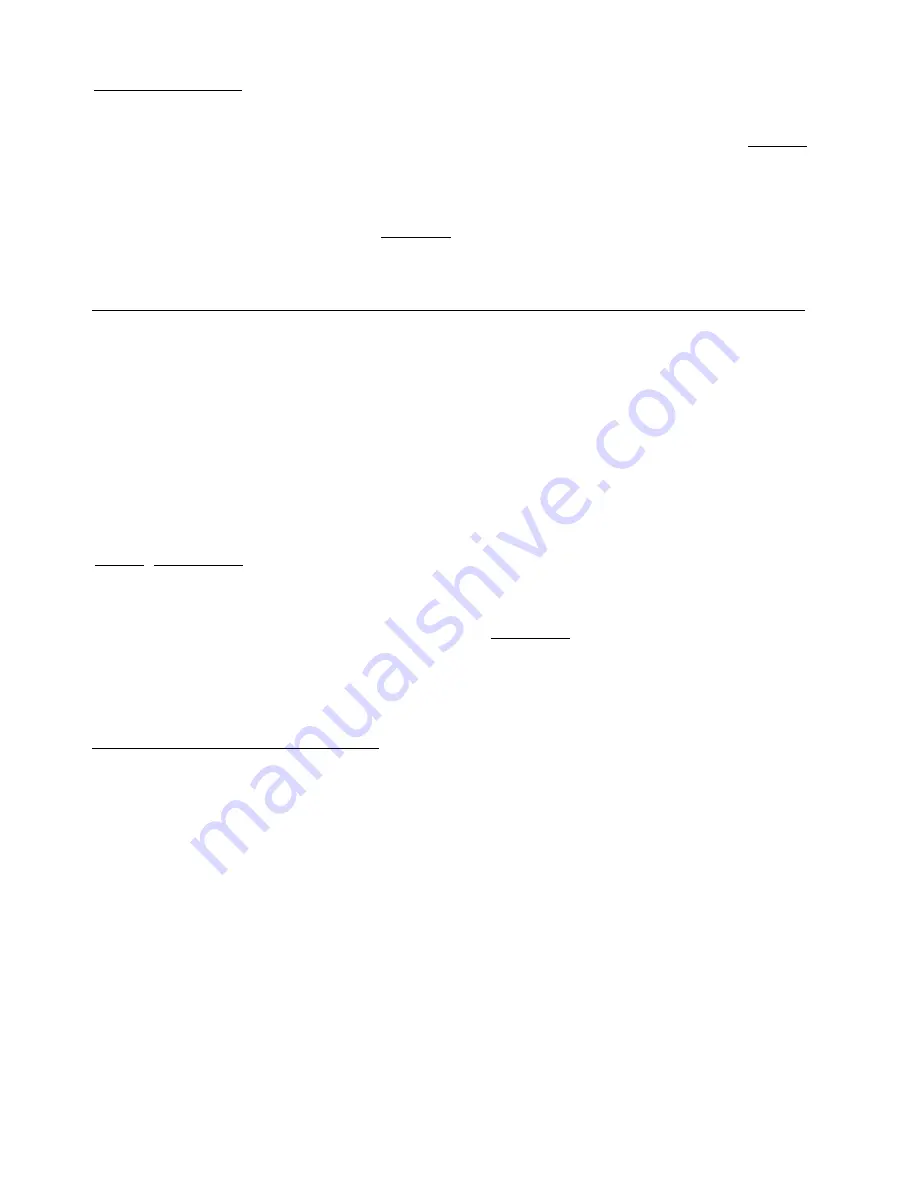
3. Frozen
Bearings
To check the bearings to find if any have seized because of lack of oil or
other causes, grasp the lower part of the whippers (21), and turn inward. If
the bearings for whipper spindle sleeves (13 and 20), motor bearings (45), or
governor slide bearing (113) have seized it will be impossible to turn the
whippers. To locate seized bearing and repair see sections 4, 5, 5-A, 5-B, 6,
7 and 9. If all bearings are free the whippers will turn freely. The whippers
should not turn at all in an outward direction; if they do, that indicates a
worm gear (9) is stripped and the gear should be taken out and replaced as in
sections 4 and 16.
4. Removal of Whipper Spindle Sleeve and Oil Retainer Assemblies (13 and 20)
To remove whipper spindle sleeves unscrew the two gear case cover screws (8)
and take off gear case cover (7). Put both whippers (21) in place and rotate
inward until worm gear set screws (10) can be seen, then loosen set screws
with “T” handled worm gear set screw wrench. Next, grasp the sleeves and pull
them down and out of the gear case (5). If juicer sleeve (20) is frozen in the
bearing it may be necessary to drive it out, using a brass rod which will pass
thru the bearing and which can be driven downward from the hole in top of gear
case. Another helpful method of removing frozen spindle sleeves is to turn the
motor up-side-down and squirt kerosene from a can between the outside of the
sleeve, and the bearing part of the gear case; then remove switch cover
assembly (71) as in section 5. Grasp the governor disc (100) in one hand and
insert a whipper in the frozen spindle sleeve and try to turn both in the same
motor direction with a back—and—forth movement. The frozen spindle should
gradually loosen until it can be rotated and set screw (10) is brought to the
front of the gear case. If whipper spindle sleeves are frozen it is necessary
to replace the sleeves only, see sections 16 and 17. But if the whipper
spindle sleeves come out easily and the armature cannot be turned by grasping
the worm shaft, the motor bearings (45) are probably seized or are badly
gummed up. To continue it will be necessary to disassemble motor as in
following sections.
5. How to Remove Governor (100) and
Switch Mounting Bracket (105).
Remove screw 90 and 65 and gently tap switch cover 71 until the lacquer is
broken and cover can be pulled straight back and off. A final test for frozen
or gummy motor bearings (45) may be made at this point by grasping the
governor disc (100) and turning it, which normally should turn freely (with
the armature shaft) if bearings are in good order. If governor and armature do
turn, it is probable that the governor slide bearing in the switch cover is
frozen or gummy and should be examined, washed out with kerosene and re-oiled,
or replaced with a new governor slide, bearing and lever assembly (113).
5-A. To continue the removal of governor (100) insert the Allen Head governor
wrench into governor set screw (101) and loosen set screw, two or three turns,
to the left. Governor may then be pulled off the armature shaft.