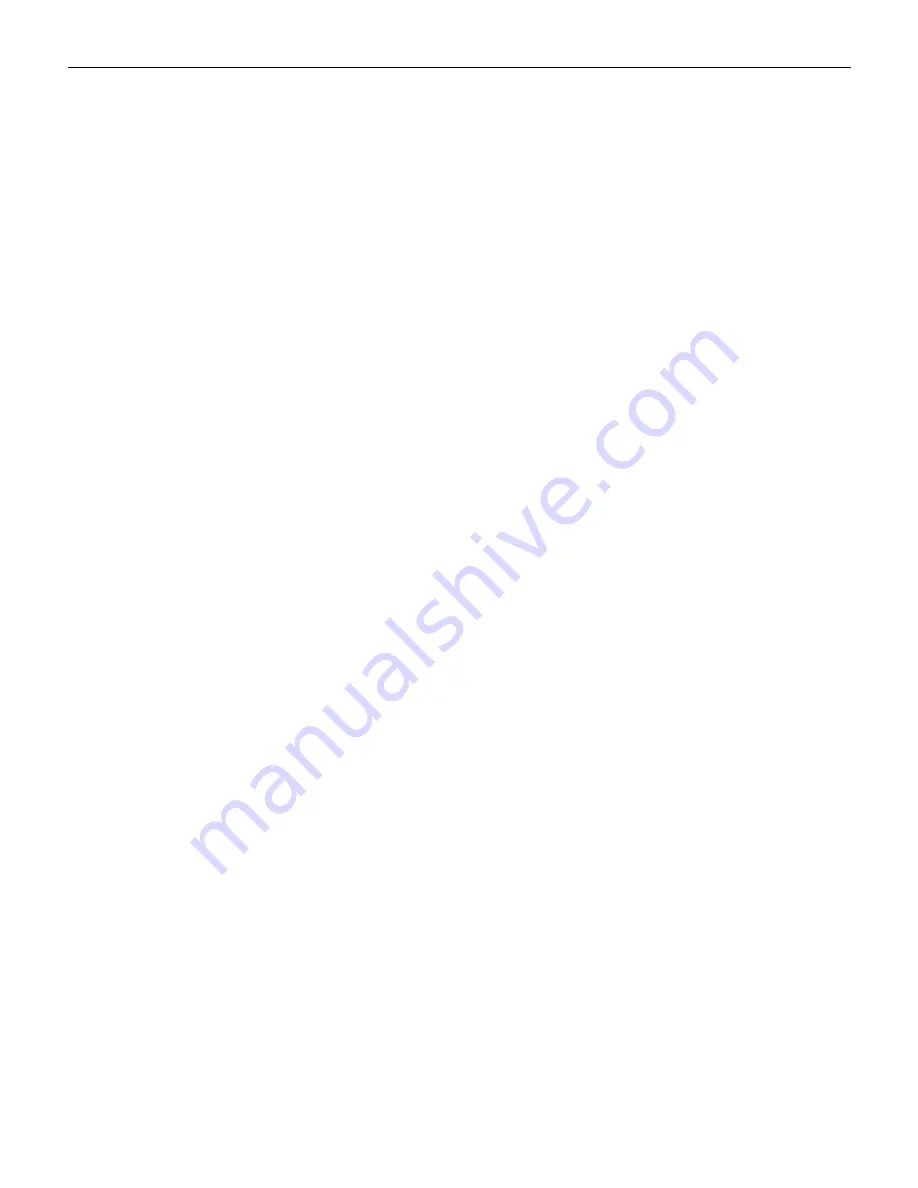
17
❖
❖
❖
❖
❖
English
L-2066
L-0123 Revised: 7-19-01
1. Determine the manufacture date of the component from
the serial number on the data plate. If you are not
familiar with the date code, write or call the TME
Customer Service Department at (804)746-1313, to
obtain the manufacture date. The hours of the Cus-
tomer Service Department are 8:00 am - 5:00 pm USA,
Eastern Time Zone) Monday through Friday excluding
holidays.
2. It is possible that there might exist a considerable time
lag between the date a component is manufactured and
the date it is put in service. In such instances, the date
of manufacture could indicate that the item is out of
warranty. However, based on the date the equipment is
first put in service, the item may still be covered by the
TME warranty described in
Section I
. For proof of date
put in service, TME will require a copy of the bill of sale
of the TME equipment from the installer or new boat
dealer to the original owner.
Section IV
How do you get service? Please Read the follow-
ing Warranty Procedure.
WARRANTY PROCEDURE
If the failure of a TME component is determined to be
covered under the TME warranty and the time in service is
determined to be within the warranty time limit, the owner
has the following three options:
1. Preferred option: Have an TME authorized Servicing
Dealer perform the work needed. The customer should
call TME's Service Department for a recommendation
as to the closest dealer. If the customer already knows
an authorized servicing dealer, the dealer should be
contacted directly.
2. If the customer contacts TME's Service Department for
a Servicing Dealer and TME has no one in that particu-
lar area, TME will authorize the use of a local service
company and TME will work with the local company to
assist in any way possible.
3. The customer may send his equipment back to the
factory to have the repair work done. TME will make
every effort to return the equipment to the customer
within a three week time period. If the claim represents
a legitimate warranty problem, TME will pay the freight
both ways. TME prefers option one and two, if at all
possible.
The customer may contact the TME Service Department at
(804) 746-1313.
WARNING
Taylor Made Environmental, Inc. (TME) manufacturers of Cruisair, Grunert, Marine
Air, Sentry and Tundra Products, makes the following safety warnings concerning
the application, installation, use and care of its products. Although these warnings
are extensive, there may be specific hazards which may arise out of circum-
stances which we have not outlined herein. Use this as a guide for developing an
awareness of potential hazards of all kinds. Such an awareness will be a key
factor in assuring your SAFETY and comfort.
ELECTRICITY - Many TME products operate on 115, 230 or 440 volt AC power.
Such voltages can be LETHAL; therefore, the chassis, cabinets, bases, etc., on all
components must be grounded together and connected to the vessel's grounding
system. Sparks can occur as switches, thermostats and relays open and close in
the normal operation of the equipment. Since this is the case, ventilating blowers
for the removal of hazardous fumes or vapors should be operated at least 5
minutes before and during operation of any TME product or group of TME
products. All electrical connections must be covered and protected so accidental
contact cannot be made by persons using the equipment, as such contact could
be LETHAL.
ELECTROLYSIS - Electrical leakage of any component can cause electrolytic
deterioration (electrolysis) of thru-hull components which could result in leakage
serious enough to sink a vessel which could result in loss of life. All TME
components must be kept clean and dry and checked periodically for electrical
leakage. If any electrical leakage is detected, the component should be replaced
or the fault causing the leakage corrected before the component is put back into
service.
GAS - CRUISAIR, MARINE AIR, GRUNERT and TUNDRA components utilize R-22
(Chlorodifluoromethane), R134a refrigerant (Tetrafluoroethane), R-407C (which
contains Diflouromethane (HFC-32), Pentafluoroethane (HFC125), and 1.1.1.2 -
Tetrafluoroethane (HFC134a)), or R404A (R125/R143a/R134 (44%/52%/4%))
which are non-toxic, non-flammable gases; however, these gases contain no
oxygen and will not support life. Refrigerant gas tends to settle in the lowest areas
of the compartment. If you experience a leak, evacuate all personnel, and
ventilate area. Do not allow open flames in the area of leaks because refrigerant
gas, when burned, decomposes into other potentially LETHAL gases. Refrigerant
components operate at high pressure and no servicing should be attempted
without gloves, long-sleeved clothing and eye protection. Liquid refrigerant gas
can cause severe frost burns to the skin and eyes.
VENTILATION - To cool or heat air, CRUISAIR, MARINE AIR and GRUNERT
components are designed to move air through a heat exchanger by a blower or
propeller fan. This design necessarily produces a suction on one side of the air
handling component and a pressure on the other side. Air handling components
must be installed so that the suction-pressure action does not: (1) pressurize an
area to the extent that structural failure occurs which could cause harm to
occupants or bystanders, or (2) cause a suction or low pressure in an area where
hydrogen gas from batteries, raw fuel vapor from fuel tanks, carbon monoxide
from operating propulsion engines, power generators or heaters, methane gas
from sewage holding tanks, or any other dangerous gas or vapor could exist. If an
air handling unit is installed in such a manner that allows potentially lethal gases
or vapors to be discharged by the air handling unit into the living space, this could
result in loss of life.
Maximum protection against the introduction of dangerous gases or vapors into
living spaces can be obtained by providing living spaces which are sealed from all
other spaces by use of airtight bulkheads and decks, etc., and through the
introduction of clean air into the living space. Bear in mind that the advent of air
conditioning, whether it be for cooling or for heating, naturally leads to the practice
of closing a living space tightly. Never close all windows and doors unless
auxiliary ventilating systems, which introduce clean outside air into the living
space, are used. Always leave enough window and door openings to provide
adequate ventilation in the event potentially lethal gases or fumes should escape
from any source.
CONDENSATE - All cooling units produce water condensate when operating on
the cooling cycle. This water must be drained from the cooling unit overboard. If
condensate is allowed to drip on a wooden structure, rotting or decay and
structural failure may occur which could result in loss of life. If condensate is
allowed to drip on electrical components, deterioration of the electrical compo-
nents could result in hazardous conditions. When an air conditioning system is in
operation, condensate drains may be subjected to negative pressure. Always
locate condensate drains as far as possible from points where engine waste and
other dangerous gases are exhausted so no such dangerous gases can be drawn
into the condensate drains.
Warning
Never sleep in a closed area on a boat when any equipment, which functions as a
result of the combustion of a volatile fuel, is in operation (such as engines,
generators, power plants, or oil-fired heaters, etc.). At any time, the exhaust
system of such devices could fail, resulting in a build-up of LETHAL gases within
the closed area.
Warning Revised: 7-19-01
Summary of Contents for Cruisair SMX II
Page 20: ...20 L 2066 Fig 1 SXR7 16CK 115 230V 50 60Hz...
Page 21: ...21 L 2066 Fig 2 SX7 24CK 115 230V 50 60Hz...
Page 22: ...22 L 2066 Fig 3 FX5 36CK 115 230V 50 60Hz...
Page 23: ...23 L 2066 Fig 4 FX48RC 230V 50 60 Hz...
Page 24: ...24 L 2066 Fig 5 FX20DC FX48EC 230V 460V 3Ph 50 60Hz...
Page 25: ...25 L 2066 Fig 6 SMXII Retrofit Typical 3 knob...
Page 26: ...26 L 2066 Fig 7 SMXII Retrofit F20C 48RC to 3 knob term strip...
Page 27: ...27 L 2066 Fig 8 SMXII Retrofit F20C 48RC to condensing unit...
Page 28: ...28 L 2066 Fig 9 Cable Diagrams Old and New P L Boards...
Page 29: ...29 L 2066 Fig 10 SMXIR Mounting Template and Instructions...