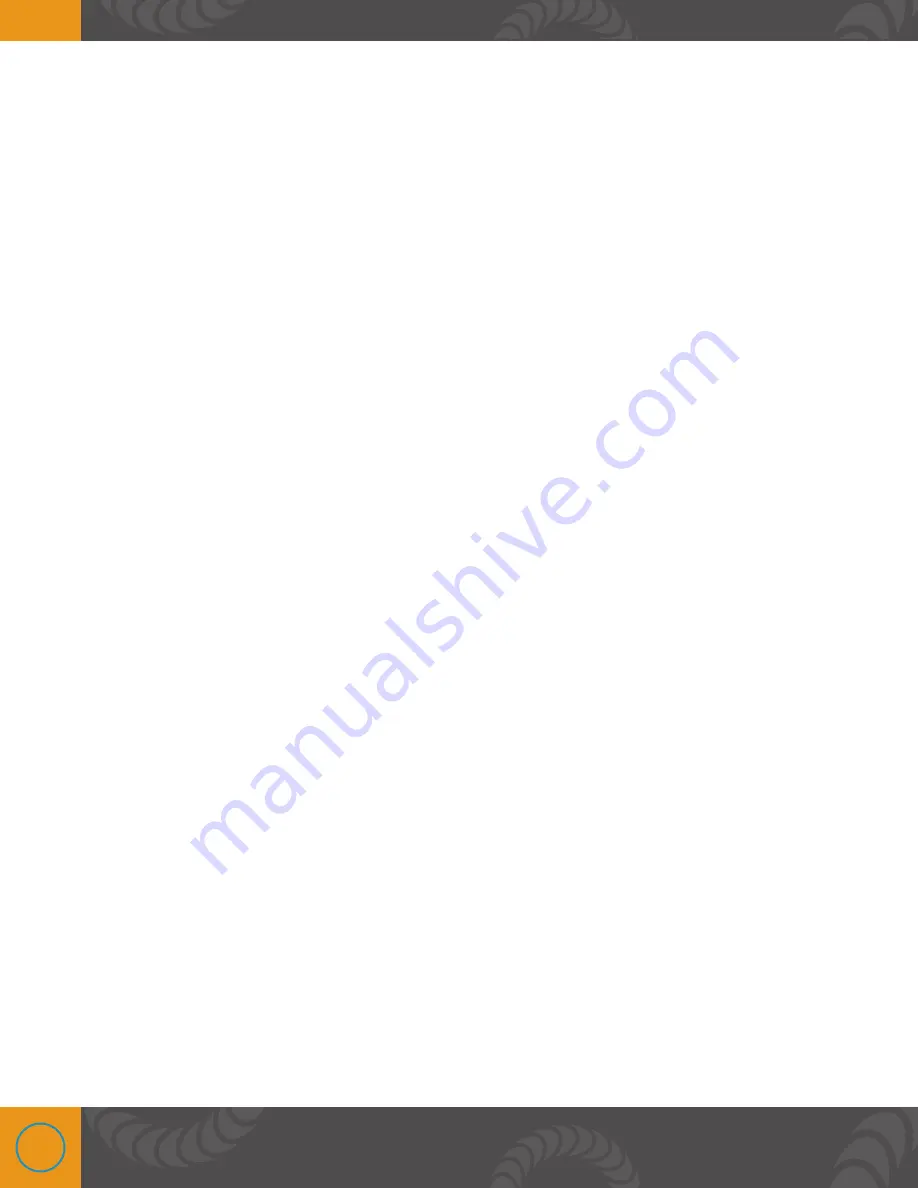
6
Fuse
20A fuse included.
Replacement fuse: Schurter Inc. Manufacturer #0034.3130.
Fans
Airflow will come out of the unit from these locations and could be warm. The fans will not normally
be spinning, but will turn on if the unit is hot. They may turn on even if welder is not being used, but
is turned on. *Do not block fans.
USB Port
USB flash drive can be inserted for updating the unit software *Use a 4GB stick of memory or less.
*See Linear DC product page at www.sunstonewelders.com for update or contact a Sunstone
representative.
Connecting Welding Attachments
CONNECT WELDING ATTACHMENTS
Sunstone Weld Head - automatic weld triggering
1. Connect weld head cables to negative and positive terminals on the back of the Linear DC.
2. Connect weld head actuation cable to “Weld Head Actuation” DIN connection port on the
back of the welder.
3. See weld head manual for instructions on weld head foot pedal setup. *Weld head foot
pedal will control weld head up and down movement and weld triggering.
Sunstone Weld Head - dual foot pedal triggering
1. Connect weld head cables to negative and positive terminals on the back of the Linear DC.
2. Connect included Linear DC foot pedal into “Weld Discharge Trigger” DIN connection port
on the back of the welder. *With this option users will not connect the weld head actuation
cable to any of the DIN ports.
3. See weld head manual for instructions on weld head foot pedal setup. *Weld head foot
pedal will control weld head up and down movement and Linear DC foot pedal will control
weld triggering.
Summary of Contents for Linear DC
Page 1: ...Sunstone Welders Linear DC User Manual...
Page 27: ...27 COMPARATOR WELD HEAD...
Page 41: ...41...