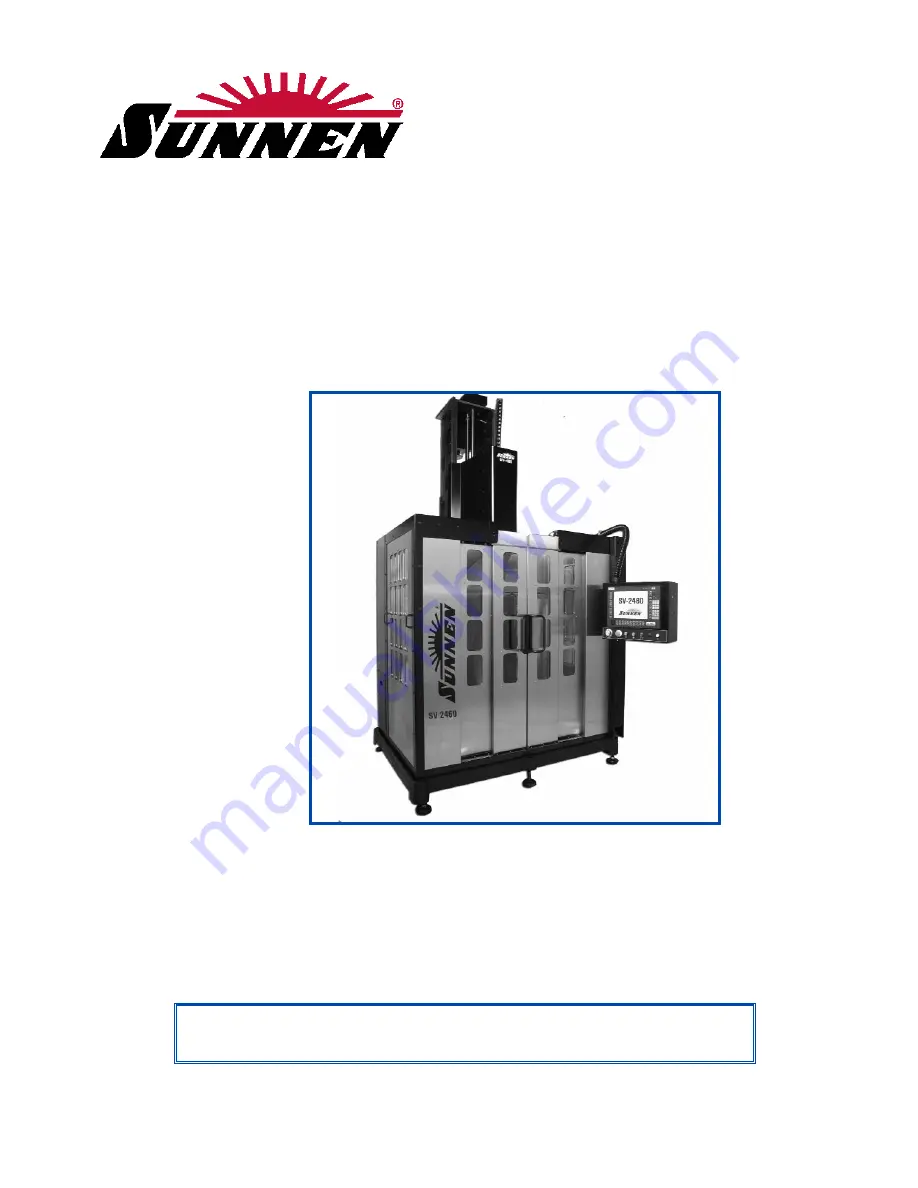
SUNNEN
®
PRODUCTS COMPANY • 7910 MANCHESTER ROAD • ST. LOUIS, MO 63143, U.S.A. • PHONE: 314-781-2100
READ THE FOLLOWING INSTRUCTIONS THOROUGHLY AND CAREFULLY BEFORE UNPACKING,
INSPECTING, OR INSTALLING THE SUNNEN
®
SV-2460 VERTICAL HONING MACHINE.
I-SV-461
Installation, Setup
and Operation
INSTRUCTIONS
for
SUNNEN
®
VERTICAL HONING MACHINE
Models:
SV-2460
“SUNNEN
®
AND THE SUNNEN LOGO ARE REGISTERED TRADEMARKS OF SUNNEN PRODUCTS COMPANY.”
O R I G I N A L I N S T R U C T I O N S
Summary of Contents for SV-2460
Page 14: ...8 NOTES...
Page 22: ...16 NOTES...
Page 26: ...20 NOTES...
Page 32: ...26 NOTES...
Page 36: ...30 NOTES...
Page 38: ...32 NOTES...
Page 40: ...34 NOTES...
Page 41: ...1 OF 2 C DECLARATION OF CONFORMITY 35 SAMPLE CE DOCUMENT...
Page 42: ...2 OF 2 C DECLARATION OF CONFORMITY 36 SAMPLE CE DOCUMENT...