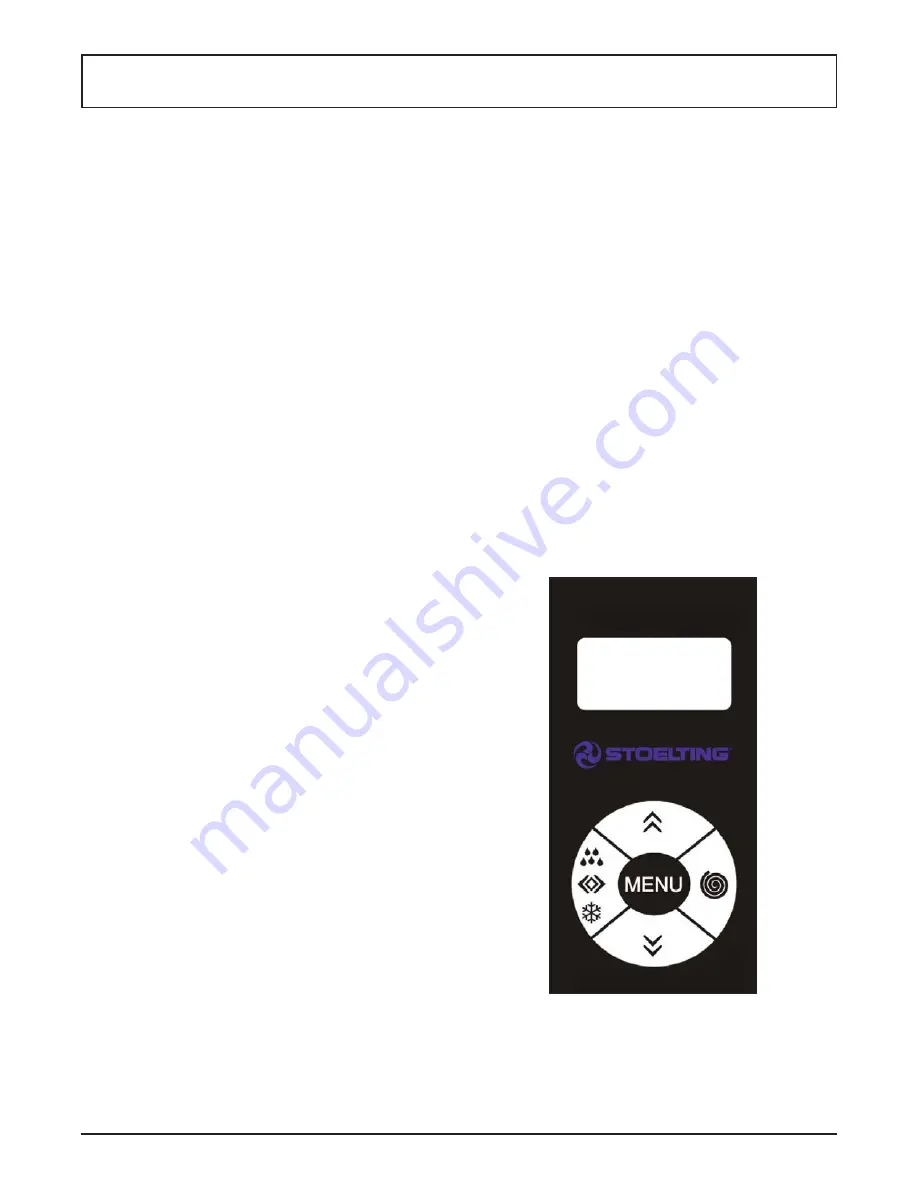
Owner’s Manual #513850 Rev.2
11
CBE Model Machines
SECTION 4
SETTINGS
The control on the First Class machine allows service
personnel the ability to make adjustments to the machine
through the touchpad.
4.1 MAKING ADJUSTMENTS
1.
Press and hold the Menu button for two seconds.
The fi rst adjustment screen will be displayed
(Lamp On/Off).
2.
Press the up or down arrow to make adjustments
to the desired settings.
NOTE
The Cold Selection button and Auger Movement
button act as left and right arrow buttons when
adjusting the time.
3.
Press the Menu button to save the setting and
go to the next screen.
4.
After making adjustments press the Menu button
until the display shows the current status.
4.2 SETTINGS
LAMP
The lamp can be set to On or Off using the arrow
buttons.
BYPASS
The Bypass button is used to enable the auger
rotation when the cover is off.
LOWLEVEL
The LowLevel setting will automatically reduce
the consistency setting to 1 (warmest/most liquid
product) when the tank is low on mix. The display
will read Please Refi ll LowLevel when this setting
is On.
NOTE
The consistency setting automatically returns to
the previous value after mix is added to the tank.
KEYBOARD LOCK
The KeyBoard can be locked to prevent
unauthorized use. When the KeyBoard Lock
is active the current status screen will show a
dot after the consistency/temperature value.
The touchpad will remain locked until the setting
is changed or the power is disconnected and
reconnected.
WASHING
The Washing setting stops the refrigeration and
disables the all buttons on the control aside from
the Menu button.
TIME
The Time setting is used to set to the local time.
It is a 24-hour clock. Press the Auger Movement
or Cold Selection button to enable and move the
cursor. Press the arrow buttons to change the
values. Press the Menu button to save the time
and go to the next screen.
NOTE
When adjusting the time, the date may be different
from the current date. The date cannot be changed
and it does not affect the operation of the machine.
DEFROST ON
The Defrost On setting determines the time when
the defrost mode starts. During Defrost Mode the
product in the tank will be kept at approximately
35ºF. If the setting is the same as the Defrost Off
setting, the defrost mode will be disabled.
DEFROST OFF
The Defrost Off setting determines when the
defrost mode stops and the machine returns to
regular operation. Stoelting recommends a defrost
mode for a minimum of 4 hours.
Figure 4-1 Controls