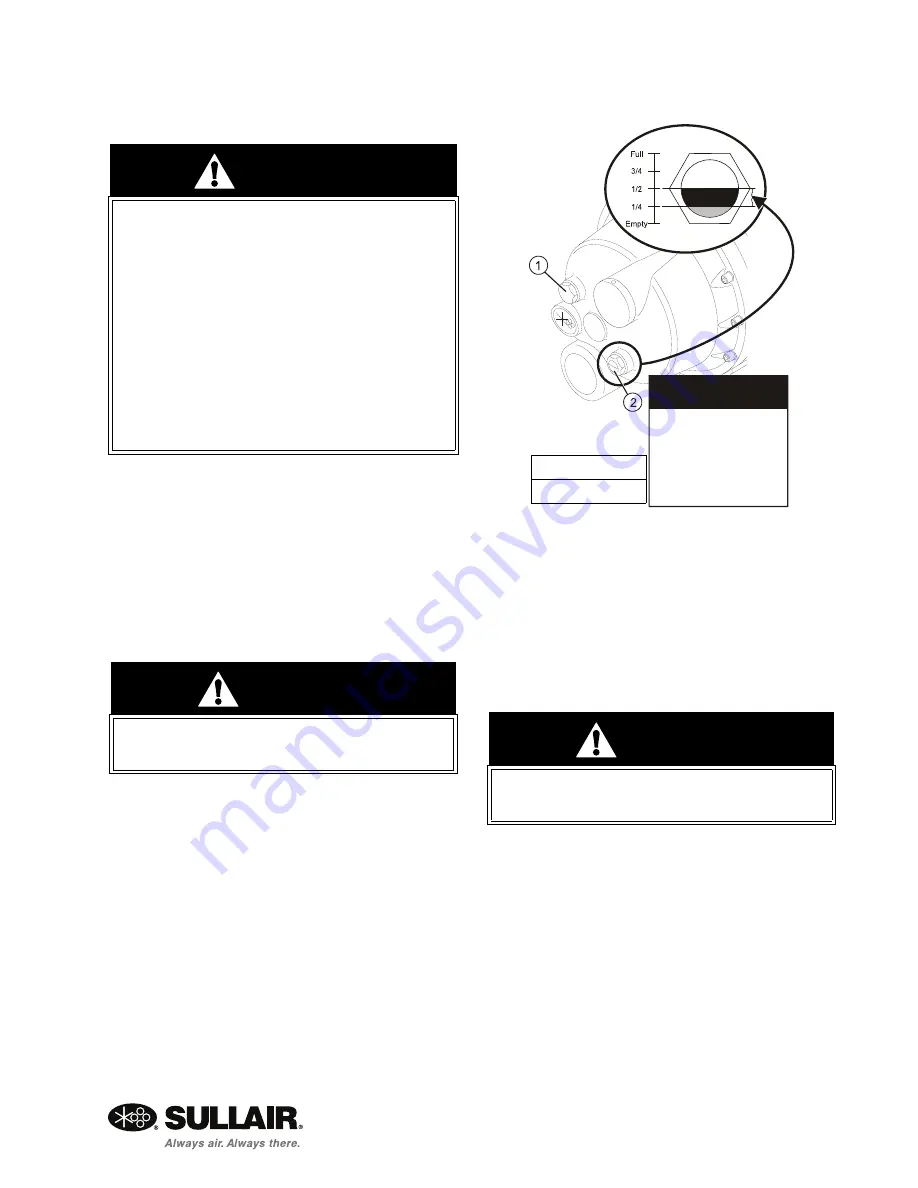
SECTION 3
ES-6 USER MANUAL
21
Maintenance of all other components is still
recommended as indicated in the Operator's Manual.
For light-duty high-humidity service where
condensed moisture and emulsification
(mayonnaise) may occur, the fluid change interval
must be reduced to 300 hours maximum. A
nondetergent fluid with rust, oxidation and foam
inhibitors and good water separation characteristics
should be used.
Contamination of non-detergent mineral fluids with
traces of ATF or detergent motor fluids may lead to
operational problems such as foaming, filter
plugging, orifice or line plugging. Flushing is required
if changing to a different lubricant.
When ambient conditions exceed those noted or if
conditions warrant use of "extended" life lubricants
contact Sullair for recommendation.
Sullair encourages the user to participate in a fluid
analysis program. This could result in a fluid change
interval that is different from those stated in this
manual.
3.3
LUBRICATION GUIDE - 24KT
COMPRESSORS
Sullair 24KT compressors are filled with a lubricant
which rarely needs to be changed. In the event a
change of fluid is required, use only Sullair 24KT
fluid.
Sullair recommends that a 24KT sample be taken at
the first filter change and sent to the factory for
analysis. This is a free service. A sample kit with
instructions and self-addressed container is to be
supplied by your Sullair Representative at start-up.
The user will receive an analysis report with
recommendations.
WARNING
“The Plastic Pipe Institute recommends
against the use of thermoplastic pipe to
transport compressed air or other com-
pressed gases in exposed above ground
locations, e.g. in exposed plant piping." (I)
Sullube should not be used with PVC piping
systems. It may affect the bond at cemented
joints. Certain other plastic materials may
also be affected.
(I) Plastic Pipe Institute, Recommendation
B, Adopted January 19, 1972.
CAUTION
Mixing of other fluids within the compres-
sor will void all warranties.
CAUTION
Mixing of other fluids within the compres-
sor will void all warranties.
Fluid fill level should
be at 1/4 to 1/2 of the
sight glass when the
compressor is
running.
NOTE
1. Fluid Fill Port
2. Sight Glass
Figure 3-1: Fluid Fill Location
Summary of Contents for ES-6 10H
Page 1: ......
Page 6: ...TABLE OF CONTENTS...
Page 12: ...NOTES 12...
Page 18: ...18 NOTES...
Page 23: ...23 NOTES...
Page 26: ...ES 6 USER MANUAL SECTION 3 26 3 6 IDENTIFICATION ES 6 STANDARD WITH ENCLOSURE 02250172 316 R00...
Page 52: ...ES 6 USER MANUAL SECTION 3 52 3 19 WIRING DIAGRAM DUAL CONTROL WYE DELTA 02250058 093 R04...
Page 54: ...ES 6 USER MANUAL SECTION 3 54 3 20 WIRING DIAGRAM SRS 25 100 115 230V 1 60 02250171 733 R00...
Page 56: ...ES 6 USER MANUAL SECTION 3 56 3 21 WIRING DIAGRAM SRS 9 18 220 240V 1 50 02250171 738 R00...
Page 58: ...ES 6 USER MANUAL SECTION 3 58 3 22 WIRING DIAGRAM SRS 24 30 220 240V 1 50 02250171 739 R00...
Page 60: ...60 NOTES...
Page 78: ...78 NOTES...
Page 82: ...82 NOTES...
Page 83: ...NOTES 83...
Page 84: ......