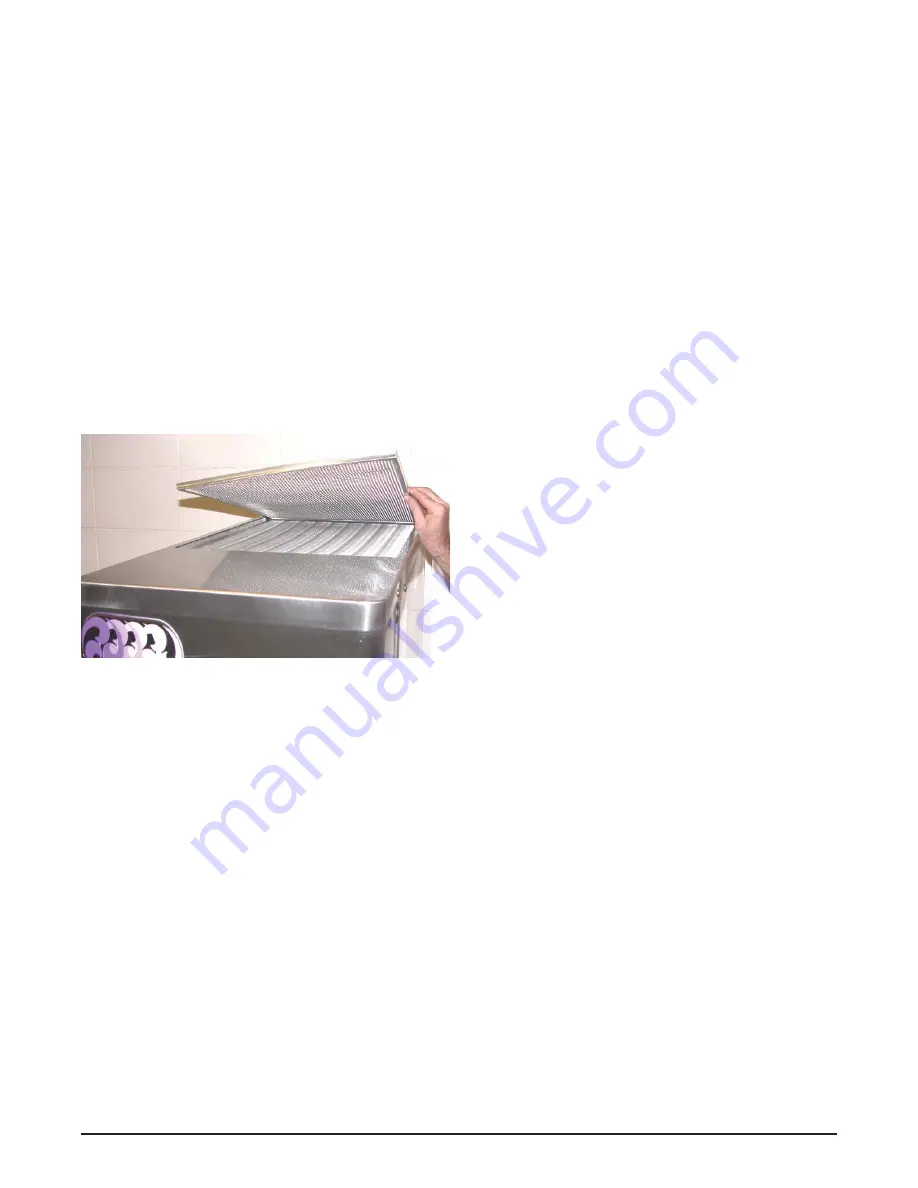
Owner’s Manual #513625
25
SU412 Model Machines
tension for the drive belt. Set the belt tension to
15 - 25 lbs.
C.
If an adjustment is necessary, loosen the four
motor plate retaining nuts, adjust belt tension
then retighten the four nuts.
D.
Using a straightedge, check that the drive motor
pulley is aligned with the speed reducer pulley.
Align the pulley if necessary.
NOTE
Belt life will be increased if new drive belts are
tightened after two or three weeks of operation.
4.13
CONDENSER CLEANING (AIR-COOLED
FREEZERS)
The condenser requires periodic cleaning. To clean the
condenser, refer to the following steps:
A.
Lift the condenser fi lter off of the freezer cover
panel. Visually inspect the condenser fi lter for dirt
(Fig. 4-4).
B.
If the condenser fi lter is dirty, vacuum or brush
it clean. Rinse it with clean water and allow it to
dry before replacing it on the freezer.
NOTE
If the condenser is not kept clean, refrigeration ef-
fi ciency will be lost.
4.14 PREVENTATIVE
MAINTENANCE
It is recommended that a preventative maintenance
schedule be followed to keep the freezer clean and op-
erating properly. The following steps are suggested as a
preventative maintenance guide.
The United States Department of Agriculture and the Food
and Drug Administration require that lubricants used in
food zones be certifi ed for this use. Use lubricants only in
accordance with the manufacturer’s instructions.
A. Daily
checks
Check for any unusual noise or condition and
repair immediately.
B. Monthly
checks
1. Check drive belts for wear and tighten belts if
necessary. (Refer to section 4.12)
2. Check the condenser fi lter for dirt. (Refer to
section 4.13).
4.15 EXTENDED
STORAGE
Refer to the following steps for winterizing the freezer or
for storing the freezer over any long period.
A.
Clean all of the parts that come in contact with
mix thoroughly with warm detergent . Rinse in
clear water and dry all parts. Do not sanitize.
NOTE
Do not let cleaning solution stand in freezer barrel
or mix pump during the shutdown period.
B.
Remove, disassemble, and clean the front door,
auger shaft, and mix pump. Leave disassembled
during the shutdown period.
C.
Place the plastic scraper blade in a plastic bag
with a moist paper towel. This will prevent the
fl ights from becoming brittle if exposed to dry air
over an extended period (over 30 days).
D.
For water-cooled freezers that are left in unheated
buildings, or buildings subject to freezing, the water
must be shut off and disconnected. Disconnect
the fi ttings at the water inlet and the water outlet
lines of the freezer. The fi ttings are located at the
rear of the freezer. Run the compressor for 2 - 3
minutes to open the water valve. Blow out all the
water, fi rst through the water inlet, then through
the water outlet lines with air or carbon dioxide.
Drain the water supply line coming to the freezer.
E.
Place the Pump OFF/ON switch and the Main
Freezer Power OFF/ON switch in the OFF
position.
F.
Disconnect the freezer from the source of the
electrical supply in the building.
Figure 4-4 Removing Condenser Filter