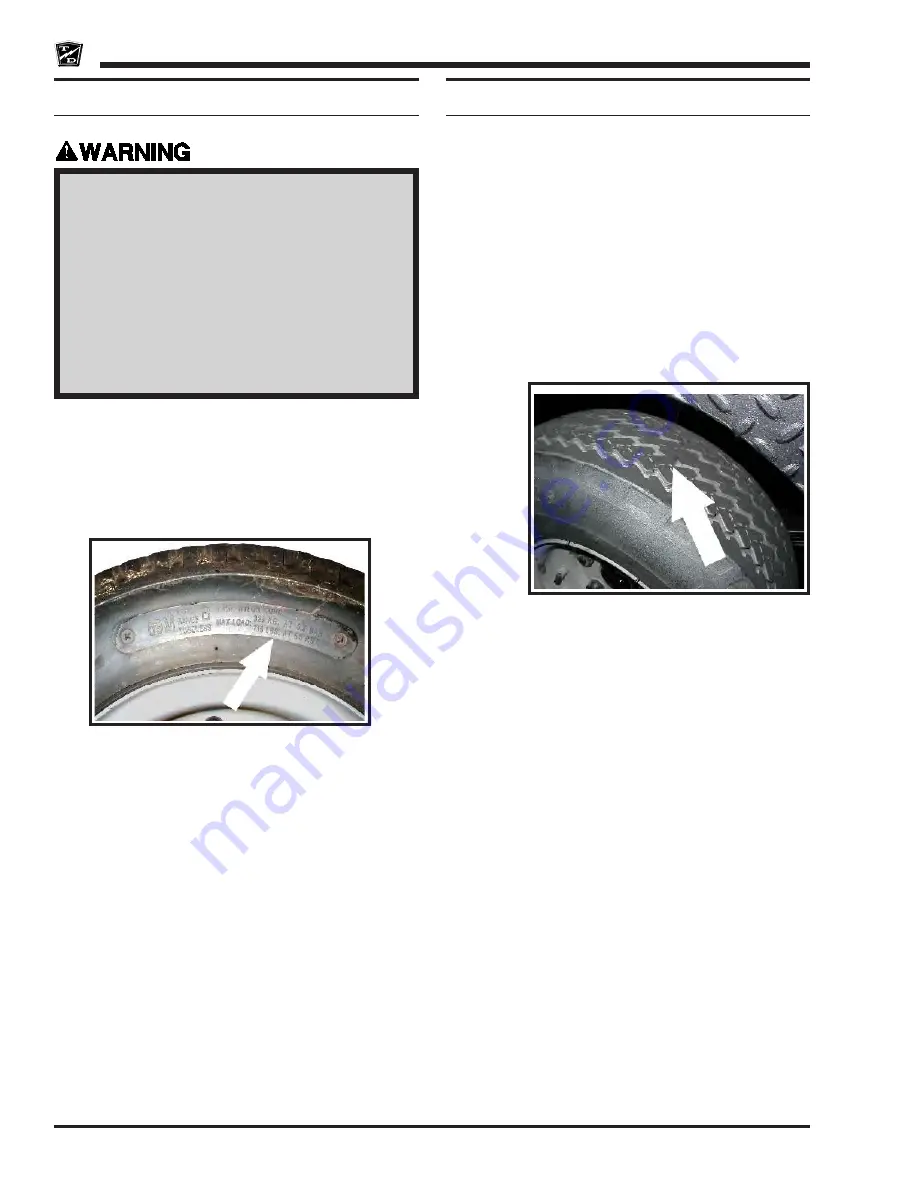
Maintenance, Service, and Repair
Tires and Wheels
Page 2
TIRE INFLATION
There are many tire options available with varying
tire pressures. Refer to the side wall of your tire for
information regarding the tire pressure for your tires.
The illustration to the right is an example of the side wall
information on a tire.
Tire pressures must be checked when the tire is cold.
1. Make sure the key-switch is in the “OFF”
position, then remove the key.
2. Place the forward-reverse switch in the
center “OFF” position.
3. Set the park brake.
4. Place blocks under the front wheels to
prevent vehicle movement.
5. Disconnect the main positive and
negative cables at the batteries.
TIRE INSPECTION
6. Check the tire pressure. Refer to
Tire Inflation
section for information on checking the tire
pressure.
7. Inspect the tire tread depth. Minimum recommended
tread depth is 1/16-inch. There are a series of tread
depth wear indicators around the circumference of
the tire. They will appear as 1/2-inch bands across
the tread as the tire approaches its wear limit (see
illustration below). Replace the tire if any tread
depth indicator can be seen or any part of the tread
depth is 1/16-inch or less. Refer to
Replace the
Tire
section for information regarding replacing
the tire.
8. Inspect for uneven tire wear on the front tires.
Uneven tire wear could be a result of an improperly
inflated tire or a misaligned or damaged front end.
Note: Refer to
Tire Inflation
section or Steering
Component Service section for information
on proper tire inflation or front end wheel
alignment.
9. Inspect the inner and outer side walls for cracks.
If any cracks are seen, then the tire should be
replaced. Refer to
Replace the Tire
section for
information regarding replacing the tire.
10. Inspect the valve stem for cracks. If any cracks are
seen, then the valve stem should be replaced. It is
also recommended that the valve stem be replaced
whenever the tire is replaced.
Note: Refer to Replace the Tire section for
information regarding replacing the valve
stem.
11. Inspect the tread and side walls for debris in the
rubber that could lead to a puncture. If any debris is
found it should be removed and the tire inspected
for a leak.
Summary of Contents for SC 0-90
Page 2: ......
Page 10: ...Page 6 Notes...
Page 12: ...Notes...
Page 34: ...Front Axle Page 6 Notes...
Page 66: ...Transmission Page 8 Notes...
Page 80: ...Batteries Page 10 Notes...
Page 85: ...TABLE OF CONTENTS Remove Install 2 Troubleshooting 2 Charger...
Page 88: ...Wire Diagrams Page 2 Notes...
Page 90: ...Illustrated Parts Parts Page 2 Axle Front and Fork...
Page 94: ...Illustrated Parts Parts Page 6 Brake Linkage...
Page 100: ...Illustrated Parts Parts Page 12 Knee Pad and Floor Mats optional...
Page 106: ...Illustrated Parts Parts Page 18 Motor...
Page 110: ...Illustrated Parts Parts Page 22 Speed Control Panel...
Page 112: ...Illustrated Parts Parts Page 24 Steering Linkage...
Page 114: ...Illustrated Parts Parts Page 26 Throttle Linkage Slip joint detail...
Page 116: ...Illustrated Parts Parts Page 28 Transmission...
Page 118: ...Illustrated Parts Parts Page 30 Wheels and Tires page 1...
Page 129: ......