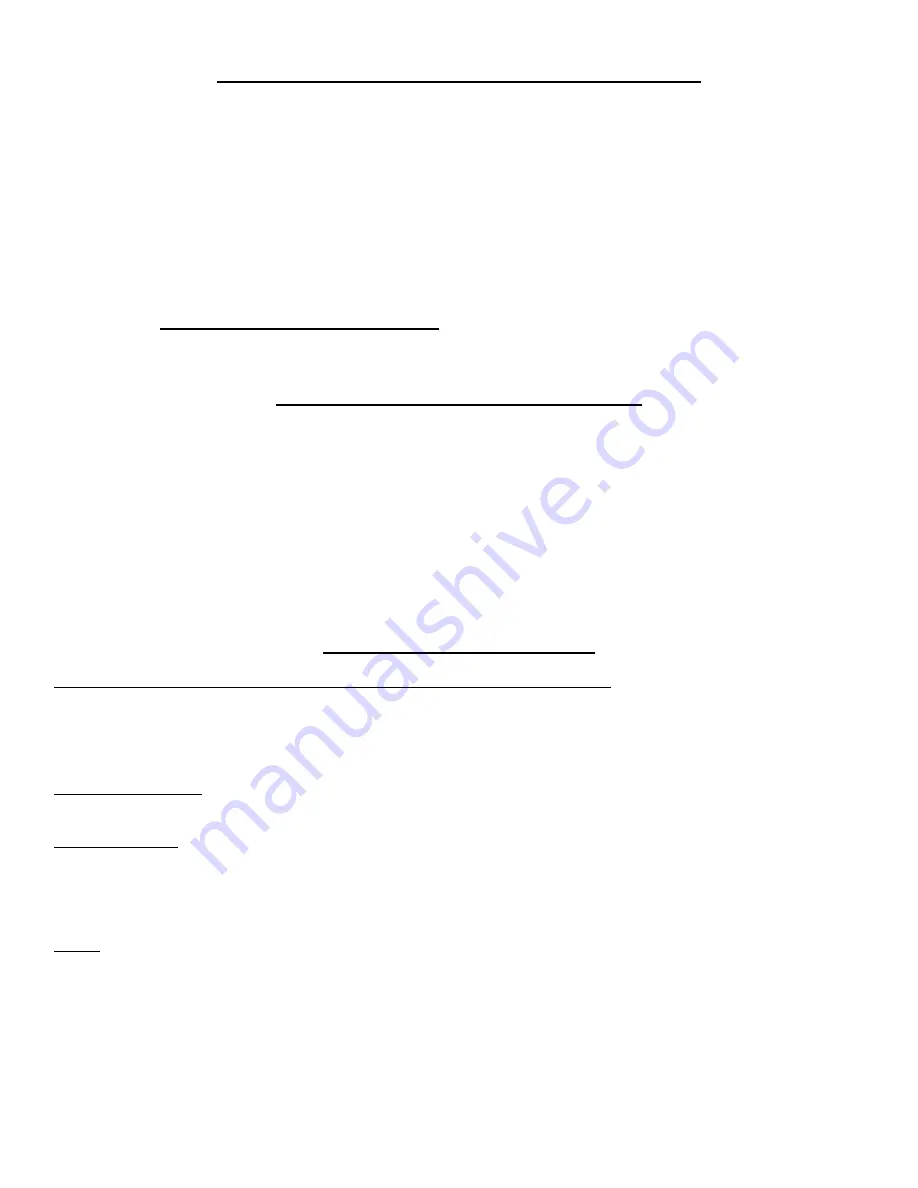
FW-200 HPA, Rev. 4
3-1
CARE AND MAINTENANCE OF WELDING JAWS
Since your welder uses low AC Voltage to weld with, it is critical to keep resistance levels at a minimum in order to maintain
consistent weld quality. The lower jaws on your welder are made from a copper tungsten alloy, which provides conductivity at 48% of
pure copper, and has better wear characteristics than pure copper. If the jaws were made of steel they would wear better, but the
conductivity would only be about 18% of pure copper. The lower conductivity would produce a lower quality weld.
Other forms of resistance include:
•
Dirt or weld flash embedded in the surface of the jaws.
•
Worn or uneven jaw surface.
•
Dirt, oil, or shims between jaw and carriage surface.
•
Pitting of jaw surfaces.
•
Jaws that have been flipped over.
CAUTION: NEVER FLIP THE LOWER JAWS OVER
as this could cause serious damage to the carriages
and will void
your warranty.
RECONDITIONING WELDING JAWS
When your jaws become worn, pitted, or embedded with foreign material they may be reconditioned by surface grinding.
Surface grinding will remove the worn part of the jaws while maintaining flatness, parallelism and a smooth finish. Both lower
jaws must be ground together in order to maintain the same thickness and keep the welded blade properly aligned. A surface
profilometer finish of 32 or better is acceptable. New jaws are 1/2” thick and can have up to 1/8” of material removed. Typically it is
necessary to remove .005” - .010” of material to restore the finish on the welding side of the jaws. The bottom (beveled side) of the
jaws also need to be surface ground to clean in order to maintain parallelism and to remove warping.
The upper steel jaws also need to be reground periodically, though not as often due to the better wear qualities of steel. These
jaws must also be ground together for the same reasons as the lower jaws, but only need to be ground on the welding side.
PERIODIC MAINTENANCE
AT THE BEGINNING OF THE DAY & EVERY TIME THE BLADE SIZE IS CHANGED
•
Clean the entire weld area thoroughly with a rag and cleaning agent, such as welding anti-spatter spray.
•
Check the clamping pressure distribution and
adjust if necessary.
•
Apply welding anti-spatter spray liberally to the weld area between the carriages and wipe the jaw surfaces dry before
welding. Reapply anti-spatter as necessary throughout the day.
AFTER EVERY WELD
•
Blow off the jaws with compressed air to remove any loose weld flash and dirt before clamping a blade.
EVERY 10 WELDS
•
Wipe the jaw surfaces with a rag and clean the weld area to remove weld flash. Any weld flash adhering to the edges of the
jaws can be removed with a scraper or a flat blade screwdriver.
CAUTION
: Take care when scraping off weld flash not to nick, dent or scratch the surfaces of the lower jaws.
DAILY
•
Remove the clamp blocks and flash guard.
•
Clean the entire weld area thoroughly with a rag and cleaning agent, such as welding anti-spatter spray.
•
Clean and inspect all parts for wear and damage.
•
Clean and inspect the flash guard for any cracks or holes and replace if necessary.
•
Inspect lower jaws for uneven wear, pitting and cracking.
Summary of Contents for FW-200 HPA
Page 4: ...Section 1 INSTALLATION ...
Page 7: ...Section 2 OPERATING INSTRUCTIONS ...
Page 8: ...FW 200 HPA Rev 4 2 1 ...
Page 21: ...Section 3 MAINTENANCE ...