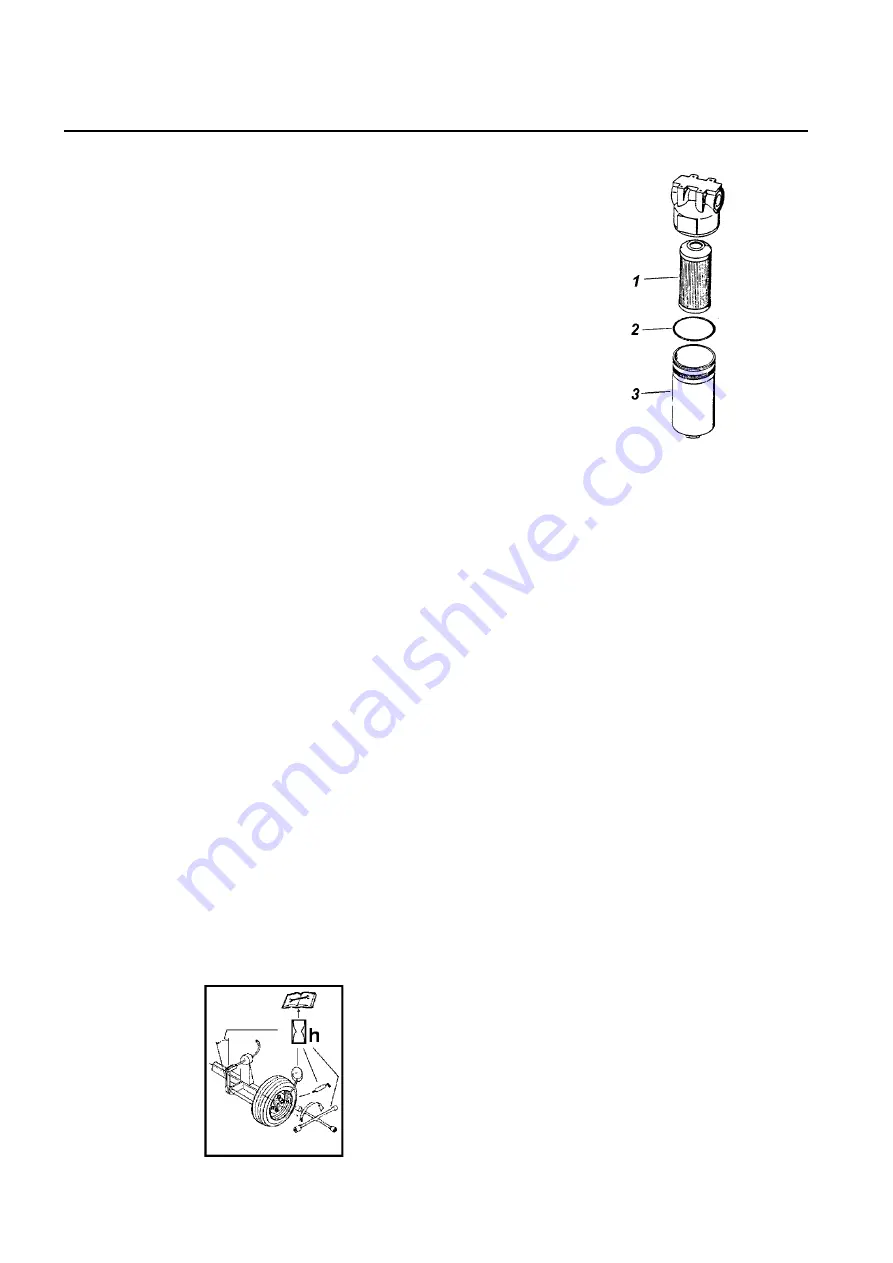
OPERATING INSTRUCTIONS
Page 24 Mega-Trailer
11.2 Hydraulic Oil Filter (for electro-hydraulic system)
The filter element (1) must be replaced after approx. 250 hours of operation.
Thereafter as required, but at least every 1000 hours of operation.
Check the O-ring (2) for damage.
Clean the filter hood (3). The filter element cannot be cleaned.
Soiled filters cause the oil to overheat.
Filter element order no. 870 01 773 (for filter HD 069 – 168)
O – ring dia. 53.6 x 3.5 order no. 870 08 702
11.3 Axles
Never overload axles. Overloading shortens the service life of the bearings and causes damage to the axles. In
addition the following may cause unnecessary wear etc. and should be avoided: Hitting kerbs, driving too fast.
Wheel brakes must always be set correctly to maintain operational safety.
Maintenance Schedule: Axles
After first working runs:
Check state of wheel nuts. If necessary, retighten wheel nuts (M 22 x
1.5 = Md 630Nm). Check leeway of wheel hub bearing.
After 50 service hours:
Check leeway of wheel hub bearing.
Every 100 service hours:
Grease brake camshaft bearing (not applicable with nylon
bushings). Check brake lever setting and adjust if necessary.
Every 500 service hours:
Check leeway of wheel hub bearing: remove dust cap and
split pin, tighten axle nut until hub run almost stops and loosen
up again to next split pin hole. Fix the nut by split pin and test run.
Every 1000 service hours:
Lubricate wheel hub bearing with roller bearing grease. Check
brake linings for wear. If necessary fit new brake linings.
This maintenance schedule has been designed for medium axle loading and brake wear. With heavier use, and
in particular higher demands on the brakes, shorten the maintenance intervals accordingly.
Check air pressure regularly. (see note 5)
Fig. 12