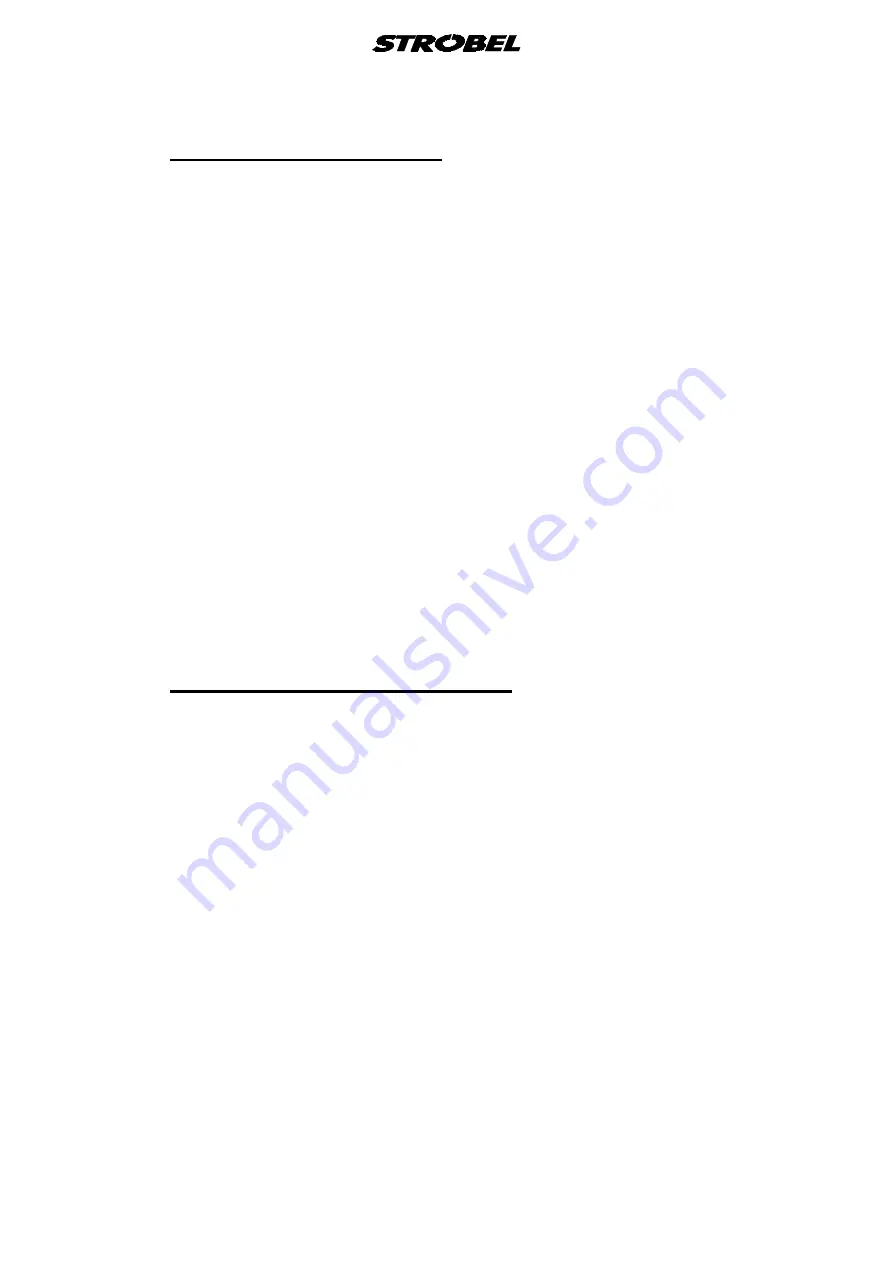
21
MA_218D-TP-R_A4_181015_en
3.7.2
Fitting takes place in reverse order.
However, the following points must be observed for precise adjustment:
Fitting the plunger (Fig. 10)
a)
the cylindrical pin (1) must engage in the groove of the plunger sleeve.
b)
Turn stitch-depth adjustment knob (1) (Fig. 12) clockwise, as far as the
stop (highest position).
c)
Turn plunger check screw (3) so far into the plunger, that when its double-
edged surface engages in the groove of the plunger adjustment screw (2),
the needle is raised 0.2 - 0.3 mm from the plunger.
d)
The plunger reaches its highest position when the tip of the needle is
approx. 2 mm towards the middle of the plunger.
The plunger remains still until the needle point is 2 mm towards the centre
of the plunger.
This value is set by the position of the slide support (5), but care must be
taken that no double stroke occurs, i.e. the slide support must not move
beyond the upper dead point (±0.01 tolerance). It is drilled on the shaft,
i.e. the first threaded pin in the direction of rotation has a tip.
e)
Factory adjustment of the plunger pressure: Screw for plunger adjustment
flush with the plunger guide (4).
Turning the plunger check screw, including the plunger adjustment screw,
clockwise, increases plunger pressure. Turning it anti-clockwise reduces
plunger pressure.
3.7.3
Set plunger motion on plunger shaft in such a way that the pressure exerted
axially by pull-back spring (2) will always by taken over from the pressure
bearing (4) on the right hand above the set ring (5) . Play between disk (1) and
slide (3) should be about 0.1 mm.
Adjusting plunger motion (Fig. 11)
The adjustment screw (2) (Fig. 12) must be limited by set screw (5) (Fig. 12),
the counter nuts (3) (Fig. 12) and the adjustment knob (1) (Fig. 12) so that slide
(3) is adjustable in its crank radius (= x in Fig. 10) from
13 - 16 mm. However, the pullback spring (2) should not be excessively
contractet, to avoid gears being placed one on top of the other, whereby
jamming and / or damaging of the slide edges would result.