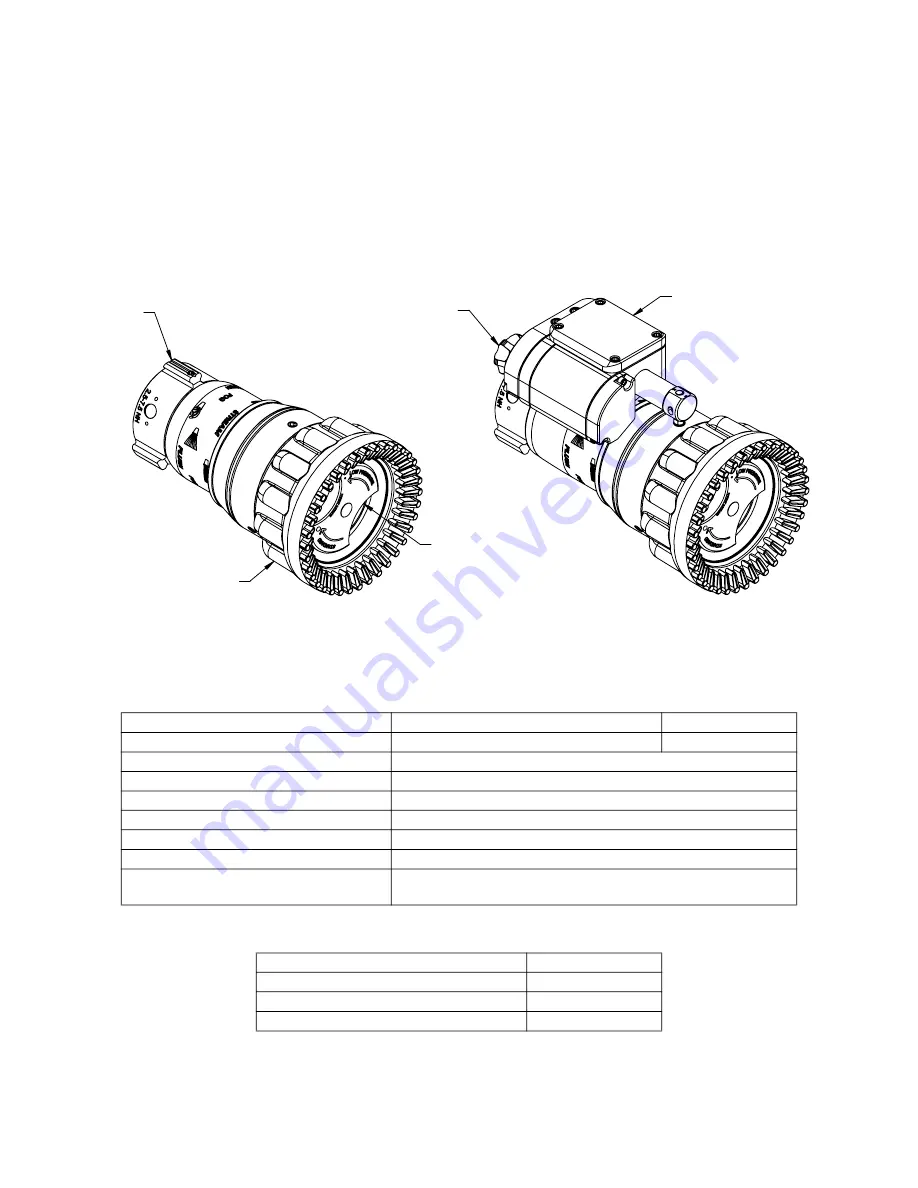
©Copyright Task Force Tips LLC 2020
6
LIM-027 December 15, 2020 Rev00
3.0 GENERAL INFORMATION
The Task Force Tips Master Force series automatic nozzles operate by sensing the pressure at the nozzle inlet and adjusting the
discharge opening to maintain a constant pressure throughout the flow range of the nozzle. The Master Force operates at either a
standard or low pressure as selected by the nozzle operator.
The Master Force are deluge nozzles with clean, far reaching straight stream capability. Stream pattern can be varied from straight
stream to a dense, wide fog pattern. Turning the shaper past the wide fog setting allows flushing the nozzle of debris without shutting
down flow. The Master Force nozzles are intended for use on fixed or portable monitors.
3.1 VARIOUS MODELS AND TERMS
Master-Force nozzles are available in several different models and inlet connections. Basic body styles are shown below.
Figure 3.1
3.2 MECHANICAL SPECIFICATIONS
Table 3.2
3.3 ELECTRICAL SPECIFICATIONS
Table 3.3
Manual Version
ER Version
Weight
9.5 lbs (4.3kg)
14.2 lbs (6.4kg)
Flow Range
300 - 800 GPM (1100 - 3000 L/min)
Operating Pressure (Standard Mode)
100 psi (7 bar)
Operating Pressure (Low Mode)
55 psi (3.7 bar)
Maximum fog angle
103°
Operating temperature range of fluid
33 to 120°F / 1 to 50°C
Storage temperature range
-40 to 150°F / -40 to 65°C
Materials used
Aluminum 6000 series hard anodized MIL8625 class 3 type 2,
stainless steel 300 series, nylon 6-6, nitrile rubber
Nominal Operating Voltage
12 or 24 VDC
Maximum Voltage
32 VDC
Minimum Voltage - 12 Volt System
9 VDC at monitor
Minimum Voltage - 24 Volt System
18 VDC at monitor
(50RWRU$VVHPEO\
0DQXDO2YHULGH.QRE
(59HUVLRQ
6WDQGDUG/RZ
3UHVVXUH.QRE
&RXSOLQJ
6WUHDP6KDSHU
0DQXDO9HUVLRQ