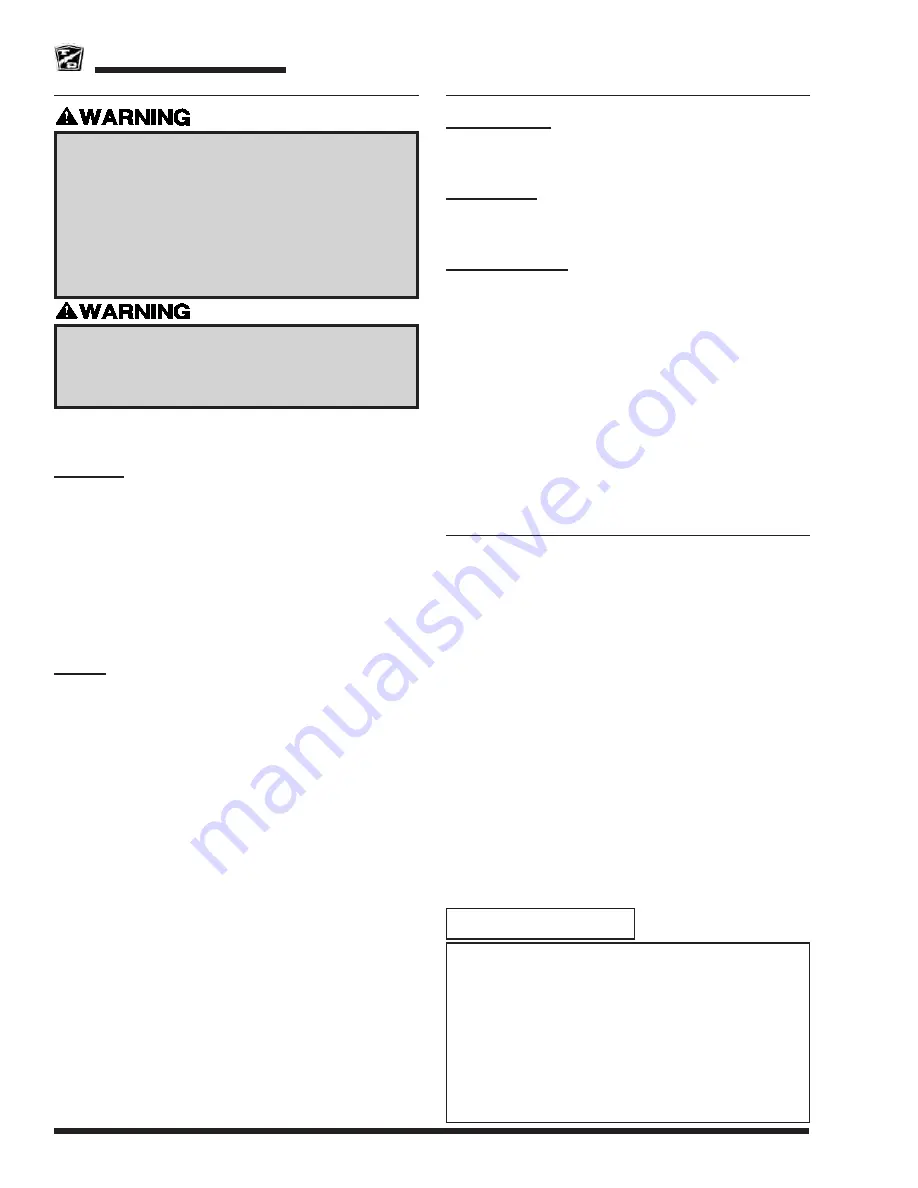
Motor Controller
Page 2
MB-T48-02
T-48 AC / ET 3000
1)
Place the Forward/Reverse switch in the center
“OFF”
position (neutral).
2) Turn the Start switch OFF.
3)
Confirm the automatic park brake is set.
4) Place blocks under the front or rear wheels to
prevent vehicle movement.
5) Disconnect the battery main positive and negative
cables or disconnect the main battery plug.
Do not allow the wires to rotate while removing
terminal hardware.
Internal electrical connection will be damaged if the
terminal stud rotates.
INSPECT
Receptacles
The inside of each receptacle should be clean and free
of any debris. Use aerosol electrical cleaner if required.
Base Plate
The base plate should be flat. If required, sand with 150
wet sandpaper to remove any raised areas.
Terminal Ends
The wire insulation at each terminal should be smooth
and free of any sign of heat. Any indication of heat is a
result of a loose connection at the terminal. This could
have been a loose bolt or a faulty crimp. It is recommend
to replace the cable terminal end.
Note: A loose bolt could result in damaging the
terminal crimp.
REMOVE/INSTALL
It may be required to remove the control panel from the
vehicle for this procedure.
Remove
6: Turn the start switch OFF.
7: Disconnect the batteries.
8: While holding the wires so that they do not rotate,
remove the terminal bolts.
9: Disconnect the logic connector.
10: Remove the four bolts holding the controller to
the panel and remove the controller.
Note: If a heat sink is installed, then these bolts
may also hold the heat sink to the panel.
Install
1: Thoroughly clean the controller base, mounting
plate, and heat sink.
2: Apply thermal transfer compound to the controller
base and heat sink.
3: Install the controller to the mounting plate.
4: Attach the wires to the studs and torque per
specification listed in the table at the end of this
section.
Note: DO NOT allow the wires to rotate while
torquing the bolts (see notice above).
5: Install silicon dielectric grease (94-422-10, 5.3
ounce tube) into the harness receptacle and
reconnect to the controller.
6: Reconnect the batteries and test drive.
TROUBLESHOOTING
Troubleshooting control system is not included in this
manual.
All electrical troubleshooting information is included in
a separate manual “Troubleshooting Electric Vehicles”.
The manual part number is M7-001-69 and was provided
on the original vehicle CD. A hard copy can be purchased
from your authorized Taylor-Dunn distributor or can be
downloaded from the Taylor-Dunn web site.
These motor controls are programmed to match the
vehicle configuration.
DO NOT move a control to another vehicle unless the
vehicle configurations are identical.
Any changes to the vehicle configuration may require
reprogramming the controller.
Installing a controller that is not programmed
correctly may result in damage to the controller or
electrical system.
NOTICE
Summary of Contents for ET 3000
Page 2: ......
Page 6: ...Notes...
Page 14: ...Notes...
Page 128: ...Notes...
Page 136: ...Battery Page 8 MB T48 02 T 48 AC ET 3000 Notes...
Page 138: ...Notes...
Page 142: ...Motor Controller Page 4 MB T48 02 T 48 AC ET 3000 Notes...
Page 148: ...Illustrated Parts Page 4 MB T48 02 T 48 AC ET 3000 Batteries...
Page 152: ...Illustrated Parts Page 8 MB T48 02 T 48 AC ET 3000 Front Brake...
Page 156: ...Illustrated Parts Page 12 MB T48 02 T 48 AC ET 3000 Brake Lines...
Page 162: ...Illustrated Parts Page 18 MB T48 02 T 48 AC ET 3000 Cargo Box Rear...
Page 164: ...Illustrated Parts Page 20 MB T48 02 T 48 AC ET 3000 Chargers Lestronic Charger Page 1...
Page 166: ...Illustrated Parts Page 22 MB T48 02 T 48 AC ET 3000 Lestronic Charger Page 2...
Page 170: ...Illustrated Parts Page 26 MB T48 02 T 48 AC ET 3000 Decals...
Page 172: ...Illustrated Parts Page 28 MB T48 02 T 48 AC ET 3000 Door Options...
Page 175: ...Illustrated Parts Page 31 MB T48 02 T 48 AC ET 3000...
Page 188: ...Illustrated Parts Page 44 MB T48 02 T 48 AC ET 3000 Motor...
Page 196: ...Illustrated Parts Page 52 MB T48 02 T 48 AC ET 3000 Steering Gear...
Page 198: ...Illustrated Parts Page 54 MB T48 02 T 48 AC ET 3000 Steering Knuckle...
Page 200: ...Illustrated Parts Page 56 MB T48 02 T 48 AC ET 3000 Steering Linkage...
Page 204: ...Illustrated Parts Page 60 MB T48 02 T 48 AC ET 3000 Transmission Differential Gear Case...
Page 215: ...Notes...