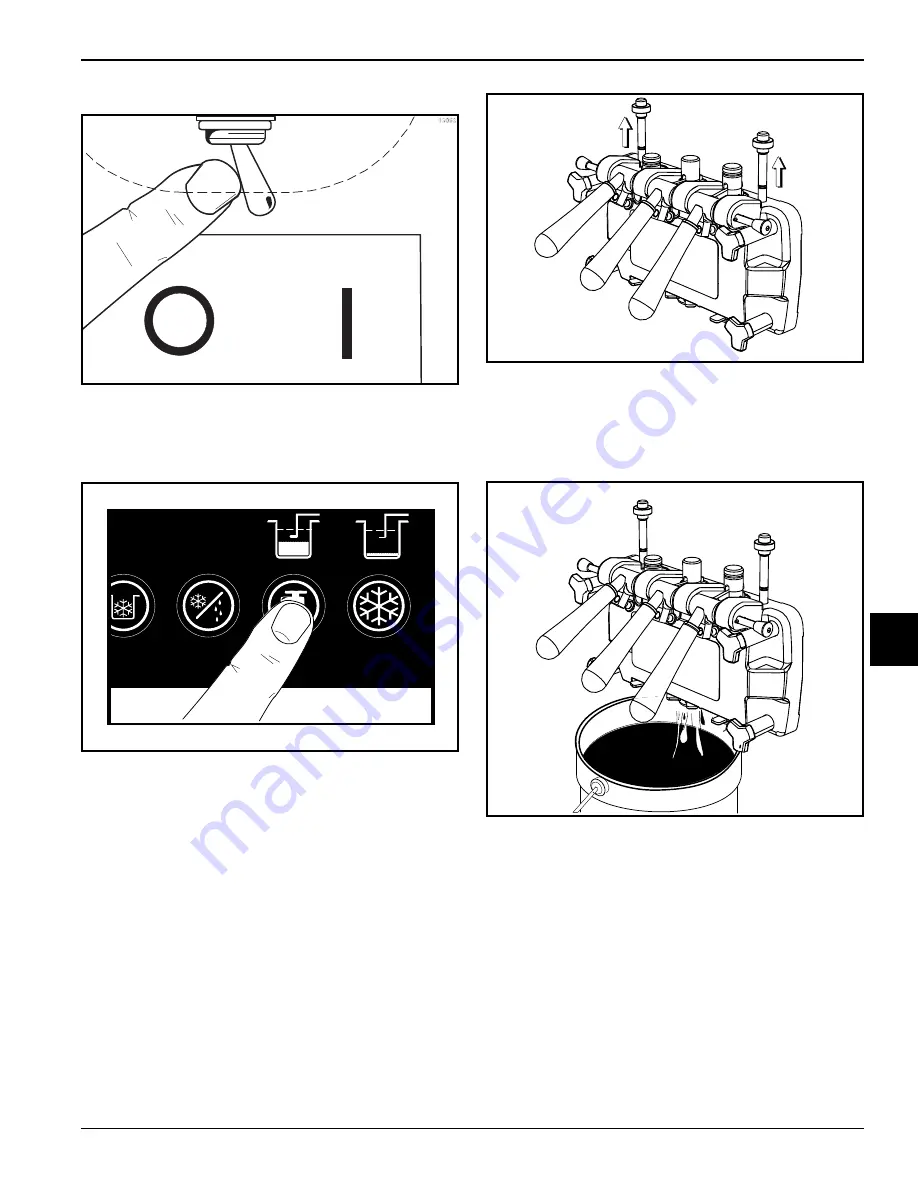
OPERATING PROCEDURES
6-7
087482-M
Operating Procedures
6
4.
Place the power switch in the ON position.
Figure 6-24
5.
Press the WASH key to cause the sanitizing solution
in the freezing cylinder to be agitated. Allow it to
agitate for five minutes.
Figure 6-25
6.
Place an empty pail beneath the door spouts and
raise the prime plugs.
7.
Momentarily pull the center draw handle down to
sanitize the center door spout.
Figure 6-26
8. When a steady stream of sanitizing solution is flowing
from the prime plug opening in the bottom of the
freezer door, lower the draw handle. Draw off all the
sanitizing solution.
Figure 6-27
9. Once the sanitizer stops flowing from the door spout,
raise the draw handle and press the WASH key,
canceling the beater motor operation.
Important!
You have just sanitized the freezer.
Be sure
your hands
are sanitized before continuing these
instructions.
13054w
131558
30141_A
30142_A
Summary of Contents for C791
Page 8: ...1 4 TO THE INSTALLER 087482 M To the Installer 1 ...
Page 38: ...9 2 PARTS REPLACEMENT SCHEDULE 087482 M Parts Replacement Schedule 9 Notes ...
Page 42: ...10 4 LIMITED WARRANTY ON EQUIPMENT 087482 M Limited Warranty on 10 Notes ...
Page 46: ...11 4 LIMITED WARRANTY ON PARTS 087482 M Limited Warranty on Parts 11 Notes ...