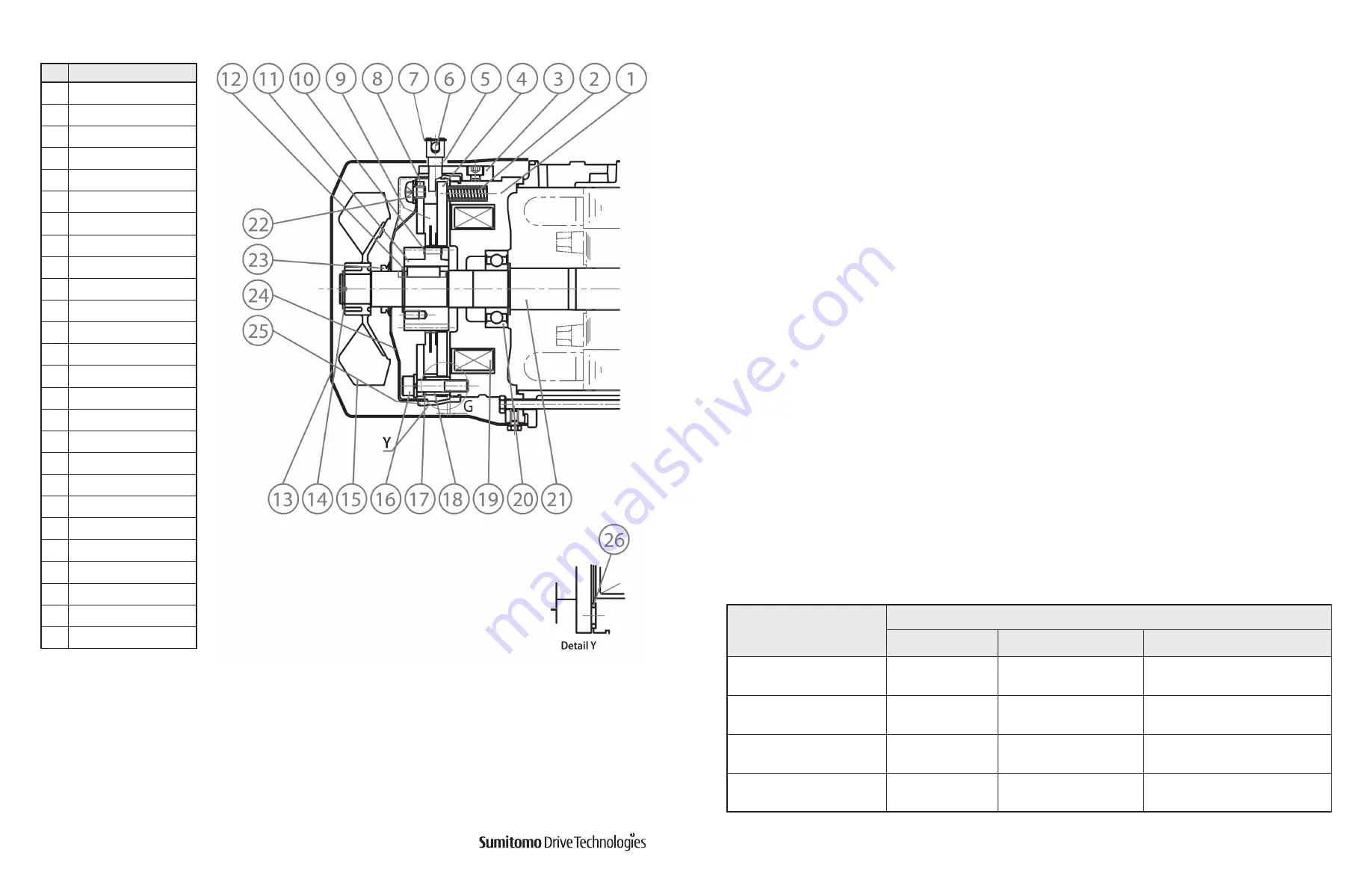
24
Hyponic®
Operating and Maintenance Manual
Hyponic® Operating and Maintenance Manual
25
www.SumitomoDrive.com
No.
Part Name
1
Stationary Core*
2
Pressure Spring*
3
Brake Release Support
4
Armature*
5
Shifting Pin
6
Brake Release Lever
7
Retaining Clip
8
Brake Shoe*
9
Brake Lining*
10
Leaf Spring*
11
Hub*
12
C-type Retaining Ring
13
Cover
14
Retaining Ring
15
Fan
16
Restraining Bolt*
17
Gap Adjusting Shims*
18
Spacer*
19
Solenoid Coil*
20
Fan Side Bearing
21
Motor Shaft
22
Attachment Screw
23
V-Ring
24
Waterproof Cover
25
Waterproof Seal
26
Shock Absorber*
Fig. 16 FB-1D, FB-2D, FB-1E, FB-1HE, FB-2E, and FB-3E Models (E-Series Shown)
*
These parts are included in a complete brake kit.
b) Operating Principles
The brake is a (fail safe type) spring actuated type brake, which will release the brake mechanism when the solenoid
coil is energized and engages when the coil is de-energized.
When power is applied to the unit, the solenoid coil and electric motor will become energized, and the energized
coil attracts the armature plate (4) against the tension of the pressure spring (2). As a result, the brake lining (9)
disengages, and the motor starts to run.
When the power is disconnected, the solenoid coil and the electric motor are not energized. This causes the pressure
spring (2) to actuate the armature plate (4) which in turn presses the brake lining (9) against the brake shoe (8) and
brings the motor to a quick stop.
a) At regular intervals, check that:
•
the unit is operating normally.
•
the brake lining is not excessively worn (or gap G is normal).
•
all the mounting screws are securely tightened.
b) Manual brake release procedure
FB-1D, FB-2D, FB-1E, FB-1HE, FB-2E and FB-3E brakemotors are equipped with a one touch release mechanism. To
manually release the brake with power to the unit turned off, pull the brake release lever up and out from its holder
and push it forward towards the reducer. Releasing the lever will re-engage the brake.
3. Inspection
The brake lining will wear after the unit has been used for a long period of time. Regularly check that gap G from
time to time
(Figure 16)
is at an acceptable value. If gap G become too large, the solenoid coil may fail to pull in
the armature plate and hence cannot release the brake, resulting in the unit remaining in a continuously braked
condition. Follow these steps to inspect the brake gap:
a)
Remove shifting pin (5) and brake release lever (6).
b)
Remove cover (13).
c)
Remove fan (15) by removing retaining ring (14).
d)
Remove waterproof seal (25).
e)
Insert a gap gage into the space between the stationary core (1) and armature plate (4). Measure the gap size at
three appropriate circumferential points.
f)
Check for brake performance by turning system power on and off a few times.
g)
The gap needs to be adjusted if the values are close to the allowable limit listed in
Table 13
.
4. Gap Inspection
Table 13. Brake Gap Size
Brake Type
Gap value G, in. (
mm
)
Spec. value
Allowable limit
Gap Adjustment Shim Thickness
FB-1D, FB-2D
0.012 - 0.016
(0.3 - 0.4)
0.024
(0.6)
0.008 - 0.01
(0.2 - 0.25)
FB-1E
0.01 - 0.014
(0.25 - 0.35)
0.024
(0.6)
0.008 - 0.01
(0.2 - 0.25)
FB-1HE, FB-2E
0.01 - 0.014
(0.25 - 0.35)
0.029
(0.75)
0.014 - 0.018
(0.35 - 0.45)
FB-3E
0.01 - 0.014
(0.25 - 0.35)
0.033
(0.85)
0.018 - 0.022
(0.45 - 0.55)