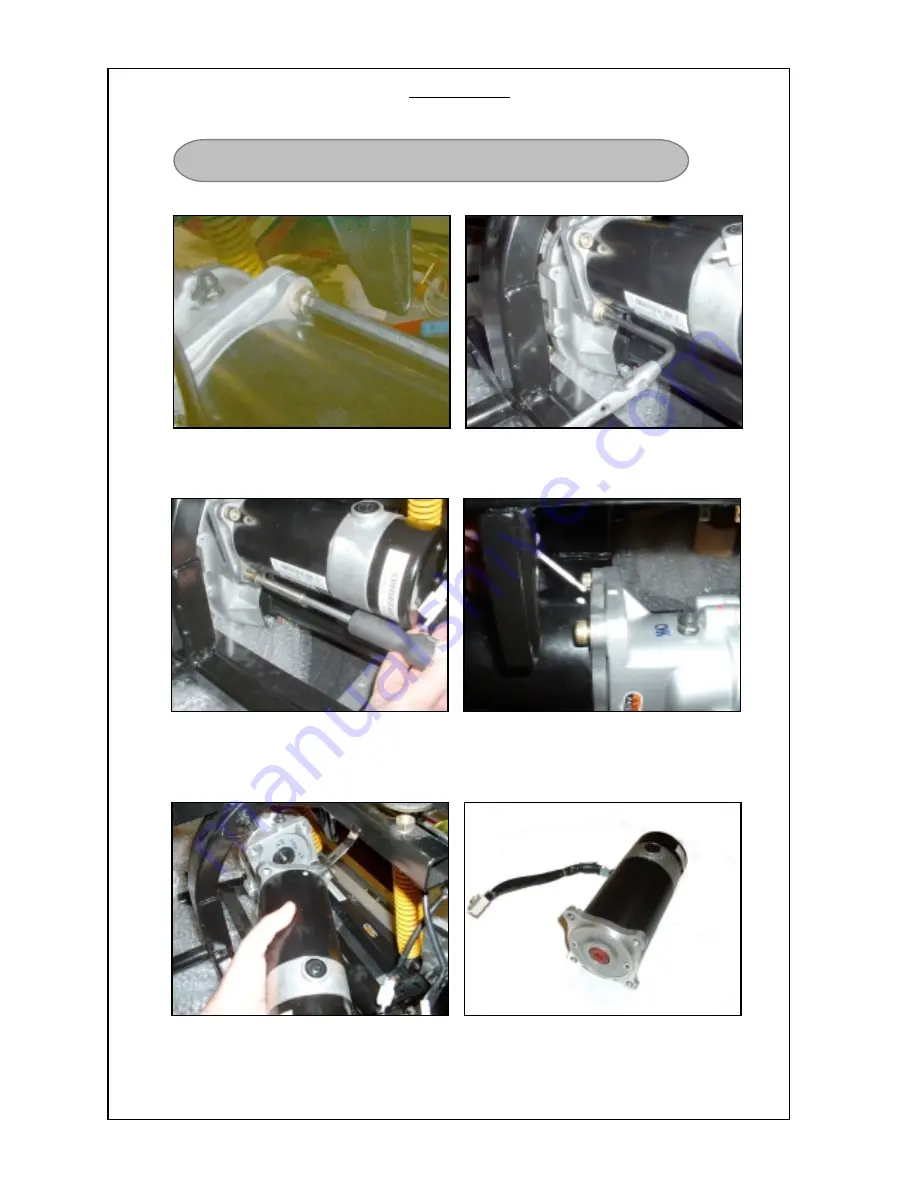
EMERALD
MOTOR/ELECTRONIC BRAKE ASSY.
1. A 6.00mm hex wrench is the basic
tool required for undoing the four
Motor Studs.
2. Some of the studs may require
extra force. That may require a
cranked hex key or tool.
3. Limited room may also require the
use of a hex key driver tool. If the
Drive Train has to be removed, do
that first and then take the Motor off.
4. It is a good idea to mark the top of
the Motor and Transaxle for refitting
purposes.
5. Carefully withdraw the Motor from
the Transaxle.
6. The Motor/Electronic Brake Assy.
27
Summary of Contents for EMERALD
Page 1: ...Workshop Manual EMERALD 4 WHEEL EN G LISH Scooters ...
Page 2: ......
Page 51: ...EMERALD ASSEMBLY REFERENCE PHOTO s MAIN FRAME ASSEMBLY 48 ...
Page 52: ...EMERALD ASSEMBLY REFERENCE PHOTO s MAIN BODY ASSEMBLY 49 ...
Page 53: ...EMERALD ASSEMBLY REFERENCE PHOTO s TILLER ASSEMBLY 50 ...
Page 54: ...EMERALD ASSEMBLY REFERENCE PHOTO s REAR DRIVE ASSEMBLY 51 ...
Page 55: ...Please use this Wokshop Manual in conjunction with the Emmerald Owners Manual Parts Manual ...