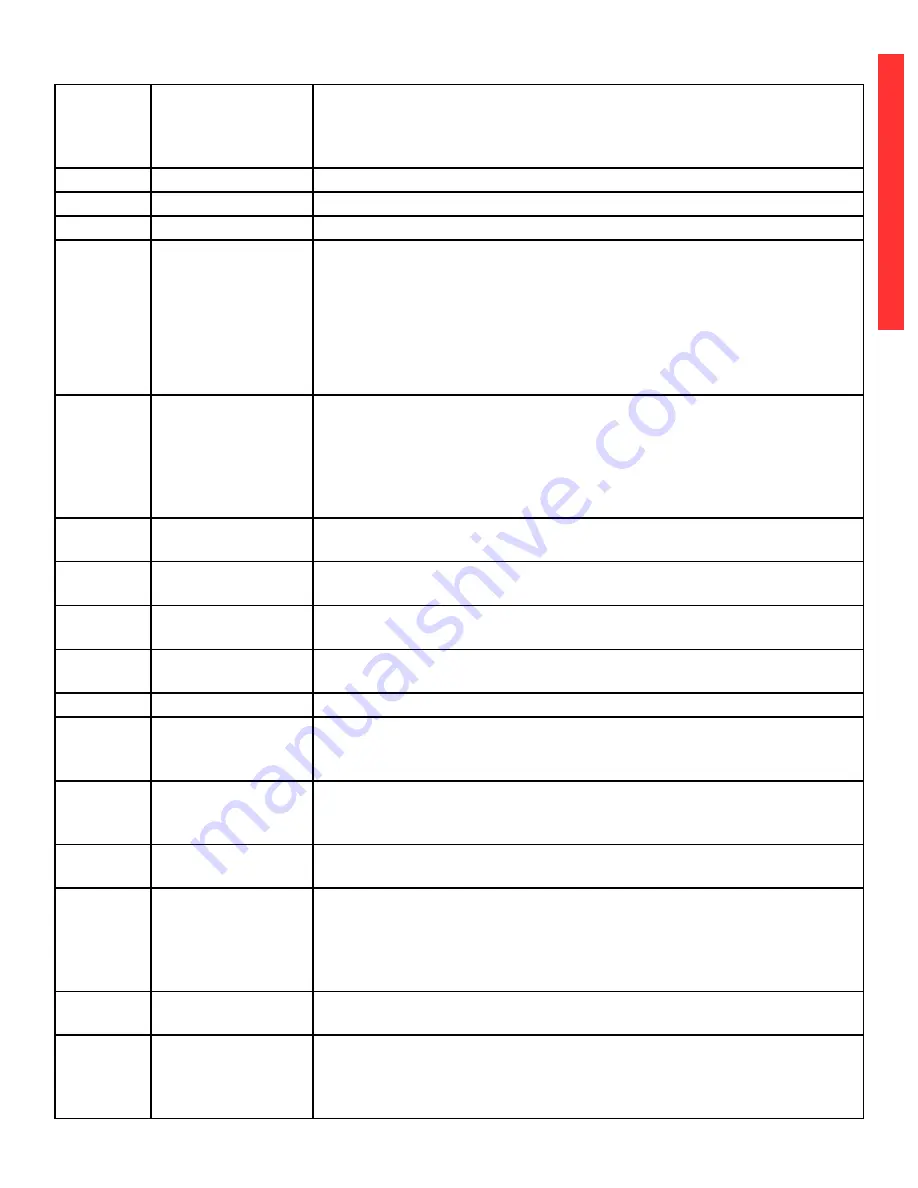
Technical Manual
31
Brew Temperature
Reads High
Display temperature will climb during brewing as high temp water from
the steam tank heat exchanger enters the brew tank. This is normal, and
the water dispensed will be at your set point, not the displayed tempera-
ture.
Make sure the set point has not been changed.
Check that the relay is functioning properly.
Check that the connection to the temperature probe is intact and secure.
Steam
Pressure
Steam Pressure is
set for 1.8 Bar or
Higher
● The machine can be set for steam pressure at over 2.0 Bar but there
can be side effects in the brewing process. A small amount of water is
preheated in the steam tank for brewing. If the temperature in the steam
tank is set very high then this could allow for the preheated brew water to
be too hot and cause some erratic brew temperature spikes. There are
ways to make this work if it is absolutely necessary to have a very hot
steam tank. Contact Synesso for more info.
Sudden loss of
Steam Pressure
● Too much hot water has been used for Tea, Americano, rinsing, or
warming cups while still steaming milk. Allow the machine to recover.
Check temperature setting on the steam tank to make sure they are high
enough for your application. Watch steam gauge, when pressure drops,
allow the heating elements to heat the cold water being introduced into
the steam tank
● Check to make sure all Set points, especially steam tank settings, are
accurate and functioning.
● Check that the element breaker on the electrical box is in the ON posi
-
tion
Steam Tank is not
filling
● Debris caught in the water control valve or worn out valve
● Water level probe (auto fill) needs to be de-scaled or cleaned. This
probe is located behind the left side panel
● Make sure level probe (auto fill) is working. See Test Level Probe
● Water is too hard. The water level (auto fill) probe requires a low level
mineral content in order to detect the water and relay the information to
the CPU. Do not use deionized water in the machine.
● On machines built prior to 01-01-2011, adjustment can be made to the
level probe sensitivity control on the power board in the electronics box.
See Probe Sensitivity Photo
Steam Valve Stem
Seals Leak
● Replace O-Rings. Purchase Rebuild Kit. See Steam Valve Rebuild
instructions for more info.
Auto Fill Valve
(Solenoid) is turning
OFF and On without
Filling the Steam
Tank
● Check that the water to the machine has not been cut off or restricted.
● Confirm that auto fill delay is set to at least 5 seconds. See
Programming Guide
● If the machine is installed on a boat or other mobile platform, increase
the autofill delay as the water may “slosh” inside the tank and confuse the
level probe.
TROUBLESHOOTING
Summary of Contents for Espresso Machine
Page 11: ...Technical Manual 11 ...
Page 13: ...Technical Manual 13 HYDRAULIC SYSTEM HYDRAULIC SCHEMATIC DUAL INLET ...
Page 14: ...Technical Manual 14 HYDRAULIC SYSTEM HYDRAULIC SCHEMATIC SINGLE INLET ...
Page 15: ...Technical Manual 15 HYDRAULIC SCHEMATIC HYDRA HYDRAULIC SYSTEM ...
Page 22: ...Technical Manual 22 ...
Page 24: ...Technical Manual 24 Electrical System Wiring schematic ELECTRONIC SYSTEM ...
Page 27: ...Technical Manual 27 ELECTRONIC SYSTEM ...