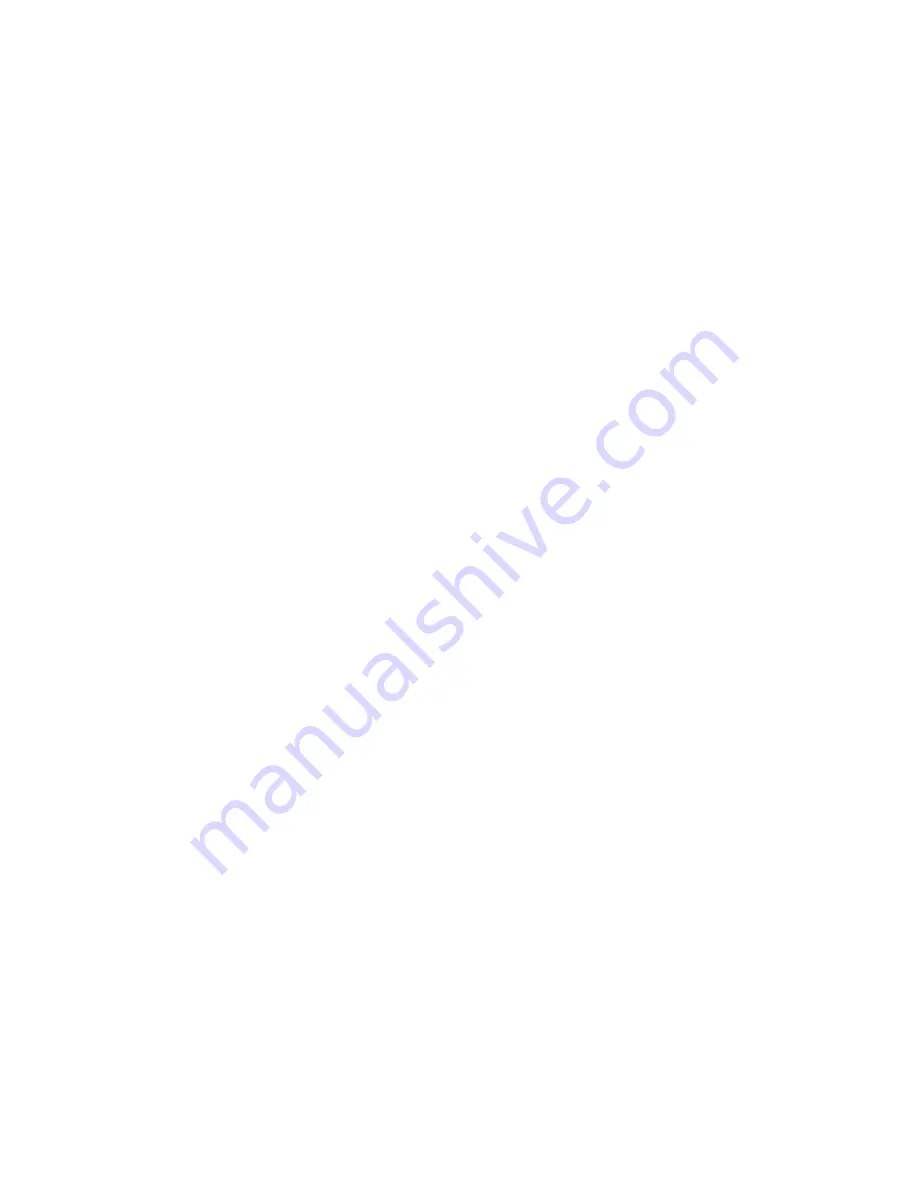
iWorx® MPU2
505-009, Effective: June 30, 2015
17
© 2015 Taco Electronic Solutions, Inc.
If configured for modulated analog output (valve or variable speed circulator) the cooling output position is calculated
by a P + I control loop based on the supply temperature and the cooling setpoint. As the temperature increases above
the cooling setpoint, the cooling output will be modulated open. The cooling output will be modulated closed as the
temperature decreases below the cooling setpoint.
The heating output (valve or variable speed circulator) position is calculated by a P +I control loop based on the supply
temperature and the heating setpoint. As the temperature decreases below the heating setpoint, the heating output will
be modulated open. The heating output will be modulated closed as the temperature increases above the heating set-
point.
If configured for a floating point valve control, the cooling valve is calculated by a P + I control loop based on the supply
temperature and cooling setpoint. As the temperature increases above the cooling setpoint, the valve will be modulated
open. The valve will be modulated closed as the temperature decreases below the cooling setpoint.
If configured for a floating point valve control, the heating valve is calculated by a P + I control loop based on the supply
temperature and cooling setpoint. As the temperature decreases below the heating setpoint, the valve will be modu-
lated open. The valve will be modulated closed as the temperature increases above the heating setpoint.
In both the heating and cooling modes, the supply air temperature setpoint may be reset by the greatest zone temper-
ature.
The controller optionally has the capability of monitoring the supply air temperature to determine if the heating and
cooling are operating properly. During the cooling mode, if the supply air temperature fails to drop below the cooling
operational limit after a pre-determined time period, the cooling stages shut down and a cooling failed alarm is reported
to the LCI.
During the heating mode, if the supply air temperature fails to rise above the heating operational limit after a pre-deter-
mined time period, the heating stages shut down and a heating failed alarm is reported to the LCI.
As a safety device, the controller can optionally monitor the supply air temperature to determine if the heating stages
have failed on. If the supply air temperature rises above the heating high limit setpoint, the fan energizes. If the supply
air temperature does not drop below the setpoint after a pre-programmed time delay, the bypass damper is overridden
closed. A heating high limit exceeded alarm is reported to the LCI and all of the zone controllers.
The controller operates in one of two states: occupied or unoccupied. The LCI determines the active operating mode.
An optional backup schedule is provided for cases when the LCI is not available.
A digital input is provided to monitor the fan proof. If the fan is energized and no air flow is detected after 30 seconds,
the controller turns off all stages of heating and cooling along with the supply air fan. The controller returns to normal
operation after it is reset. An alarm is reported to the LCI when this condition exists.
A digital input is provided on the controller to monitor the status of the air filter. An external pressure switch is wired to
the input to determine when the filter becomes dirty. An alarm is reported to the LCI when this condition exists.
Mixed air low limit protection is provided through a digital input. If a low limit condition exists, the controller turns off all
stages of heating and cooling along with the supply air fan. An alarm is reported to the LCI when this condition exists. If
configured for either analog or floating point valve, the output will open 100% to prevent freezing of the coils. The con-
troller returns to normal operation after it is reset. Following the reset there is a 10 minute delay before the mixed air
low limit is checked again.
The controller monitors the runtime of the cooling stages, heating stages, and fan. When any of the runtimes exceeds
the programmable limit, a maintenance alarm is reported to the LCI.
When the Return Air Humidity rises above the humidity setpoint, dehumidification is enabled by enabling the cooling
stages, if modulated cooling is enabled; the cooling output goes to 100%. Dehumidification is disabled, when return air
humidity drops below the setpoint by 3%.