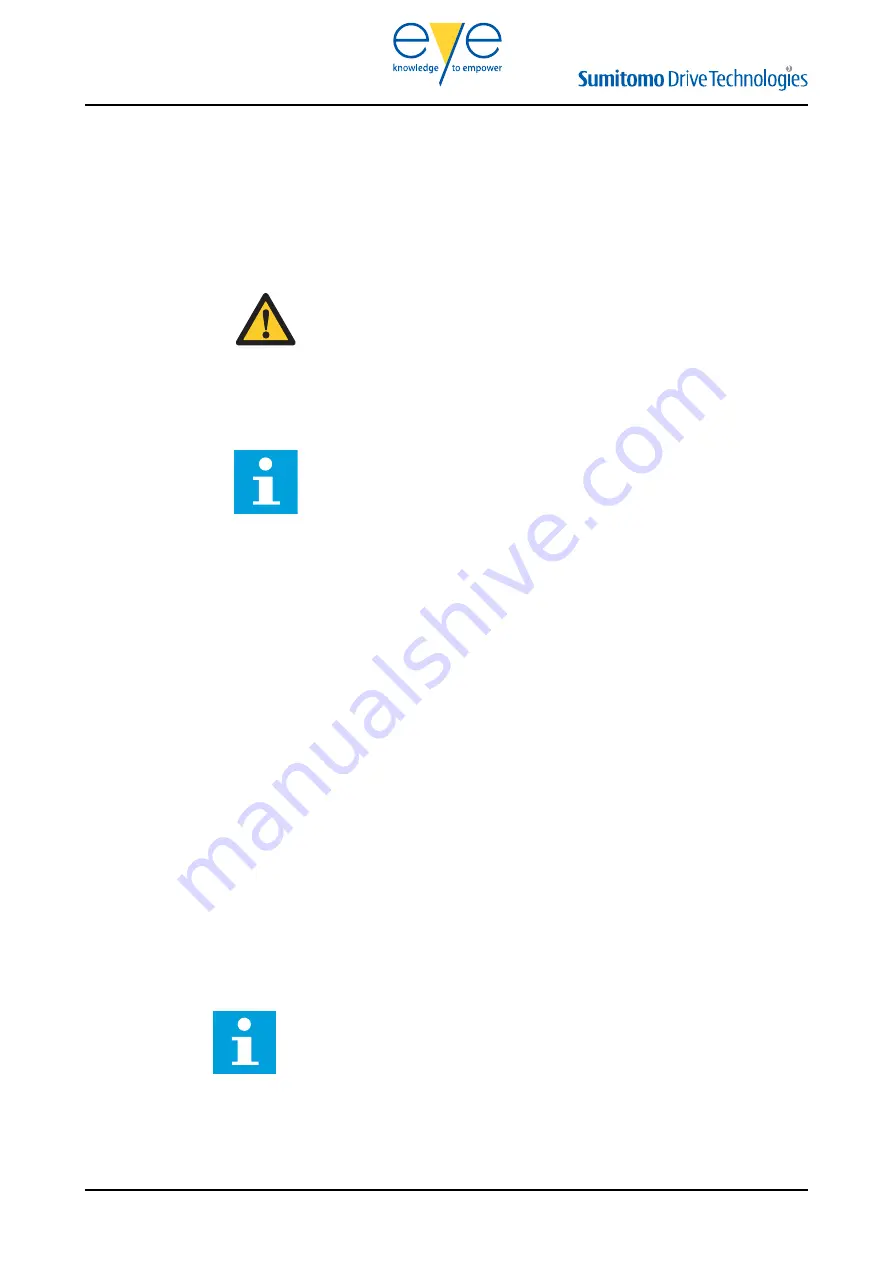
Installation
Installation - general instructions
• Put the device as close as possible to the gear unit or the hydraulic system.
Caution: Do not put the device above the oil level of the gear unit of the
hydraulic system. This can cause under-pressure at the suction side of the
pump.
• The device must be stable and easy to access.
• Use high-quality hoses that meet these requirements:
• The hoses must be a short as possible.
• The hoses must have the correct internal diameter.
Note: S.D.T. supplies hoses with the device that obey the requirements of
the gear unit or hydraulic system that you use. If you must use hoses with
different specifications, speak to S.D.T.
• Make sure that no oil can come out of the gear unit or the hydraulic system when you
connect the device:
• If the gear unit or hydraulic system has a drain valve, close the drain valve.
• If the gear unit or hydraulic system does not have a drain valve, drain the oil from
the gear unit or the hydraulic system. Do not discard the oil.
• Replace all the magnetic plugs on the gear unit or the hydraulic system with non-
magnetic plugs.
• Only install the LM2 Gears CMS unit when the device is in its final operation position.
Remove the packaging material
Procedure
1. Do a check for damage to the package.
2. If you see damage, speak to S.D.T. immediately.
3. Remove the packaging material.
4. Do a check for damage to the device.
5. If you see damage, speak to S.D.T. immediately.
6. Do a check if the device agrees with the shipping papers.
7. If the device does not agree with your order, speak to S.D.T. immediately.
Connect the device
Note: Before you connect the device, refer to the general instructions in
section
Installation - general instructions
on page 18.
6
6.1
6.2
6.3
Installation
18
UM_VP2500L_002_EN