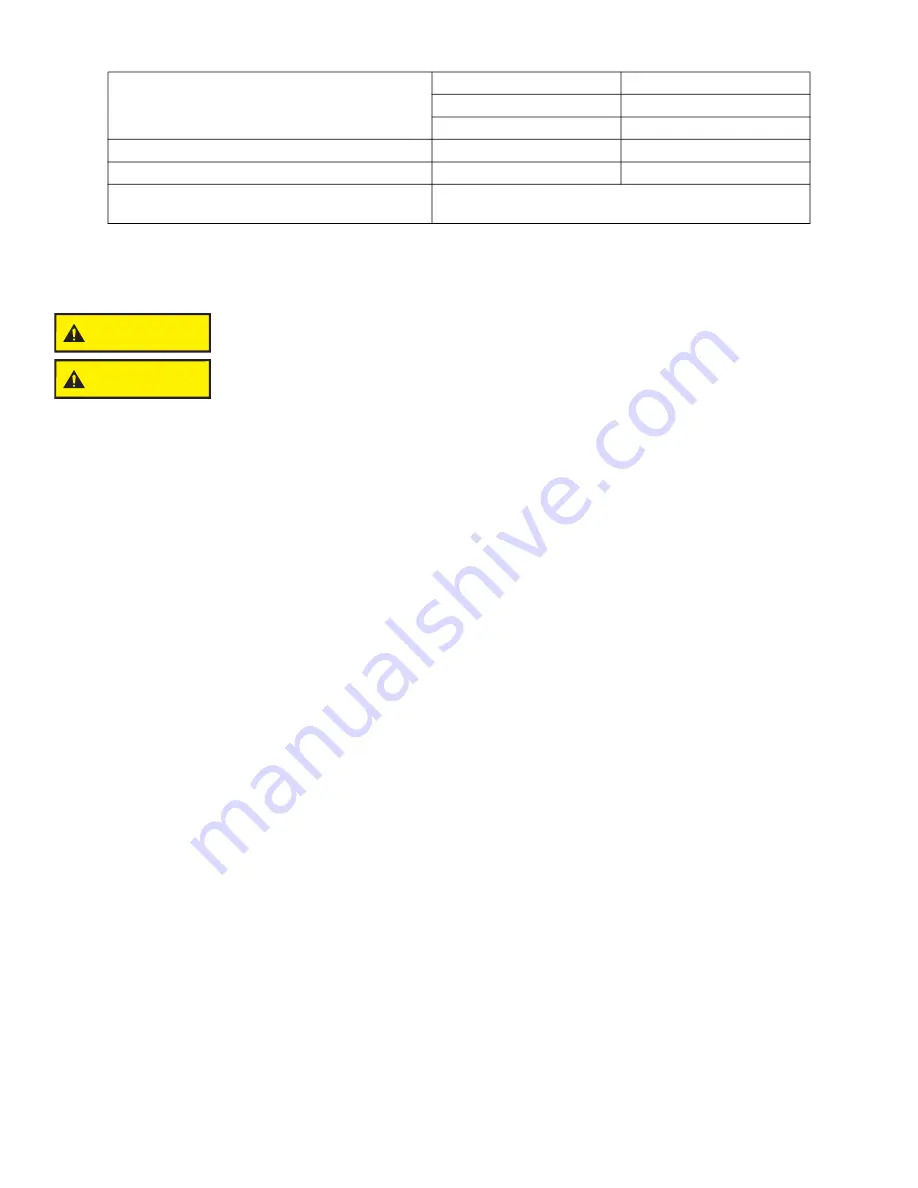
©Copyright Task Force Tips LLC 2002-2020
5
LIN-040 November 30, 2020 Rev15
3.2 SPECIFICATIONS
Table 3.2
3.3 NOZZLE COUPLINGS
NH (National Hose Threads) threads are standard on all nozzles. Other threads such as NPSH (National Pipe Straight Hose) may be
specified at time of order.
3.4 USE WITH SALT WATER
Use with salt water is permissible provided the equipment is thoroughly cleaned with fresh water after each use. The service life of the
equipment may be shortened due to the effects of corrosion, and is not covered under warranty.
Maximum operating pressure (with valve shut
off)
Metro 0 - 580 psi
40 bar
Metro 1 - 300 psi
21 bar
Metro 2 - 300 psi
21 bar
Operating temperature range of fluid
33 to 120° F
1 to 50° C
Storage temperature range
-40 to 150° F
-40 to 65° c
Materials used
Aluminum 6000 series hard anodized MIL8625 class 3 type
2, stainless steel 300 series, nylon 6-6, nitrile rubber
CAUTION
Mismatched or damaged waterway connections may cause equipment to leak or uncouple under
pressure. Failure could result in injury. Equipment must be mated to matched connections.
CAUTION
Dissimilar metals coupled together can cause galvanic corrosion that can result in the inability to
uncouple the connection, or complete loss of engagement over time. Failure could cause injury. Per
NFPA 1962, if dissimilar metals are left coupled together, an anti-corrosive lubricant should be
applied to the connection and the coupling should be disconnected and inspected at least
quarterly.