“A” (With Cage
Assembly Seated)
0.10 (Max)
Gap Allowed
Application Tool
Shut Height (Ram
Fully Down) See
Section 4, Step 1
CONNECTOR TYPE
“A”
Standard (Without Cover)
42.15
Standard (With Cover)
42.37
Belly-Belly (Without Cover)
41.80
Belly-Belly (With Cover)
42.05