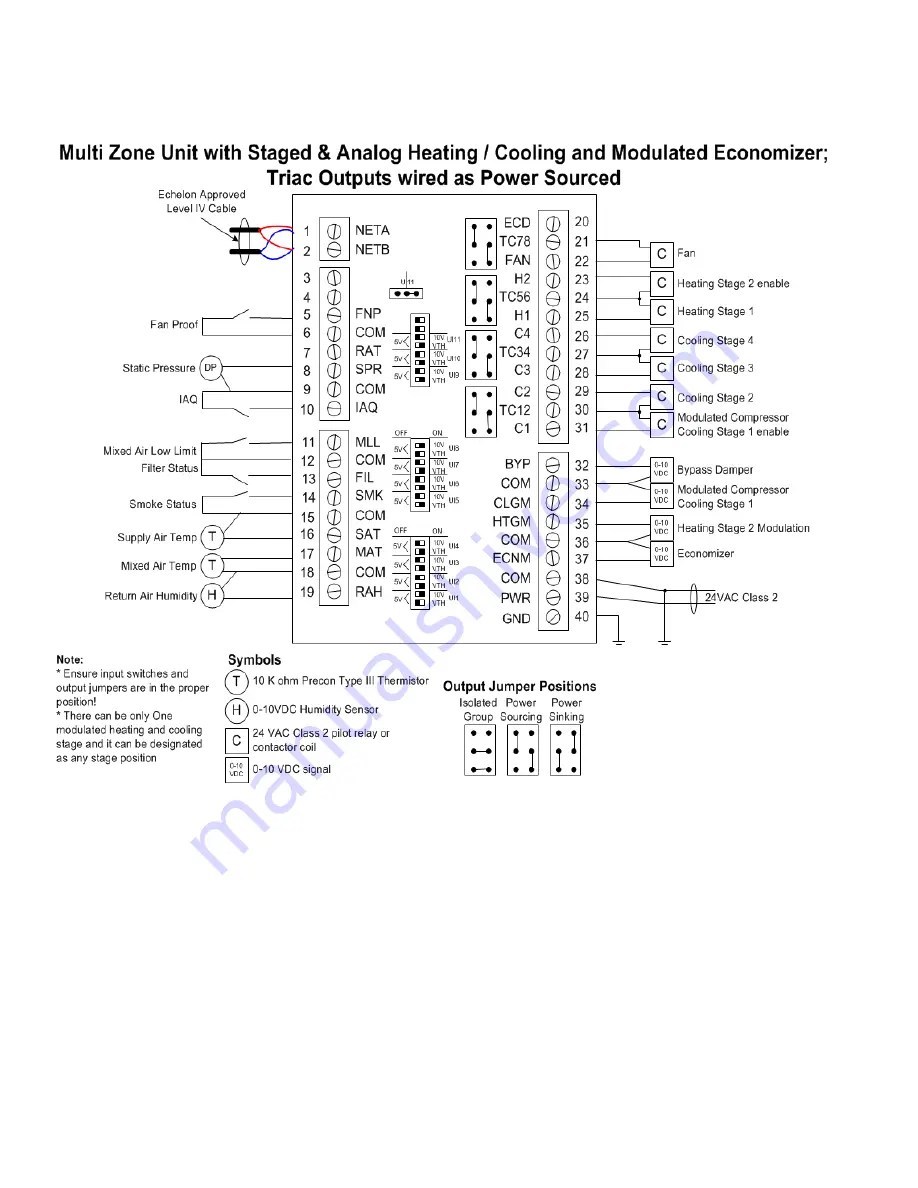
iWorx® MPU2
10
505-009, Effective: April 28, 2014
© 2014 Taco Electronic Solutions, Inc.
Figure 4: Typical MPU2 Wiring - Example C
Connecting Input Devices
Return Humidity (RAH)
To connect the Return Air Humidity sensor to the unit, connect the positive wire from the sensor to RAH (T19) and the
other wire to the adjacent common (T18). The sensor must be of the 0-10 Volt type.
If global indoor air humidity readings are being provided over the network, it is not necessary to attach a return air
humidity sensor directly to the MPU2.