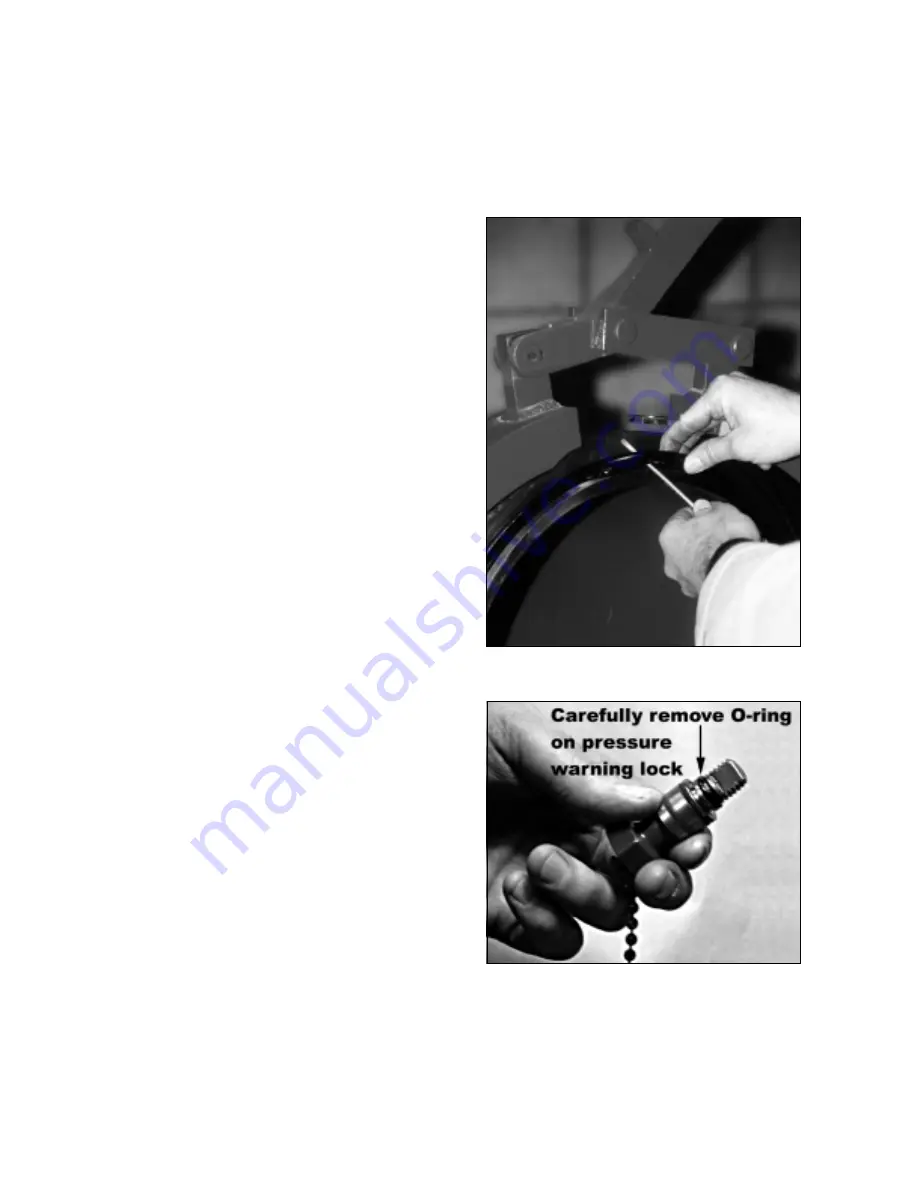
3
Section II: Installation and Operation
1.0 Installation
1.1 General
A. To maintain the closure in proper working
order, those making the shop or field
installation must carefully follow the welding
instructions and preventive maintenance
instructions.
B. It is important to keep the following points in
mind during installation:
•
Level the closure during the installation
process;
•
Properly align the barrel collar;
•
Position the door hinge in the vertical
position (horizontal on a vertical
installation) to permit easy opening and
closing of the door.
C. A bleeder valve and a pressure gauge must be
installed on the vessel the closure is welded
to. An operator must be able to bleed the
vessel and determine when there is zero (0)
psig within the vessel.
1.2 Welding Procedures
A. The same welding procedures are to be used
whether post-weld heat treatment is required
or not.
1. Remove closure door O-ring and pressure
warning lock O-ring before welding. (See
Figures 2 and 3.)
2. If post-weld heat treatment is required, it is
recommended that it be accomplished by
localized stress relieving. If that is not
possible, the closure door must be
removed prior to heat treatment. (See
Section II, subsection 3.1, beginning on
page 9, for removal instructions.)
Figure 2. Remove O-Ring on Closure Door
Figure 3. O-Ring on Pressure Warning Lock