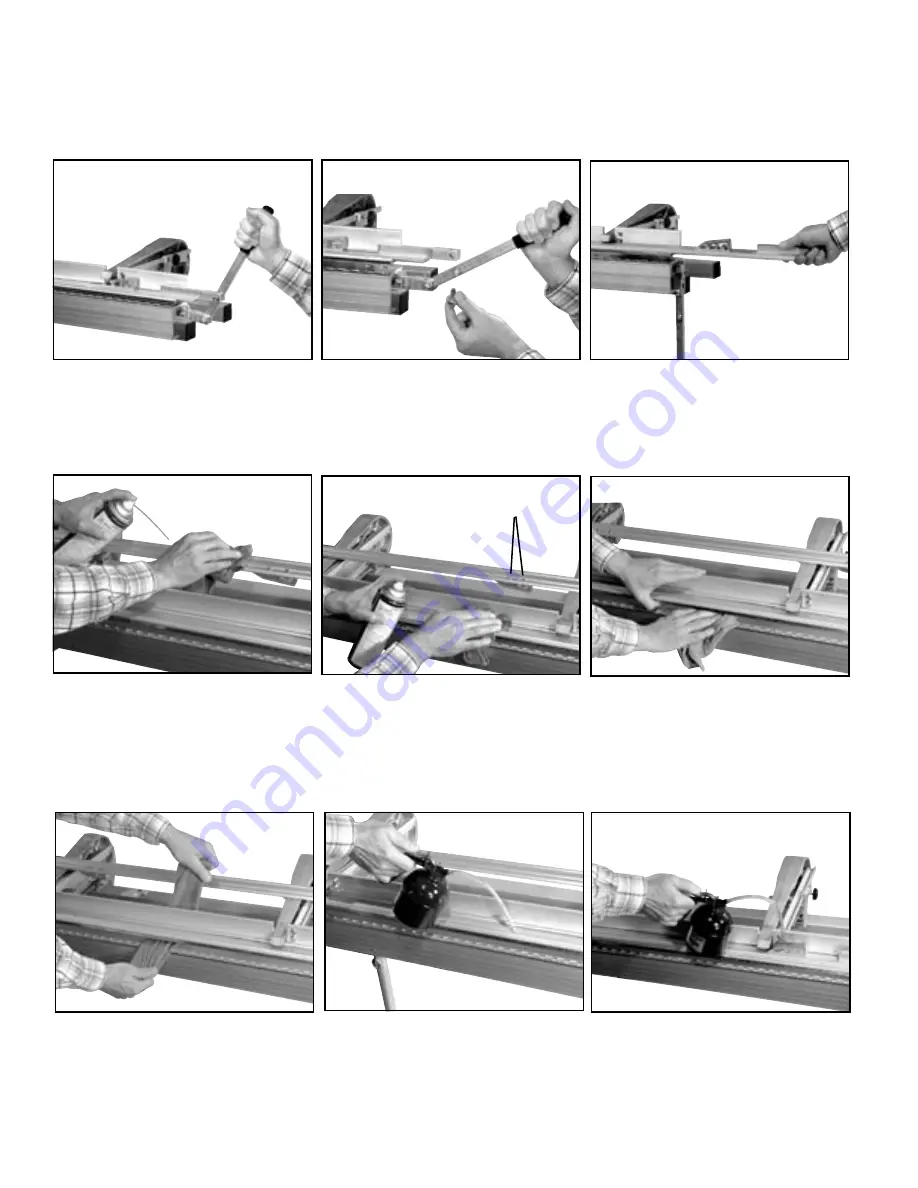
8
Clean Underneath Clampin
Surfaces
Using solvent on a shop rag, clean upper
and lower clamping surface as indicated
and wipe dry. Do not apply oil here.
6
Replace Sliding Bar & Oil Wedges
Replace Sliding Bar making sure that
it slides easily along the Clamping Bar.
Wipe up excess oil. Clean and oil the
Wedges now and regularly thereafter.
9
CLEANING THE LOCKING AND CLAMPING SURFACE
Open Brake
Move Locking Handle to Right. Follow
steps 1, 2, and 3 in reverse order to
reassemble.
Remove Top Yoke Pin
With Brake unlocked remove Cotter
Pin from Top Yoke Pin and disengage
handle.
Remove Sliding Bar
Grasp and pull Sliding Bar to the right
and forward to remove. Turn upside
down and rest on brake castings.
Loosen Dirt and Residue
Use Gum-Out
®
, WD-40
®
or quality
commercial cleaning solvent on a clean
shop rag and clean the bottom surface
of the Sliding Bar.
Clean Clamping Bar
Clean the bottom surface of the Clamp-
ing Bar in the same manner. Before
reinstalling check that screws securing
wedges are tight.
1
2
3
4
5
Tools needed: clean shop rag, commercial cleaning solvent such as Gum Out
®
or WD-40
®
, light weight oil
Wedge
Screws
Oil Clamping Bar
Using any lightweight oil such as
“3 in 1”
®
or 30 Wt. motor oil, lightly
lubricate the Clamping Bar.
Note
:
Do not use
graphite, silicone or
heavy grease as these “hold” dirt.
8
“Spot” Cleaning
For everyday cleaning, a rag may be
used between the clamping surfaces
with the Brake assembled.
7