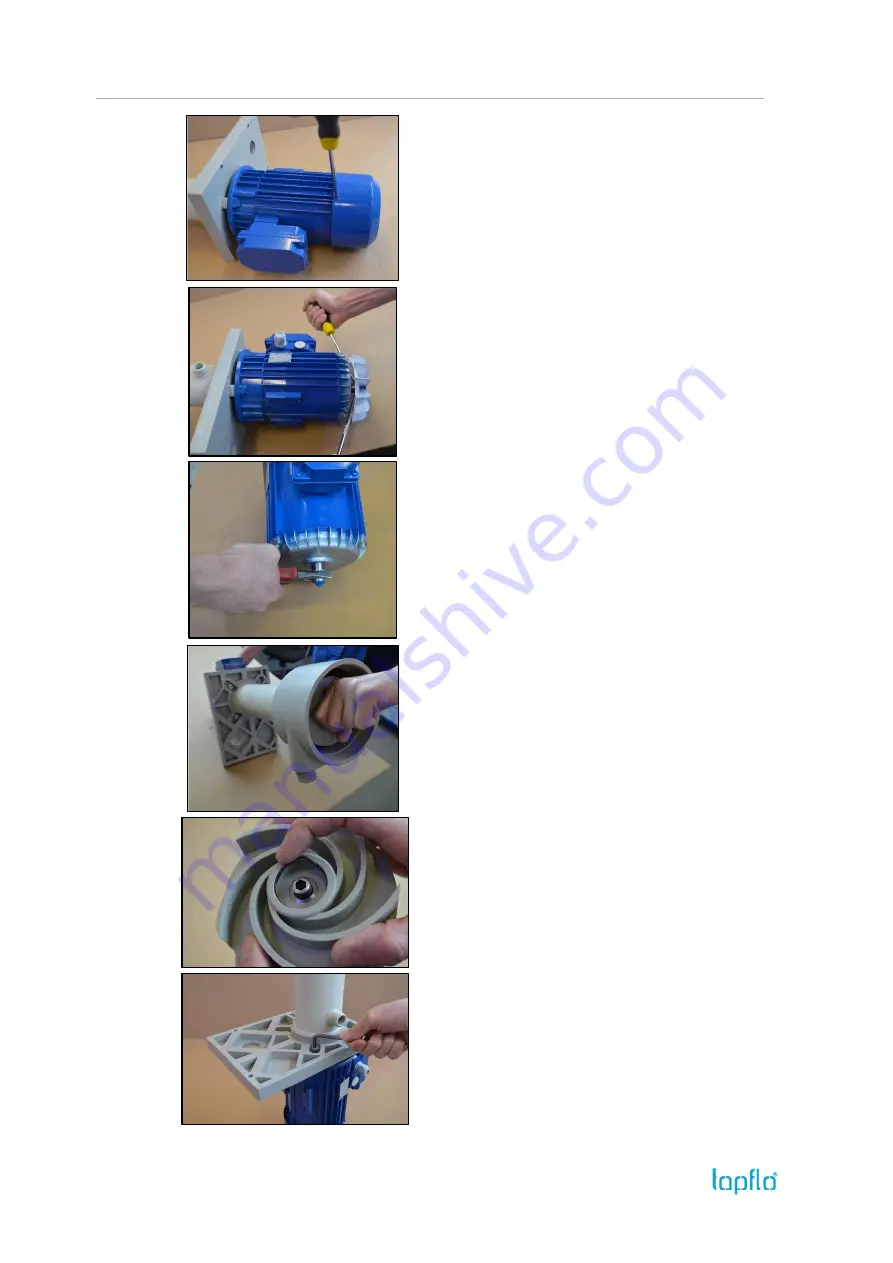
3.
MAINTENANCE
IOM manual CTV vertical centrifugal pumps
16
Fig. 3.3.1.4
Remove the motor fan cover from the electric motor
and then remove the motor fan.
Fig 3.3.1.5
Secure the free end of the motor shaft using universal
pliers or similar.
Fig 3.3.1.6
Unscrew the impeller.
Fig 3.3.1.7
Remove the impeller O-ring [193] from the impeller.
Fig 3.3.1.8
Unscrew the motor mounting screws [121] and
washers [122] and carefully pull the pump casing unit
[11] from the motor/shaft assembly.
Summary of Contents for CTV Series
Page 38: ......