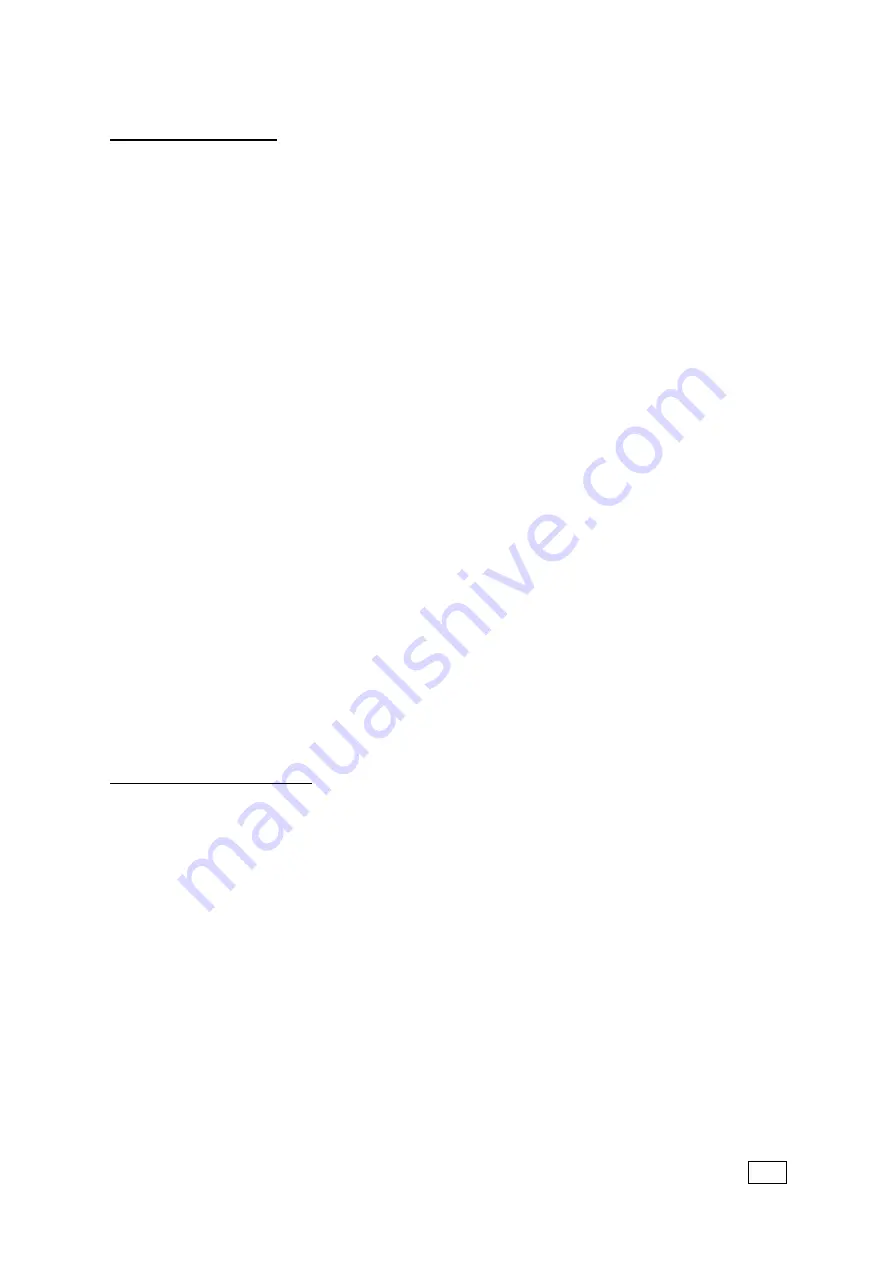
V
-
21A
WELD TESTING
16
There are two factors which should receive special attention in establishing visually whether or not
a stud weld is sound. These are :
•
The length after weld (L.A.W.) of the stud should be correct. That is to say that a stud which is
intended to be 50 mm long after welding, should be correct 0/
-
1 mm. A word of
explanation is perhaps needed on this point. All studs produced include a "weld allowance".
This allowance is so arranged for the different diameters of stud, that it will be completely
melted during the welding process, provided of course that the correct conditions have been
established and the correct values of current and time are used.
•
The fillet of metal formed around the base of the stud should be well formed, reasonably
evenly distributed, completely free from blow holes and of a silver blue colour.
These two factors combined form the basis of all visual stud weld examination. It should be the aim
of every operator to produce these results.
Under normal conditions a stud welded to clean mild steel plate of adequate thickness having the
correct L.A.W. and fillet formation. as described above, will be a satisfactory weld.
It should be remembered, however, that different applications or conditions will produce slightly
different visual results, particularly in the appearance of the fillet, i.e.. Slightly rusty, dirty or oily
plate will produce blow holes in the fillet, in proportion to the degree of plate contamination.
Welding close to some magnetic obstruction may produce uneven fillet distribution. Too much
power will produce a fillet that flows too easily and is lost either up in the threads of the stud or out
through the ferrule vents, while too little power may not melt sufficient material to form a complete
fillet.
It is important, therefore, to judge the degree to which these possible variations will affect the weld
strength, but in general, provided that the L.A.W. is correct and the fillet formation is not unsightly,
a visual examination is all that is required.
Further testing may be carried out on a "percentage of production" basis, and the methods used fall
into the classes outlined below.
1.
DESTRUCTIVE TESTING.
Should only be used on studs welded to samples and test pieces.
•
Hammering a stud over may look spectacular, but it is not a satisfactory test, as the direction
and force behind the blows is uncontrolled, as also is the point at which the impact takes
place. The length, diameter and type of stud also have an effect on the results obtained.
•
Bending the stud over by using a tube of approximately the same bore as the stud diameter.
This method is preferred to hammering, but again no conclusive evidence as to the strength
of the weld is obtained.
•
Loading the stud by the use of washers / spacer and a nut until the stud breaks. This method
is much more conclusive and should show that the weld is in fact stronger than the stud. Use
of a suitably calibrated torque wrench for this test will give an indication of the U.T.S.
developed by the stud material under test.