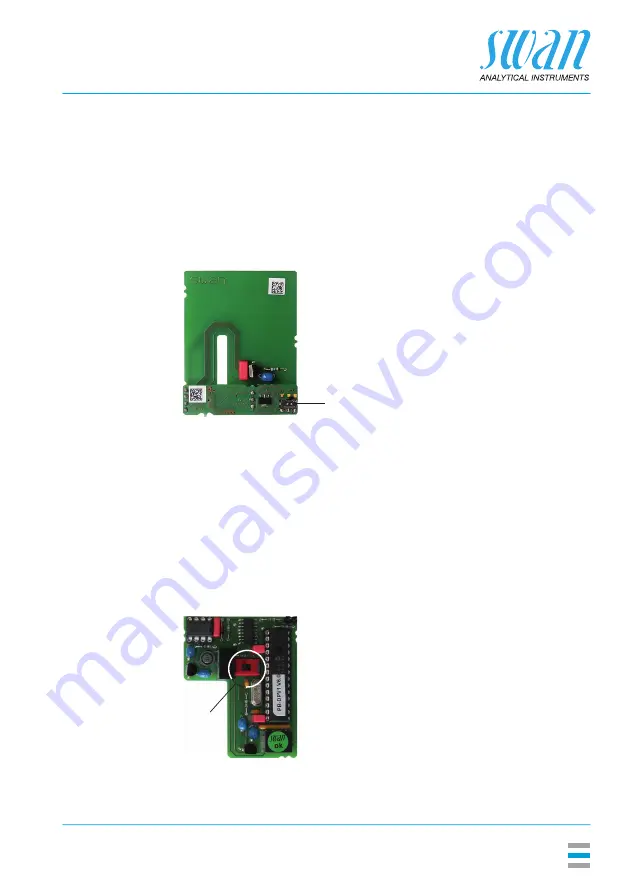
A-96.250.211 / 171121
AMI Sodium P
Installation
47
3.11.1 Signal Output 3
Terminals 38 (+) and 37 (-).
Requires the additional board for the third signal output 0/4–20 mA.
The third signal output can be operated as a current source or as a
current sink (switchable via switch [A]). For detailed information see
the corresponding installation instruction.
Note:
Max. burden 510 Ω.
Third signal output 0/4 - 20 mA PCB
3.11.2 Profibus, Modbus Interface
Terminal 37 PB, Terminal 38 PA
To connect several instruments by means of a network or to config
-
ure a PROFIBUS DP connection, consult the PROFIBUS manual.
Use appropriate network cable.
Note:
The switch must be ON, if only one instrument is installed,
or on the last instrument in the bus.
Profibus, Modbus Interface PCB (RS 485)
A
Operating mode selector switch
A
A
On - OFF switch
ON
OFF
A