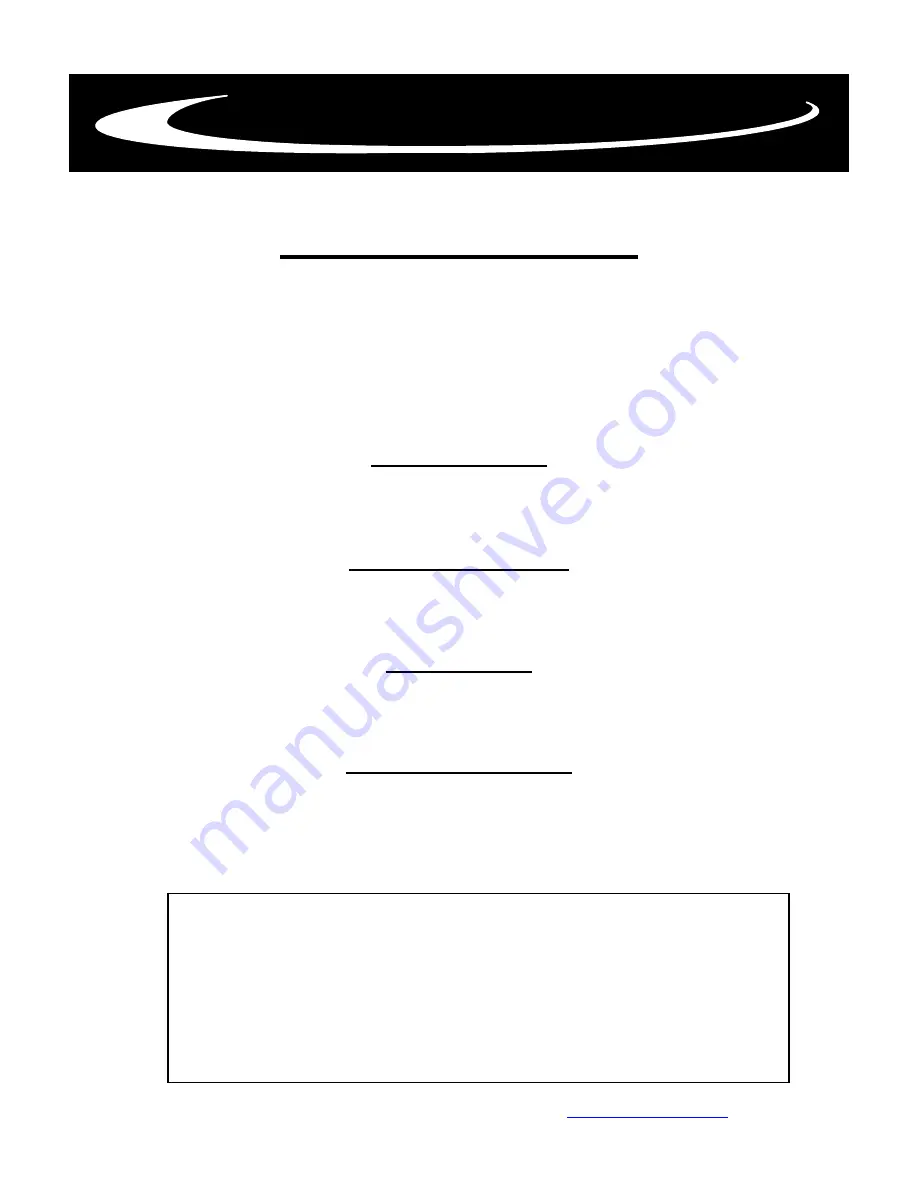
Surface to Surface Inc.
®
Operators Manual
** M-750H **
USE IN CONJUNCTION WITH OEM MANUALS (ENCLOSED)
Unit Serial No. _______________
Hydraulic Motor
SNM2/19C106 – Serial No.__________________
Gorman-Rupp Pump
GR-84B2 – Serial No. ________________
Control Valve
Brand FC51 Serial No.__________________
Links relating to this Manual
www.stsmixers.com
www.grpumps.com
STS-132 Rev. 09/20/12
www.stsmixers.com
Dealer
Summary of Contents for M-750H
Page 12: ...12...
Page 16: ...16 M 750H Identifying Your Machine Components Location of Tags and PIN Plates...
Page 17: ...17 SECTION II Description Care and Maintenance...
Page 30: ...30 SECTION III Set up and Installation of Unit in Detail...
Page 32: ...32 SECTION IV Operating the M 750 Unit...
Page 41: ...41 SECTION V Troubleshooting the M 750 Unit...
Page 44: ...44 SECTION VI Periodic Maintenance Repair Information...
Page 49: ...49 SECTION VII OEM Repair Information...
Page 62: ...62...
Page 63: ...63...
Page 64: ...64...
Page 68: ...68 SECTION VIII Parts Manual...