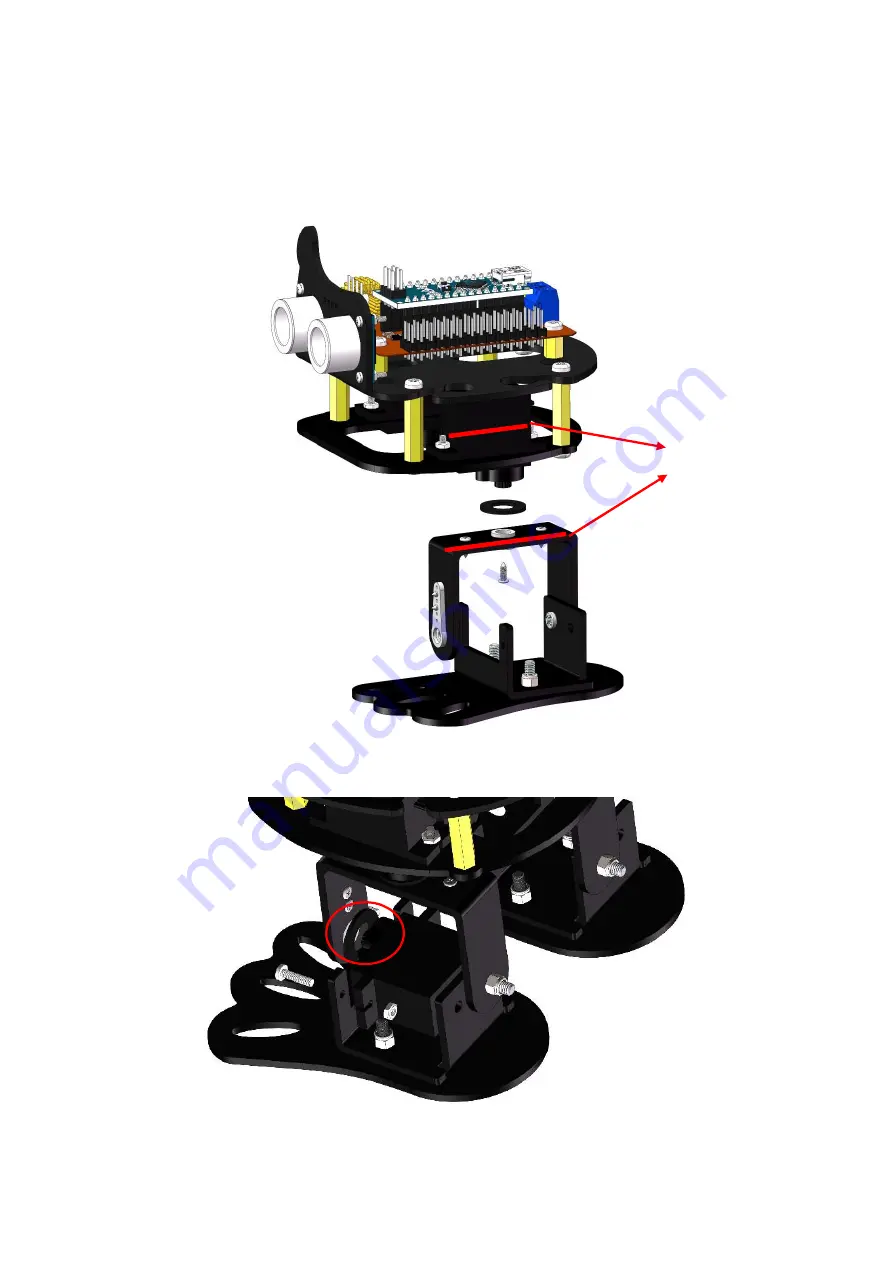
21
v. Foot Assembly
Assemble the No.4 board on the left leg and the No.3 board on the cover together with the
upper-left servo through the servo's matching screws (the smallest screws in the packaged
with servo). Try to keep the edges of the 4th board and the servo parallel to each other.
They need to be reinstalled if not parallel to each other.
Parallel
Put a servo shaft on No.3 board, and then secure the lower-left servo (pin 12) to the No.5
board with M2*8 screws and M2 nuts.
Note that the servo shaft should be close to the inside
of No. 7 board
.