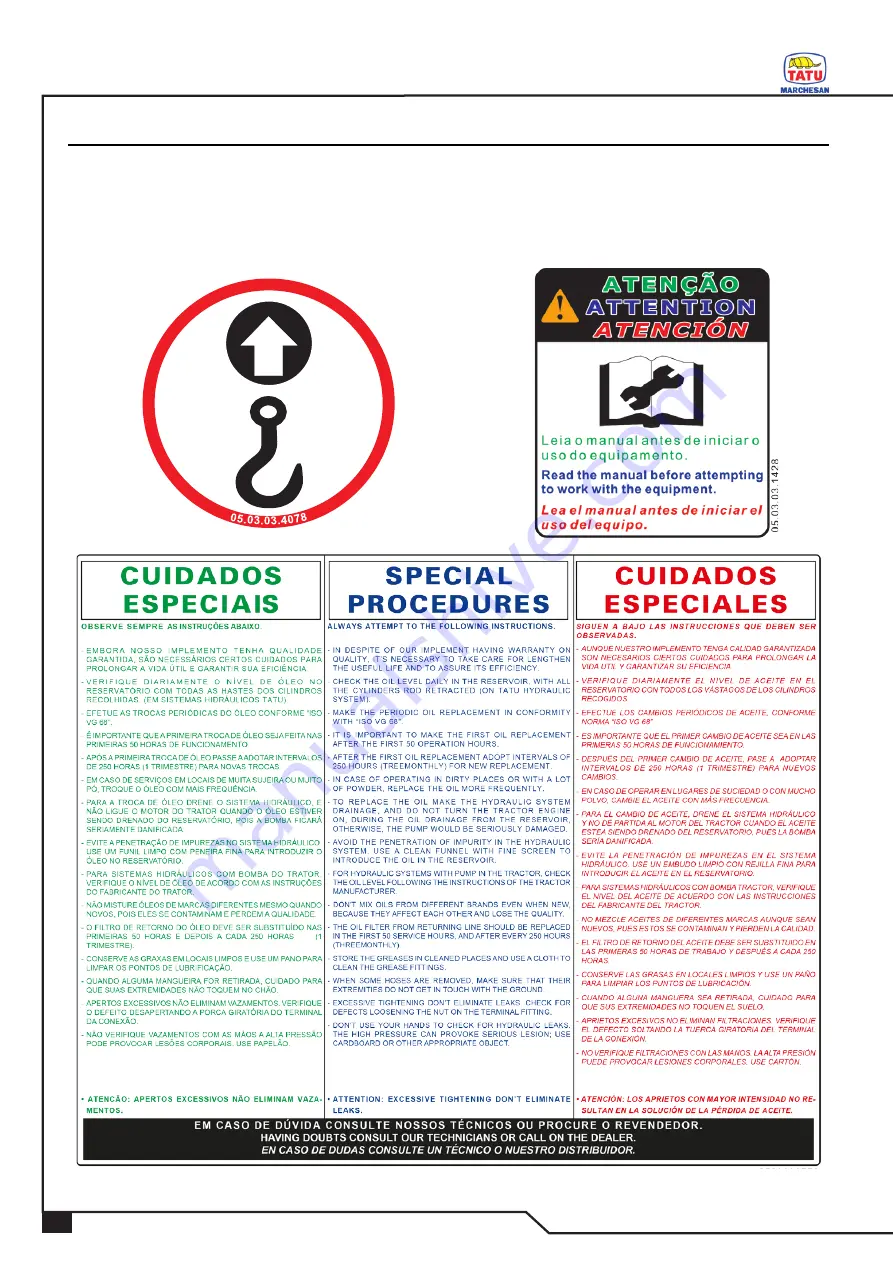
14
PD / PCA / PCA PLUS - Rev. 01 - Jun/22
2. To the operator
Safety decals
The safety decals warn about the equipment points that require more attention and
they should be kept in good repair. If these decals become damaged or illegible, replace
them. Marchesan provides decals, upon request and indication of the respective serial
number.