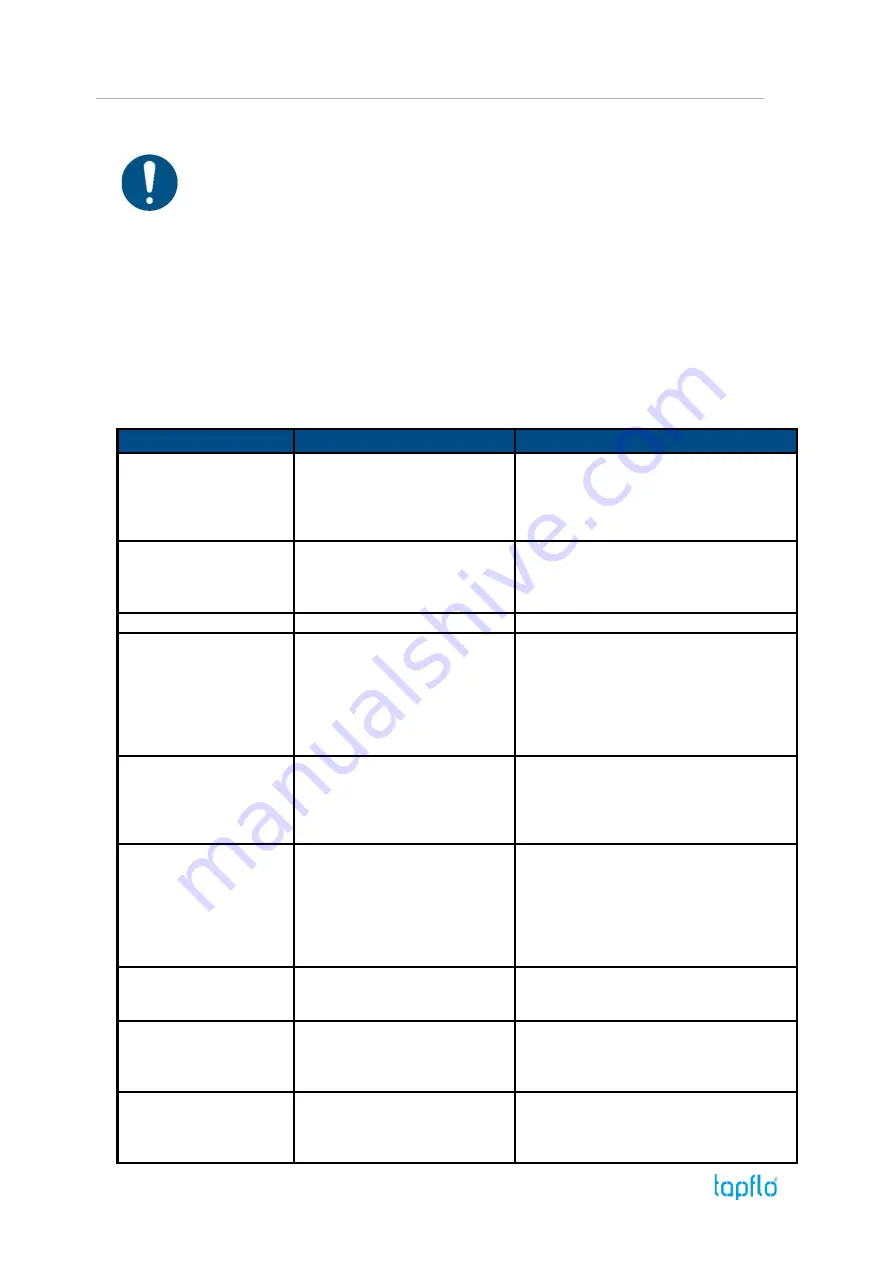
3.
MAINTENANCE
IOM manual Tapflo Hose pumps
18
3.4.
Complete inspection
The intervals for a complete inspection depend upon the operation conditions of the pump.
The characteristics of the liquid, temperature, materials used in the pump and running time
decide how often a complete inspection is necessary.
Nevertheless, Tapflo recommends to inspect the pump at least once a year.
If a problem has occurred, or if the pump is in need of a complete inspection, refer to
chapters
3.5 "Location of faults"
and
3.6
"Disassembly of the pump"
. You are of course warmly
welcome to consult Tapflo for further help.
Parts that are subject to wear should be kept in stock, see our recommendations in chapter
4.7
3.5.
Location of faults
PROBLEM
POSSIBLE ISSUE
POSSIBLE SOLUTION
Pump does not run
Lack of power supply
Check if the motor is connected properly
Check if power supply is ON
The rotor is stalling
Check the fixing of the hose
Check if the discharge pressure is not too high
Check if particles are not blocking the hose
The suction is bad
Suction connection is not tight
Tighten the suction line
Suction connection is blocked
Clean suction line
Hose is blocked or damaged
Check for any debris inside the hose
Air in suction / discharge line
Vent suction / discharge line
The pump runs irregular
Hose is blocked or damaged
Check for any debris inside the hose
Bad flow/pressure
Wrong set-up of the rollers
Check and adjust if necessary
Suction blocked
Check / clean suction connection
Pressure losses on suction side
Check/change installation on suction side
Too viscous liquid
Check if pump speed is proper for viscosity
Air in liquid
Seal suction line; check / refill container
Hose is blocked or damaged
Check for any debris inside the hose, replace hose
if necessary
Liquid leaks from the pump
Screws on the pump not properly
tightened
Shaft seal or seal ring worn
Tension / stress form the installation
Check tightening torques of the screws
Replace if necessary
Adjust installation, eliminate stress, when using a
dampener provide separate support for it.
Hose life is too short
Wrong selection of material
Long periods of dry running
Too high discharge pressure
Too high speed
Wrong set-up of the rollers
Too high liquid temperature
Contact us for information on material selection
When dry, run pump slowly (see chapter 2.2)
Check if pump rated pressure is not exceeded
Check if the discharge line is not blocked
Reduce the pump speed
Check and adjust if necessary
Contact us for information on material selection
Overheating of motor
Flow rate too high
Liquid parameters different than
calculated
Reduce the flow / rotation speed of the motor
Check pumped liquid parameters
Overheating of the pump
Flow rate too high
Liquid temperature too high
Foreign objects in the liquid
Pump is not filled with liquid
Reduce the flow / rotation speed of the motor
Cool the liquid
Use a filter on the suction side
Fill pump with liquid
Noise and vibration
The pump sucks air
Suction pipe is blocked
Flow rate too high
Loads on the pipes
Make sure all connections are tight
Check pipes / valves and filters on suction line
Reduce the flow / rotation speed of the motor
Connect the pipes independent of the pump
Summary of Contents for PTL 13
Page 45: ......