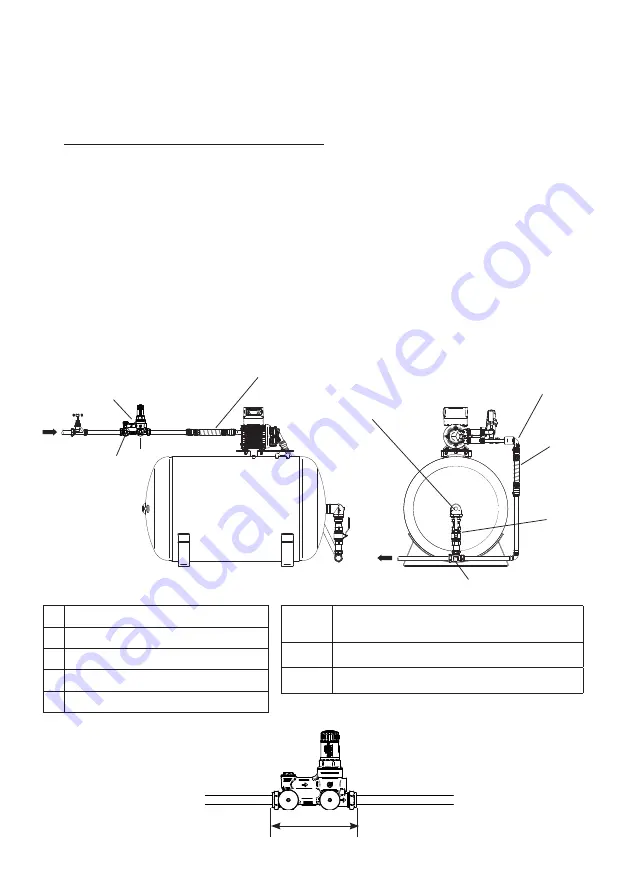
- 20 -
Horizontal Step 2:
The vessel assembly should then be positioned and checked to ensure there is
sufficient space to install the upstream line-in kit between the stopcock and
pressure vessel inlet. Refer to the chart below as a guide.
Monobloc 22/28mm Upstream line-in kit
The Monobloc upstream line-in kit includes:
1 - Monobloc unit
2 - Pressure gauge (upstream)
3 - Pressure gauge (downstream)
4 - Vessel Connector (see step 1)
5 - Isolation Valve (see step 1)
NOTE: the Monobloc can be installed either horizontally or vertically but not upside
down. There are pressure gauge ports on both sides of the Monobloc to allow the
pressure gauges to be visable in any orientation. Follow the directional flow arrows
on the Monobloc to ensure correct installation.
NOTE: It is good practice to install a drain port between the isolation valve and the
vessel.
1 Monobloc unit
2 Pressure gauge (upstream)
3 Pressure gauge (downstream)
4 Mainsboost vessel connector
5 Lever isolating valve
Fig. 24a
Pipe
Size
Minimum pipe length required to install
the Monobloc upstream in line kit (mm) (A)
22 mm 203 mm
28 mm 203 mm
A
Inlet
Outlet
1
2
Flexible
hose
4
5
Flexible
hose
3
Fig. 23a
Push fit elbow
(not supplied)
T-piece (not supplied)