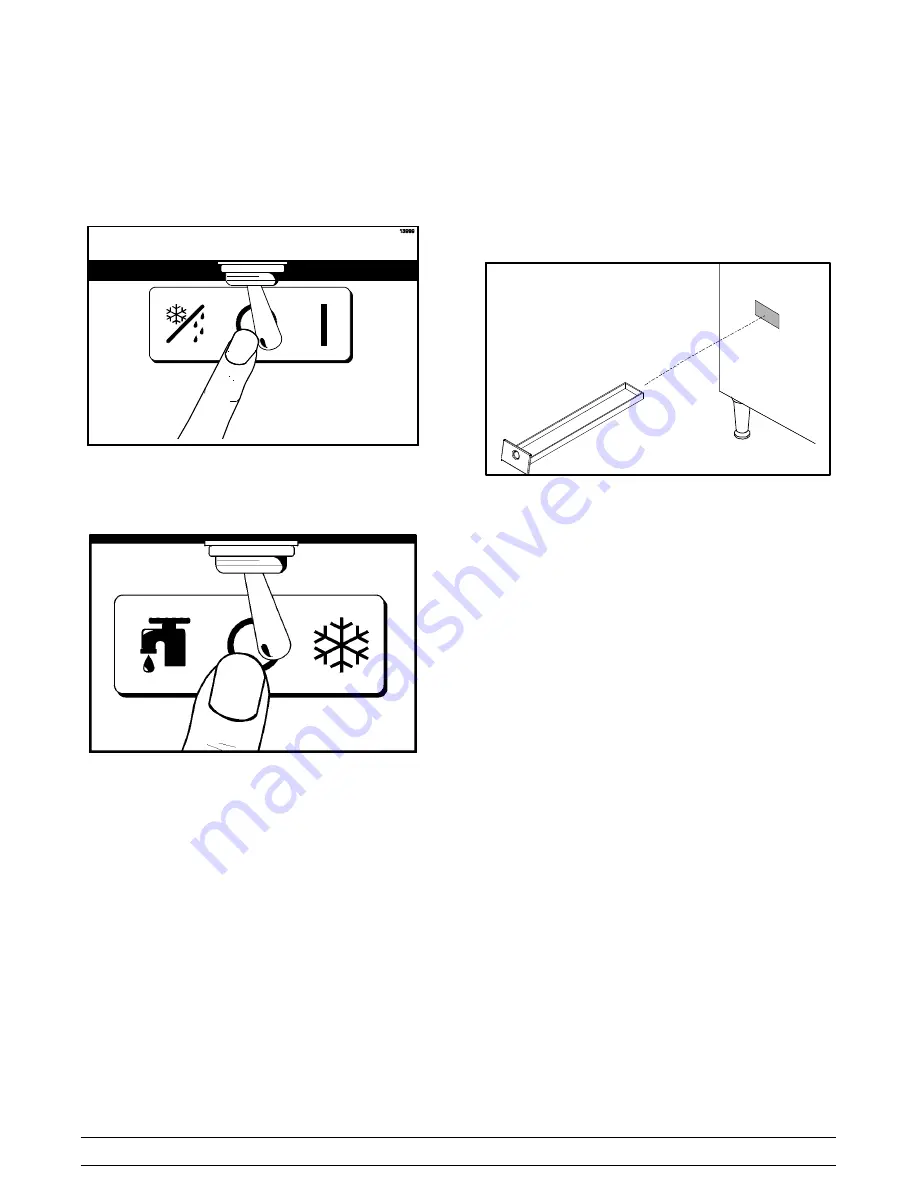
24
Models 150, 152, 162, 168
Operating Procedures
150105
Step 3
Place the mix hopper cover in position.
Step 4
Place the mix refrigeration switch in the “ON” position.
Figure 38
Step 5
Place the power switch in the “AUTO” position.
Figure 39
Step 6
Momentarily raise the draw switch paddle to activate
the refrigeration cycle. When the unit cycles off, the
product will be ready to serve.
Repeat the applicable steps
for the second freezing
cylinder on Models 162/168.
Step 7
Slide the rear drip pan into the hole in the side panel.
Figure 40
Closing Procedure
To disassemble the Models 150/152/162/168, the
following items will be needed:
S
Two cleaning pails
S
Sanitized stainless steel rerun can with lid
S
Necessary brushes (provided with freezer)
S
Cleaner
S
Single service towels