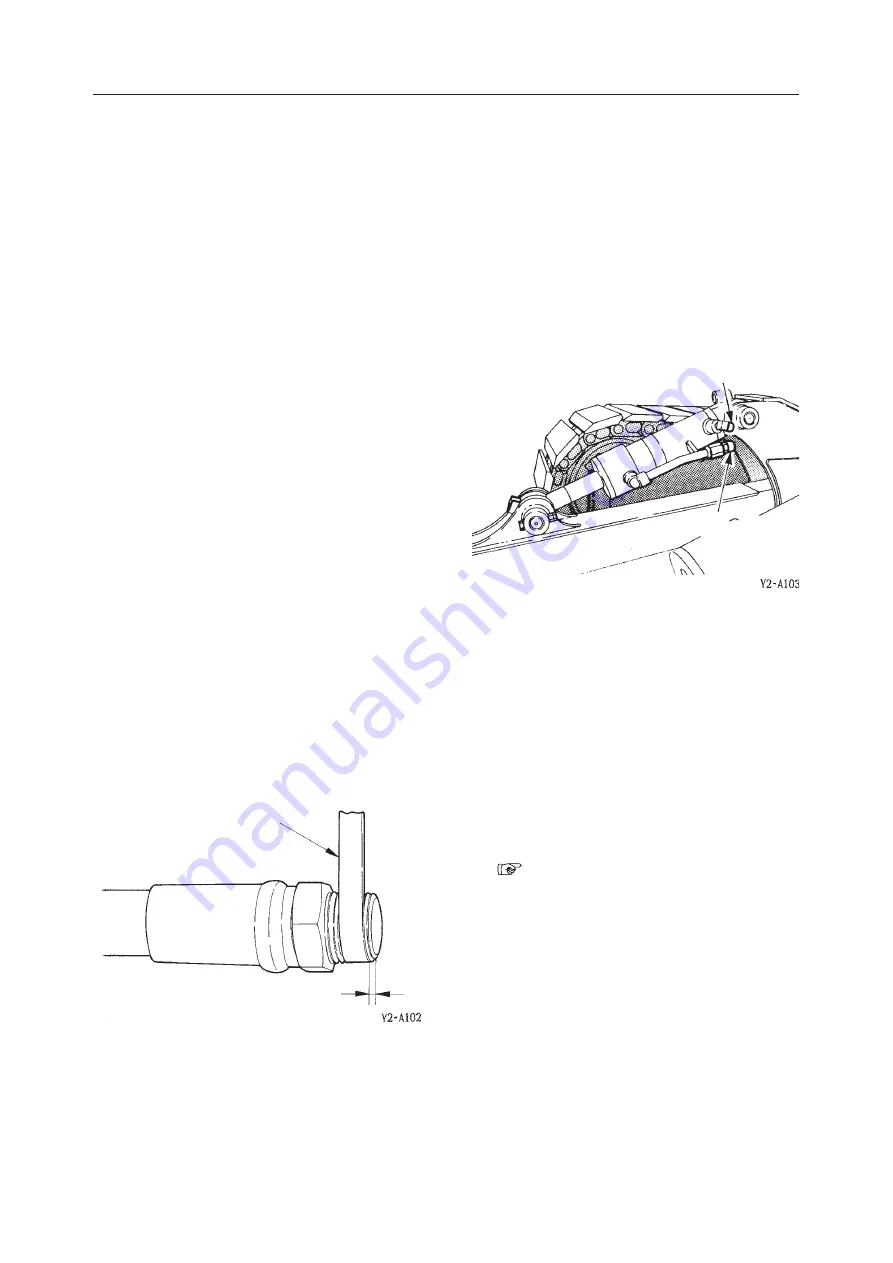
GENERAL
I-9
REV. 1
CAUTIONS DURING REMOVAL AND
INSTALLATION OF THE HYDRAULIC UNITS
1. Make sure that the temperature of the hydraulic
oil has dropped.
2. To prevent a loss of flow of the hydraulic oil, the
residual pressure in the piping and the internal
pressure in the hydraulic tank should be released.
3. Be sure to install caps or plugs on all openings in
the hydraulic unit to prevent dirt from getting into
the unit through the openings.
4. It is easy to mistake hydraulic oil adhering to the
hydraulic unit for an oil leak, so wipe the unit off
thoroughly.
5. Be sure that no damage is done to the plating on
the rod in the hydraulic cylinder.
6. As a rule, removal and installation of the hydrau-
lic cylinder should be done with the rod fully
retracted.
7. Be sure to bleed the air after replacing the hydrau-
lic oil or removing any of the hydraulic devices.
“III. Machine Configuration, Hydraulic Sys-
tem”
CAUTIONS DURING DISASSEMBLY AND
ASSEMBLY
1. Clean the machine before disassembly operation.
2. Before disassembly, check the machine condi-
tions and record them.
• Model, Machine Serial Number, Hourmeter
• Reason for Repairs, Repair History
• Dirtiness of Filters
• Fuel and Oil Conditions
• Damage to each parts, etc.
3. To make reassembly operations easy, make match-
ing marks at the necessary points.
4. Clean all disassembled parts and new parts, then
arrange them in the proper sequence.
5. Be sure to replace all seals and cotter pins, etc.,
with new parts.
6. Keep parts which should not come in contact with
oil and water separate from parts with oil on them.
• Electrical Parts, Rubber, V-Belts, etc.
7. When installing bearings, bushings and oil seals,
as a rule, use a press. When a hammer, etc., is
used, it leaves bruises.
8. Wipe all joining surfaces clean so that there is no
dirt or dust adhering to them.
9. Wrap seal tape from the front end, Wrapping it
tight and leaving 1 or 2 threads bare, Overlap the
tape by about 10 mm.
10. When fitting the snap rings, the bigger, rounder
side of their circumferences should face the mat-
ing surfaces.
SEALING TAPE
LEAVE 1 OR 2 THREAD MARGIN
PLUG
PLUG
Summary of Contents for TL130
Page 1: ...0 1 REV 1 ...
Page 7: ...I 1 I GENERAL ...
Page 20: ...I 15 II SPECIFICATIONS II 1 ...
Page 27: ...BUY NOW Then Instant Download the Complete Manual Thank you very much ...