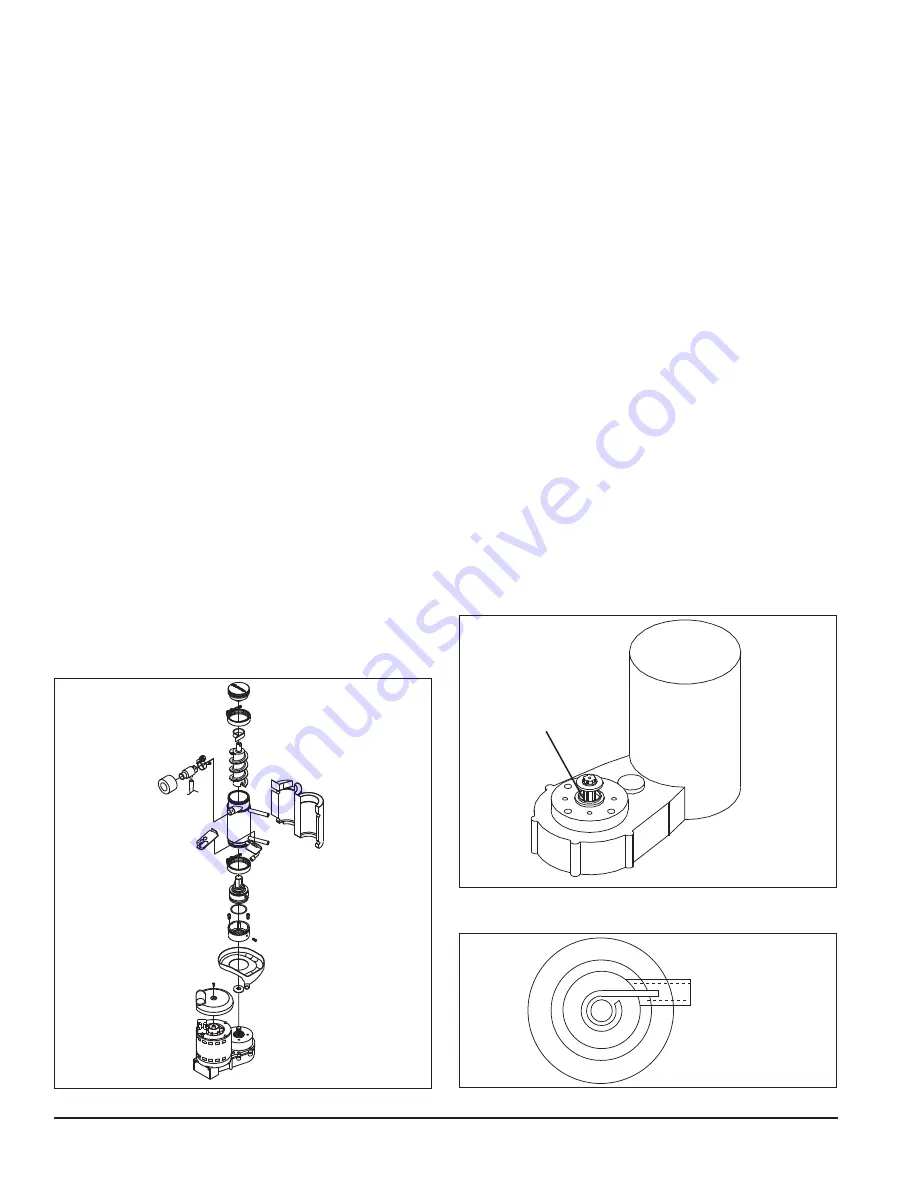
18
25CI400A/W • 25HI400A • 50CI400A/W • 50HI400A
Evaporator reassembly
1. Clean gearmotor boss, output shaft and shaft well.
2. Install drain pan and evaporator mounting base.
3. Fill gear motor shaft well with food grade grease
(Fig. 27.1).
4. Install condensate shield and seat against gear
motor boss.
5. Install bearing O ring in groove in evaporator
mounting base.
6. Lower bottom bearing assembly into evaporator
mounting base.
7. While maintaining a slight downward pressure on
bottom bearing assembly, tighten hex head bolt with
a 5/16" wrench.
8. Position evaporator over lower bearing assembly
and align grooves with pins in bearing assembly.
9. Install vee band clamp and nut to 70 in/lb.
10. Place auger in center of evaporator and rotate to
mate with drive pin.
11. Install ice compression loop, orienting loop as
shown in Fig. 28.
12. Install upper bearing and seal assembly, rotating
bearing to slip pin into auger slot.
13. Install upper vee band clamp and nut to 70 in/lb.
14. If evaporator was replaced, reinstall compression
nozzle on new evaporator.
Fig. 27
27.1
Fig. 28
Evaporator disassembly
Note:
The upper bearing, lower bearing and auger
assemblies must be replaced as assemblies. The bottom
and top bearing assemblies cannot be fi eld assembled to
factory specifi cations (Fig. 26)..
1. Disconnect power to icemaker.
2. Shut off water to icemaker.
3. Drain evaporator and fl oat tank.
4. Disconnect plastic tubing from evaporator water
inlet.
5. Disconnect compression nozzle tubing and reservoir
overfl ow tubing from secured clip.
6. Remove nut and upper vee band coupling from top
of evaporator
7. Lift top bearing assembly straight up with a slight
rotating motion and remove.
8. Remove ice compression loop located at top
of auger.
9. Lift auger straight up and out of evaporator.
10. Remove nut and lower vee band coupling from
bottom of evaporator.
11. Lift evaporator to clear bottom bearing assembly.
12. Loosen hex head bolt in side of mounting base with
5/16" wrench and lift lower bearing assembly.
13. Remove condensate shield.
14. Remove four Allen head machine screws holding
mounting base to gearbox.
15. If replacing evaporator, remove compression nozzle
from evaporator port.
Fig. 26