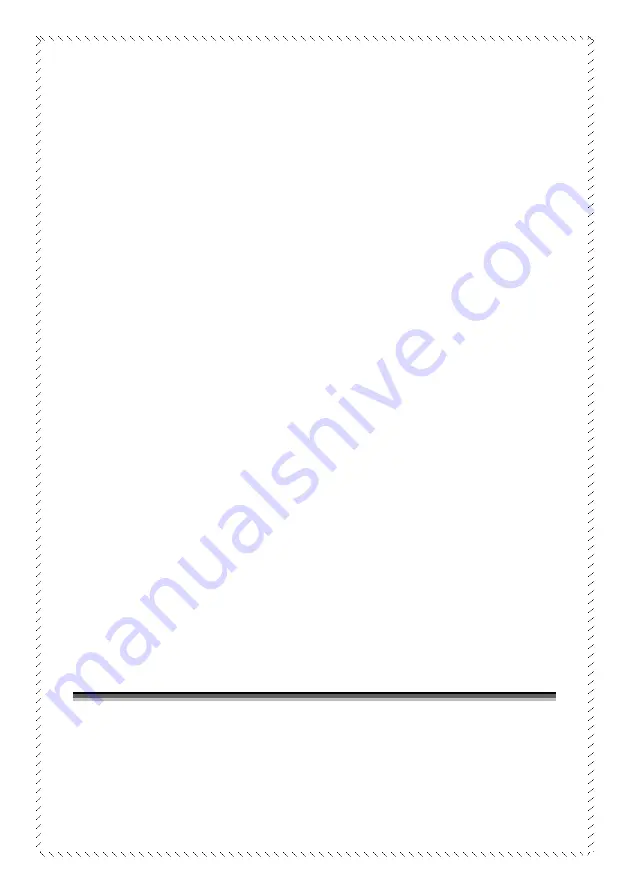
- 25 -
7.1. Blackened Welding Spots
This phenomenon indicates that the welding spot is oxidised owing to insufficient
protection. The following remedial actions can be pursued:
7.1.1. Check the efficiency of gas flow and pressure. As a general rule the
pressure in the cylinder should be above 0.5 mPa. If not, exchange or
refill the cylinder.
7.1.2. Check the gas flow and ensure there is sufficient flow-rate shielding for
the job at hand. The flow-rate should never be below 3 l/min.
7.1.3. Ensure that the gas flow to the torch is unobstructed.
7.1.4. Ensure that the gas being used is correct and of good quality.
7.1.5. Strong air flow in the welding environment may influence gas shielding.
7.2. Difficult Arc Start or Easy Arc Break.
7.2.1. Only use a good quality electrode to meet the requirements for
high-quality welding.
7.2.2. Ensure that electrodes are sufficiently dried. Electrodes with a too high
moisture content will cause arc instability, welding defects and poor
welding quality.
7.2.3. Extended welding cables can cause excessive voltage drop at the torch
end resulting in arc problems.
7.3. The Output Current is Below the Rated Value
Power supply which deviates from the rated voltage, will have a consequential
effect on the output current. Under-power input will result in under-power output.
.
Maintenance
Safe operation of the machine is dependent on regular maintenance and the
replacement of worn and defective parts where necessary.
Summary of Contents for MIG-250TD
Page 32: ...31 4 Circuit Diagram...