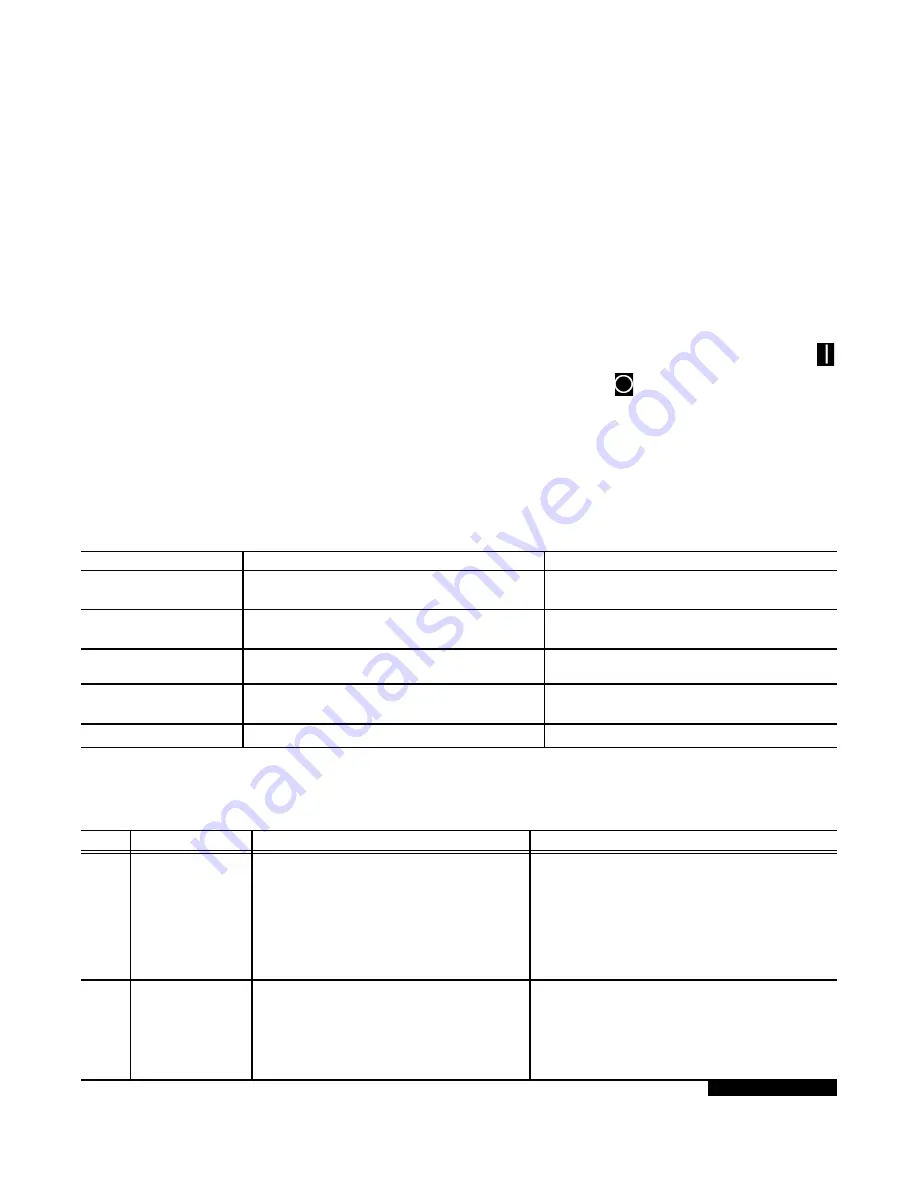
26
Section 6
VARIABLE SPEED DRIVE
Motor FLA -
The motor's rated full load amps at
nominal HP
(I)
Motor SF -
The motor's nameplate service factor
Motor V -
The motor's rated voltage
(I)
Motor Hz -
the motor's nameplate frequency
Motor RPM -
the motor's nameplate full-load speed
(I)
Some package designs employ motors connect-
ed for voltages lower (and FLA higher) than the
nominal voltage of the package, for improved per-
formance.
6.5 STARTUP OF NEW COMPRESSOR PACKAGE
1. Read and follow all safety warnings and cautions
in this manual.
2. At installation ensure:
• That the incoming power and ground wires
are properly connected to terminal blocks in
the electrical control box.
• Visually check all power and controls con-
nections to the drive to ensure that no dam-
age has occurred.
3. Check that moisture has not condensed inside
the variable speed drive.
4. Connect to the utility and switch the power on.
The Supervisor will establish communications
and report errors if correct conditions are not
found. If replacing a drive, communication faults
will be indicated for either improper communica-
tion wiring or improper application or communi-
cation software in the drive.
5. To check rotation, quickly press first the Start
then the Stop
key on the Supervisor. Com-
pressor rotation is factory set. If the fan rotates
incorrectly, disconnect power and simply inter-
change two of the fan motor leads at the fan
starter.
6.6 FAULT AND WARNING CODES
The Supervisor constantly monitors drive performance through the serial channel. The following messages
are specifically displayed by the Supervisor in the event of problems.
FAULT
VSD Param Lim Fault
VSD Com Error
VSD Emergency Stop
(VSD Code 51)
VSD Com Fault
(VSD code 53)
Drive Fault xx
POSSIBLE CAUSE
Incorrect model, HP or Voltage selected in
Factory & VSD Setup
Communications lost with the VSD
Emergency Stop is pressed
Break in Estop wiring
Communications problems detected reported
by the VSD
Problem reported by the VSD
SOLUTION
Make proper selections.
Check connections to the VSD. Check VSD
control power and check for board faults.
Clear the package emergency stop.
Check Estop wiring to the drive input.
Check connections to the VSD. Check VSD
control power and check for board faults.
Refer to fault codes in table below.
Drive fault codes are used for least-likely faults. The Supervisor will display these as "Drive Fault" with a code
number. If a keypad service tool is plugged into the drive, it will display the fault code and the fault name
shown in the first two columns.
1
2
Overcurrent
Overvoltage
The variable speed drive has detected a
high current (>4xIn) in its output due to:
• sudden heavy load increase
• short in the motor
• short in the cables to the motor
• unsuitable motor
The DC-link voltage has exceeded its high
limit due to:
• too short a deceleration time
• high voltage levels or surges in the utility
supply
Check loading.
Check motor.
Check cables.
Make the deceleration time longer.
Use a chopper and brake resistor.
Correct utility supply voltage (level is too high).
Add input impedance to limit surges.
CODE FAULT
POSSIBLE CAUSE
SOLUTION
Continued...
Summary of Contents for SUPERVISOR CONTROLLER Series
Page 6: ...Section 1 SAFETY 2 Figure 1 1A Decals...
Page 8: ...4 Section 2 SUPERVISOR DESCRIPTION Figure 2 1 Supervisor Control Panel...
Page 16: ...12 NOTES...
Page 24: ...20 NOTES...
Page 26: ...22 Section 5 WIRING SCHEMATIC DIAGRAMS 5 2 WIRING DIAGRAM SUPERVISOR CONTROL 02250132 198R00...
Page 33: ...29 NOTES...