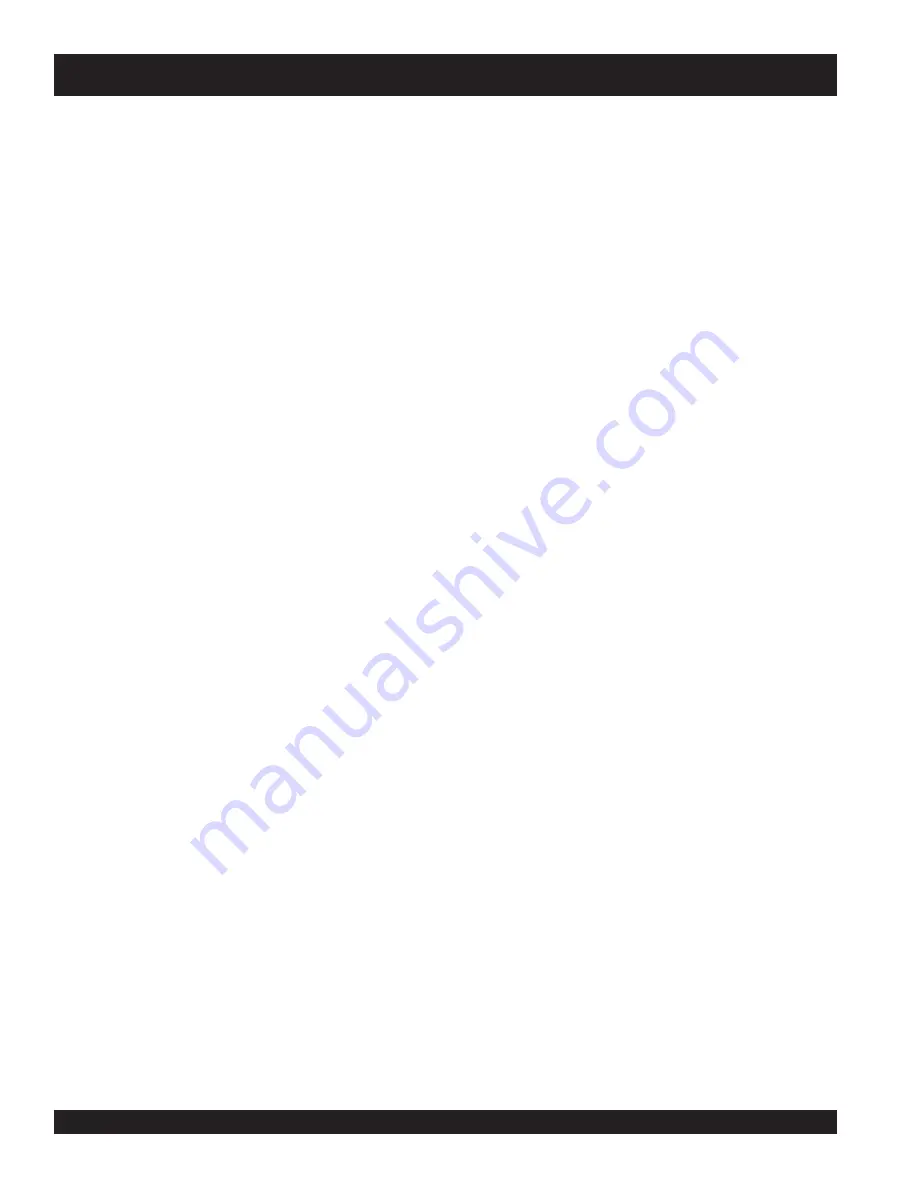
PAGE 14 — HHN 31V
STR46SPVGH • RIDE-ON POWER TROWEL — OPERATION MANUAL — REV. #0 (07/17/08) — PAGE 14
STR46SPVGH — GENERAL INFORMATION
STR46SPVGH Ride-On Power Trowel Familiarization
The STR46SPVGH Ride-On Power Trowel is designed for the
floating and finishing of concrete slabs.
Take a walk around your trowel. Take notice of all the major
components like the engine, blades, air cleaner, fuel system,
fuel shut-off valve, ignition switch etc. Ensure engine and gearbox
lubricant levels are within proper operating range.
Read all the safety instructions carefully. Safety instructions will
be found throughout this manual and on the machine. Keep all
safety information in good, readable condition. Operators should
be well trained on the operation and maintenance of the trowel.
Look at the operator control levers. Grasp the control levers and
move them around a bit. Observe how moving the control levers
cause the gearboxes and frame to move.
Notice the foot pedal which controls the engine and blade speed.
Also take a look at the main driveline of the trowel. Take note
and reference how the belts look, this is the way the belts should
look when adjusted properly.
Before using your trowel, test it on a flat watered down section of
finished concrete. This trial test run will increase your confidence
in using the trowel and at the same time it will familiarize you
with the trowel’s controls and indicators. In addition you will
understand how the trowel will handle under actual conditions.
Engine
This Trowel is equipped with a liquid cooled 31 HP Vanguard
gasoline engine. Refer to the engine owner’s manual for specific
instructions regarding engine operation. This manual is included
with the trowel at the time of shipping. Please contact your nearest
Multiquip Dealer should a replacement manual be required.
Blades
The blades of the STR46SPVGH Ride-On Power Trowel finish
the concrete as they are swirled around the surface. Blades are
classified as combination (10 or 8 inches wide) and finish (6
inches wide). The STR46SPVGH Ride-On Power Trowels are
equipped with five blades, per rotor equally spaced in a radial
pattern and attached to a vertical rotating shaft by means of a
spider assembly
.
Figures 3 and 4 show the location of the controls, indicators and
general maintenance parts. Each control may perform more than
one function. The functions of each control or indicator is on
pages 15 and 16.
Gearboxes
The STR46SPVGH Ride-On Power Trowel consist of two
separate gearbox assemblies that are enclosed in rugged cast
aluminum gear cases.
The gearbox casing holds 50% more oil capacity than
competitors, which allows more lubrication to be provided to
critical points.
Steering
Dual control levers located in front of the operator's seat are
provided for steering this trowel. The control levers are linked to
two spring loaded cylinders.
Push the left control lever forward and pull the right control lever
backward and the trowel will rotate clockwise on approximately
a center axis. Pull the left control lever backward and push the
right control lever forward and the trowel will rotate
counterclockwise. See Table 3 on page 21 for a complete
description on the control levers directional positioning.
Constant Velocity Joints (CV-Joints)
Constant velocity joints insure the efficient transfer of power to
the drive shaft and maintain the timing of the gearboxes without
any chance of slippage.
Training
For training, please use the “
TRAINING CHECKLIST
” located
in the front of this manual (Page 4). This checklist is not intended
to be a substitute for proper training but will provide an outline
for an experienced operator to provide training to a new operator.