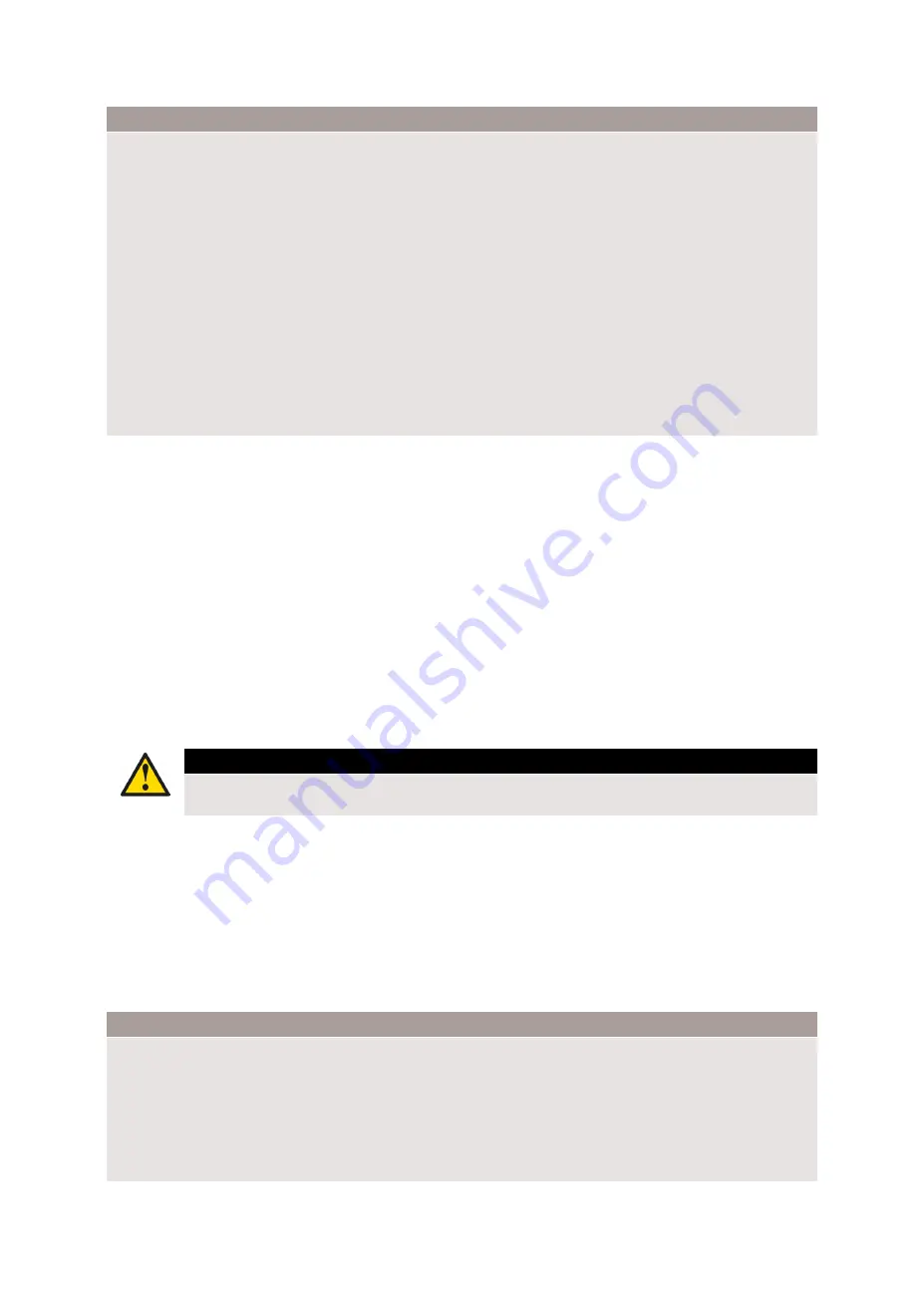
34
system
air
Commissioning
•
Before checking the correct fan installation and operation, switch off the repair switch of the fan section in which
you intend to intervene, or alternatively switch off the main switch on the air handling unit electric control cabinet,
and lock the switch in the off position, to break the current supply circuit to the drive electric motor.
•
Prior to starting the electric motor, remove any mechanical interlocks on vibration isolators.
• The fan must not be operated if the door of the fan unit is open.
•
By means of a pulse start, check the correct direction of the fan rotation. The rotor must rotate in the direction of
the arrow on its casing. In the event of an incorrect direction of rotation, switch two phases on the contactor. The
procedure for checking the direction of rotation must be carried out with the fan section door closed. Observe the
direction of rotation through the service door inspection window, with the lamp in the section on.
•
After the first start, measure the electric motor current. If the electric current is less than or equal to the nominal
current, you may proceed to set up the air volume flow rate.
•
The air volume flow rate is adjusted by changing the position (opening or closing) of the control dampers. Once
the air volume flow rate is set up, measure the electric motor current again. An electric current lower than or equal
to the nominal current indicates the correct operation of the fan section. If the motor current exceeds the nominal
value, shut down the electric motor and establish the cause of its incorrect operation.
Causes and corrections
The possible causes are the following: an incorrect motor connection, an incorrect supply voltage, an incorrect supply
frequency, incorrect electric leads, an incorrectly selected size of the electric motor, incorrect pressure drops, an excess
air volume flow rate.
In order to correct the air volume flow rate, reduce the electric motor revolutions by means changing the pulley on the
motor and/or the pulley on the fan. In order to correct the pressure levels, adjust the control dampers.
After remedying all the causes of incorrect operation, measure the electric motor current again. An electric current lower
than or equal to the nominal current indicates the correct operation of the fan section.
For rooms with an excess supply air, any failure of the intake air fan must result in the automatic shutdown of the
discharge air fan, too, in order to prevent any reversal of the air flow from the room to the neighbouring rooms. If excess
discharge air is required, the interlock logic of the preceding sentence is reversed.
In the case of the use of air recirculation in hygienic-type air handling units, check whether there are any hygienic-
toxicological concerns associated with the contamination of the supply air by harmful gases, i.e. whether the use of air
recirculation is allowable at all.
Caution
During operation, all the covers and service doors of the section must be kept closed at all times. The fan
may not operate with the fan section door open.
Prior to any intervention in the fan section, switch off the repair switch on the fan section in which you intend to
intervene, and lock the switch in the off position, in order to break the current supply circuit to the drive electric motor.
Proper maintenance is also a prerequisite for safe unit operation. Regularly check the tightness of all the threaded joints,
electrical connection terminals, grounding and section casing sealing.
Overloads and excessive temperatures may damage the bearings and lead to excessive operating noise. Replace
damaged bearings.
With proper maintenance, approx. 20,000 hours of service life of the bearings can be achieved at a minimum; the
specific service life value is quoted by the fan manufacturer.
Check monthly
• The mounting of the rotor on the shaft,
• the tightness of all the threaded joints,
• the rotor run,
• the vibration isolators of the fan-electric motor assembly,
•
the flexible connections, and
•
the shaft bearings; if axial shifts of shafts in the bearings are detected, consult the fan manufacturer and remedy
the fault.