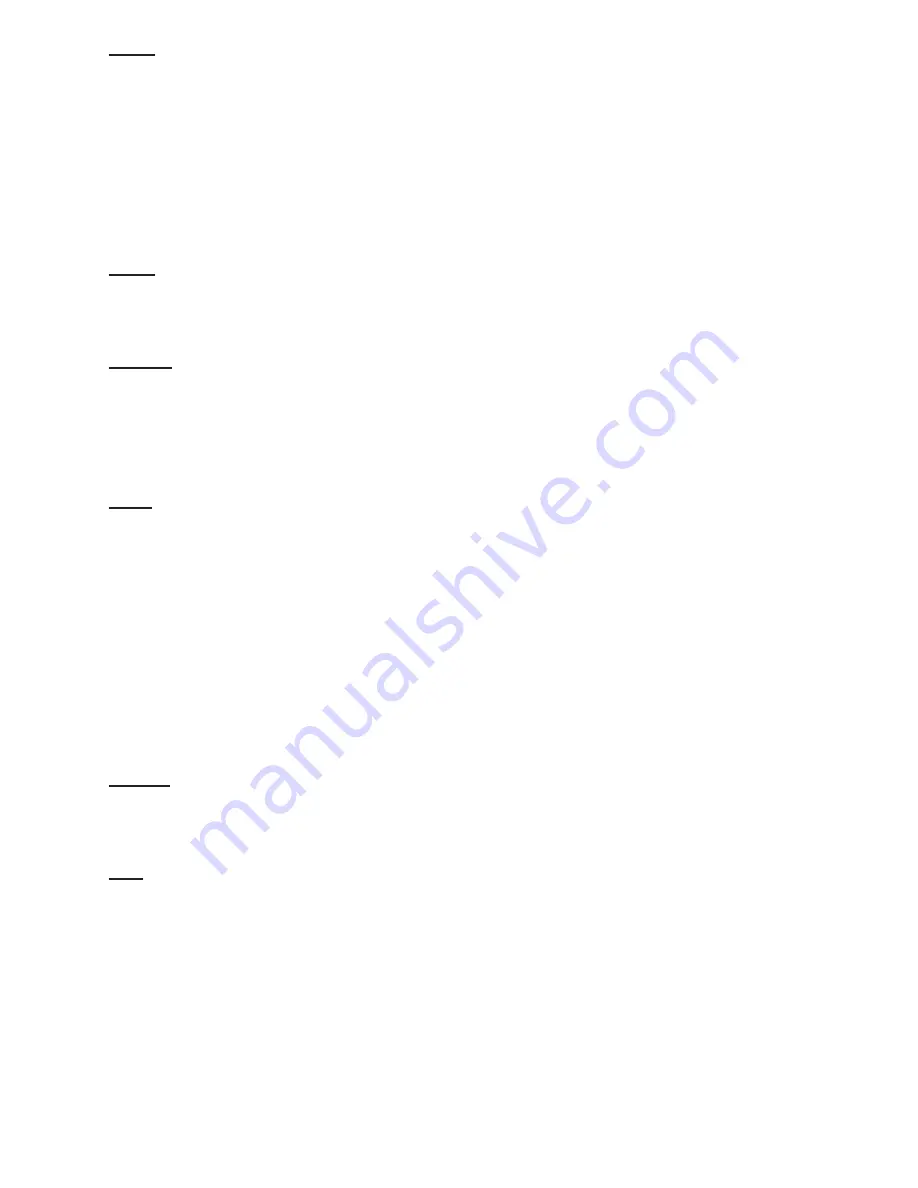
RD3-
“RD3” is the restart delay after an undercurrent. It is also known as a dry
well recovery timer and is usually used in submersible pumping
applications. The setting of “RD3” depends on the recovery time of the
water well and varies widely from application to application.
Note: In linear trip mode (TC = J00), the RD3 time is appoximately 50% of
the normal RD3 time. Example: If RD3 is set to 30 minutes, the
TC = J00, then the actual RD3 time in the linear trip mode will be 15
minutes.
#RU-
“#RU” is the number of successive restart attempts allowed after an under
current fault before the overload relay requires manual reset. A setting of
“0” is manual reset and a setting of “A” is continuously automatic reset.
ADDR-
“ADDR” is the address setting for RS-485 communications. Available
settings are from A01 - A99. This setting is programmed on the right half
of the PROGRAM/DISPLAY adjustment (see programming instruction
note for explanation of dual function settings). You may ignore this
setting if RS-485 communications are not used.
#RF-
“#RF” is the number of successive restart attempts allowed after a current
unbalance, single phasing or overload fault. The following settings are
available: “0”, “1”, “oc1”, “2”, “oc2”, “3”, “oc3”, “4”, “oc4”, “A”, and “ocA”.
A setting which includes “oc” will allow the overload relay to automatically
reset after an overload fault (eg., a setting of “oc2” will allow the overload
relay to reset 2 times after an overload condition, current unbalance, or
single phasing before locking out if an overload condition, current
unbalance, or single phasing is detected within one minute after
restarting). A setting which does not include “oc” requires a manual reset
for all overload faults. A setting of “0” is manual reset and a setting of “A”
is continuously automatic restart.
UCTD-
“UCTD” is the undercurrent trip delay timer. This setting represents the
maximum time that the unit will tolerate an under current condition.
Typically, UCTD is set to 2 - 4 seconds.
GF-
“GF” is the ground fault protection amperage threshold. This setting
detects a leakage current to ground and signals an insulation breakdown
in the system. The “GF” setting should be some where between 10% and
20% of the full load motor current. Short circuit protection is provided by
separate branch protective devices such as circuit breakers or fuses.
Ground fault protection is a Class II ground fault protector and should not
be used for personnel safety, but can be used to indicate motor
degradation for maintenance purposes.
07/25/03
-8-