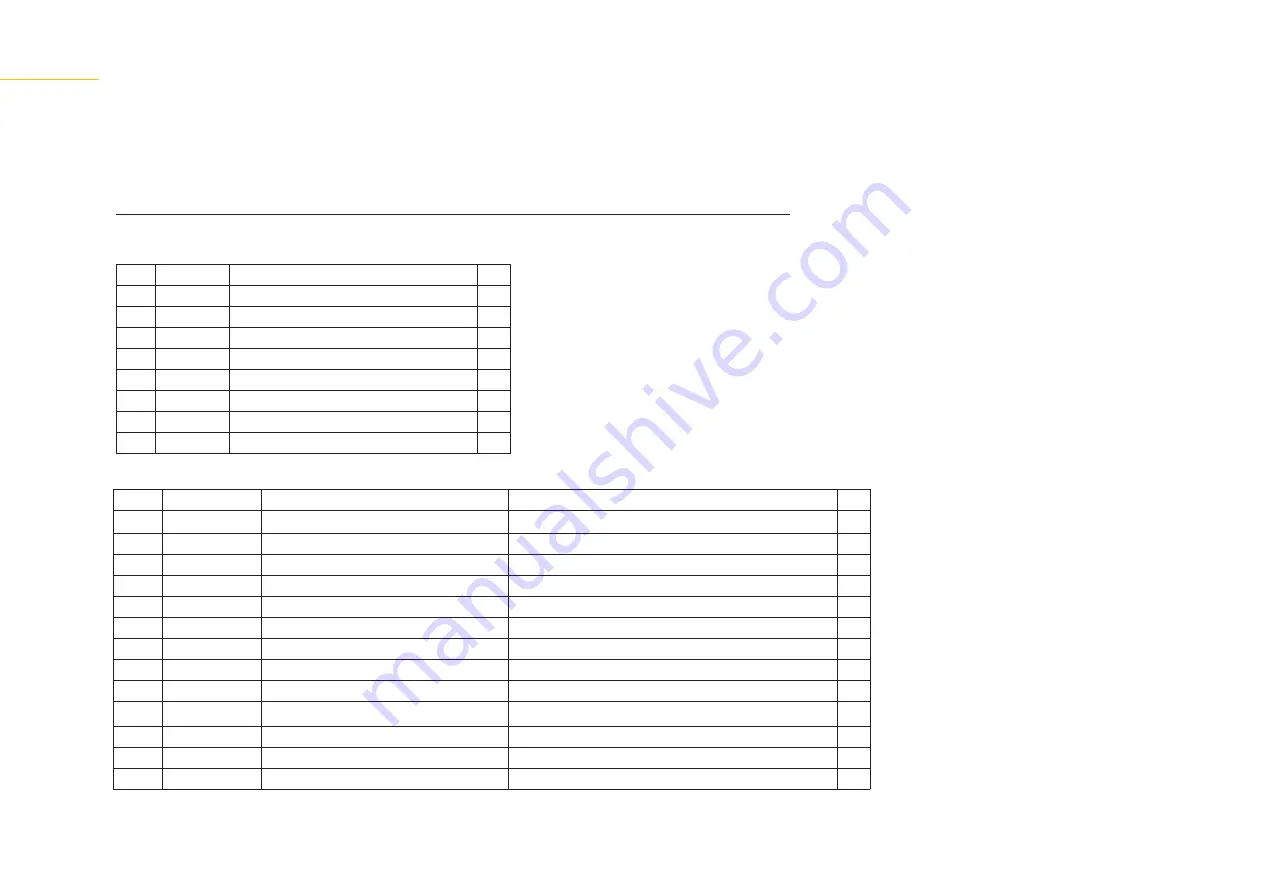
ELECTRO-
HYDRAULICS
Hydraulic Components
Pos.
Part No.
Designation
Qty
1.1
2008250
A100EH Control Valve
1
2.1
1308075
In-line FIlter with Bypass and Indicator
1
3.1
1208250
3 Way Pressure Compensated Flow Regulator
1
4.1
2008151
Table Drive Motor
1
5.1
Z01-03-1046 3/8" Speed control valve
1
6.1
2008010
Tip Cylinder
1
7.1
2008020
Load Ram
1
8.1
2008030
Cut & Start Cylinder
1
Pos.
Part No.
Designation
Qty
101
Hydraulic Hose
3/8" x 2490mm 90°|90°
From: Main Valve to Load Ram (Pull)
1
102
Hydraulic Hose
3/8" x 2640mm 90°|90°
From: Main Valve to Load Ram (Push)
1
103
Hydraulic Hose
1/4" x 3075 Straight | 90°
From: Main Valve to Tip Cylinder (Push)
1
104
Hydraulic Hose
1/4" x 3000mm Straight | 90°
From: Main Valve to Tip Cylinder (Pull)
1
105
Hydraulic Hose
1/2" x 650mm Straight | 90 °
From: Filter to Speed COntrol Valve
1
106
Hydraulic Hose
1/4" x 2800mm 1/4" Straight | 1/4" Long Banjo
From: Table Gearbox Coupling to Cut & Start
1
107
Hydraulic Hose
3/8" x 800mm 90° | 90° (315°)
From: Main Valve to Speed Control Valve
1
108
Hydraulic Hose
3/8" x 2900mm 90° | 90° (270°)
From: Table drive motor to Fast Speed adjustment valve
1
109
Hydraulic Hose
3/8" 400mm 90° | 90° (90 °)
From: Flow Control Valve to Main Control Valve (Back to Tank)
1
110
Hydraulic hose
3/8" x 3150mm 90° | 90°
From: Restrictor valve to Table drive motor
1
111
Hydraulic Hose
1/4" x 3100mm 90° | Banjo (90°)
From: Main Valve to Gearbox Coupling
1
112
Hydraulic Hose
1/2" x 2050mm Feed | Straight
From: Main feed hose to inlet Filter
1
113
Hydraulic Hose
1/2" x 2300mm Return | 90°
From: Main return Hose Port (T)
Hydraulic Hoses
A100 EH Operator’s Manual
38 //
49