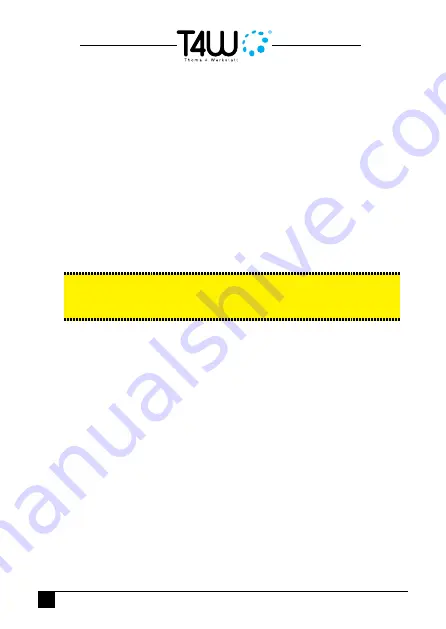
5
Technical Data:
Available nozzle ________________________________________________
1.3mm: No.59474
________________________________________________________________1.4mm: No.59528
________________________________________________________________1.5mm: No.59529
________________________________________________________________1.7mm: No.59530
________________________________________________________________2.1mm: No.59531
________________________________________________________________2.5mm: No.59532
Pressure required _____________________________________________
1-2 bar (10-28 psi)
Air Consumption___________________________________________________
150~280 l/min
Air connection ________________________________________________________
1/4” PS(M)
Net weight ________________________________________________________________
450g
Safety
Never point the tool against people and animals - coating
materials or compressed air may be the cause of injuries. It is
forbidden to use any other gas instead of compressed air.
•
The use of other gases can lead to serious injury, or threaten to cause a fire hazard.
• When connecting the tool to the compressed air system should take into account
the space needed for the hose to prevent damage to the hose or fittings.
• At work should be ensured adequate ventilation. Lack of ventilation
can cause damage to health, or threaten to cause a fire hazard.
•
The tool should be used away from sources of heat and fire, as
this could cause damage to or deterioration of functioning.
• Observe general safety rules when performing work of coating
materials and used appropriately selected personal protective
equipment such as goggles, masks, gloves and overalls.
• Never leave the assembled air system without the supervision of the person
entitled to maintenance. Do not allow children near the assembled air system.
• Supply compressed air under high pressure, can cause kickback
tool in a direction opposite to the direction of ejection of the coating
material. It should be especially careful, because the recoil forces
may, in certain circumstances, result in multiple injuries.
• It is recommended to try the tool before you start. It is recommended that
utility workers are properly trained. This will improve safety significantly.
• Follow manufacturer of coating materials and use them in
Summary of Contents for 59474
Page 1: ...OPERATION MANUAL PIKqXRP ...
Page 9: ......
Page 10: ...Thoma Tel Fax 48 95 741 11 62 info t4w eu www t4w eu ...