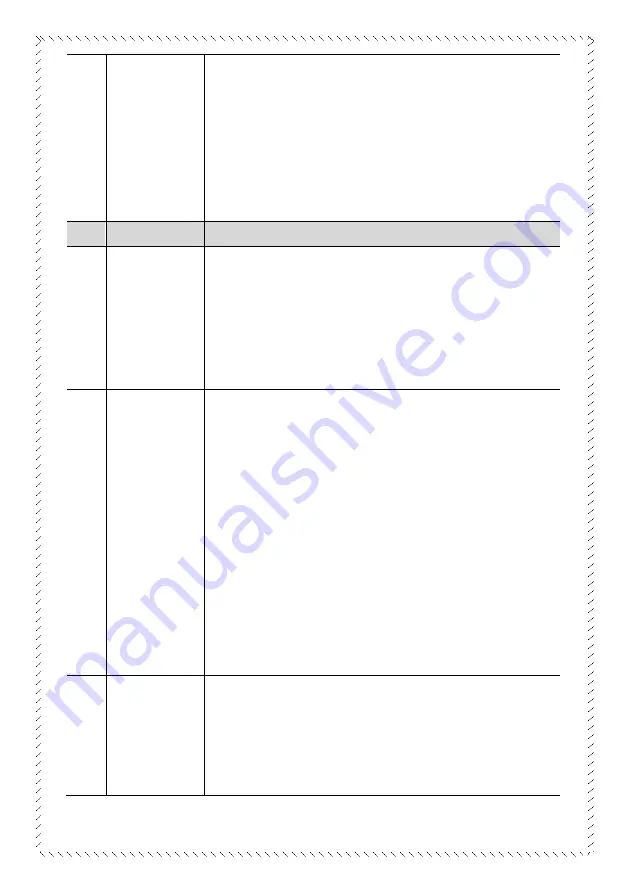
- 25 -
2
Incomplete
penetration
1. Low welding current and uneven wire-feed speed.
2. Arc voltage too low or too high.
3. Inside the beveled edge the welding speed is too
slow or too fast.
4. Beveled gap too small.
5.
Welding wire out of position and not aligned with
the centre of the welding bead.
No.
Imperfect
Root Cause
3
Poor welding
bead
1. Welding parameters unsuitable for the current job.
2. Welding wire out of position and not aligned with
the centre of the welding bead.
3. Centre deviation of wire feed roller.
4. Wire straighteners not properly adjusted.
5.
Loose or worn contact tip.
4
Unstable
welding arc
1. Loose or worn contact tip or too large in diameter
for the wire thickness.
2. Uneven wire spool rotation: excessive wear on
the groove of the drive roll and the pressure from
the tensioner roller not adequate.
3. Too low welding current and fluctuation of arc
voltage.
4. Protruding welding wire outside the the contact tip
too long.
5. Surface pollution of the workpiece from rust, paint
or grease.
6.
The earth cable set not properly connected.
5
Spatter
1. Too large or too small inductance in short circuit
transition.
2. Imbalance between arc voltage and welding
current.
3. Inadequate cleaning of welding wire and material.