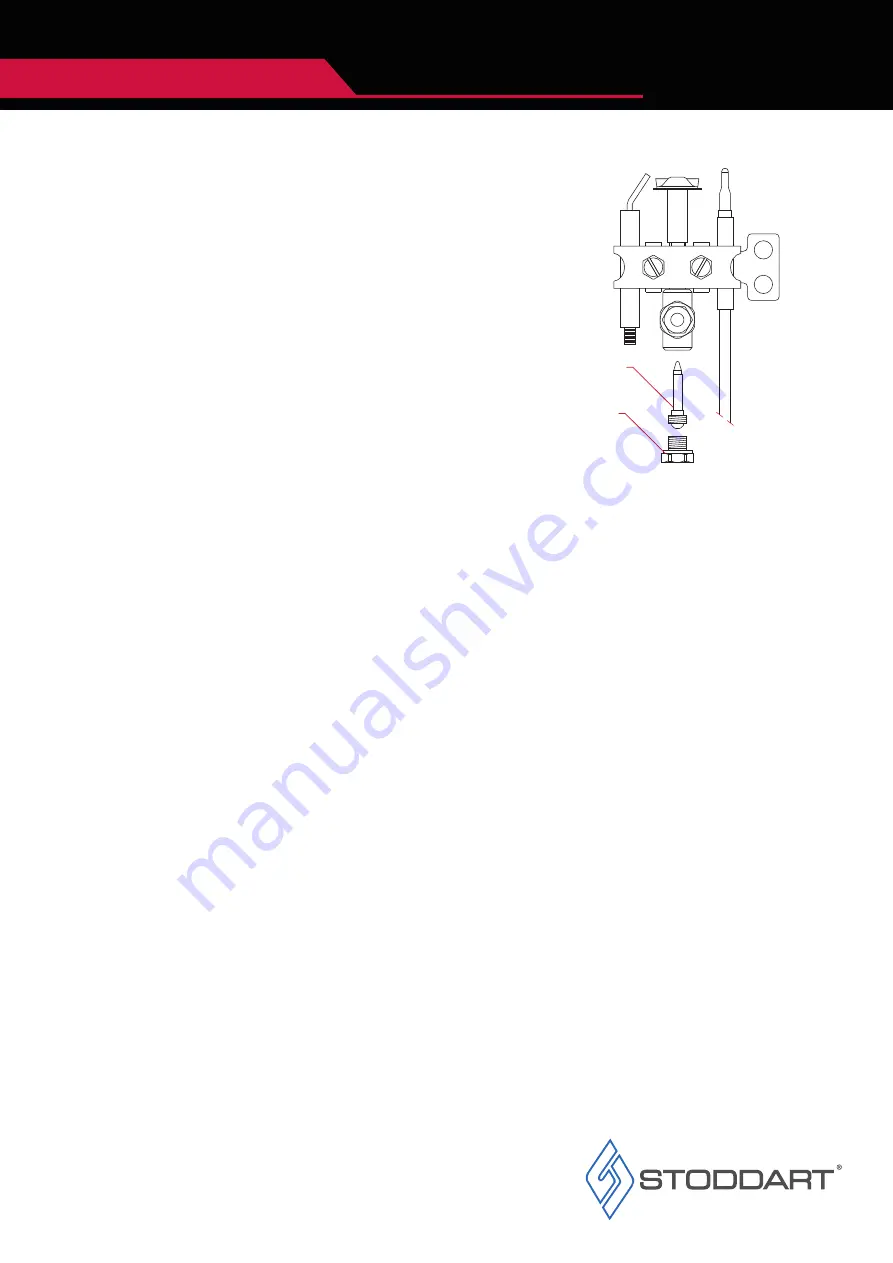
Page 22
Due to continuous product research and development,
the information contained herein is subject to change without notice.
www.stoddart.com.au
www.stoddart.co.nz
700/900
3.0 Installation
To replace the pilot nozzle:
1. Close gas isolation valve
2. Ensure the area is ventilated
3. Unscrew nut ‘F’ (Fig.8) on the pilot gas tube
4. Remove the nozzle ‘G’ (Fig.8) and replace it with the one for the type of gas chosen
5. Re-install the nozzle and nut
6. Check for gas leak using water and detergent solution
3.4.3 Pilot Nozzle Replacement
3.4.4 Final Check - Main Burner
After replacement of burner nozzles and checking the fixed primary air, light the appliance and check that the ignition and flame are operating
correctly, with the minimum adjustment set as per page 8 / 2.1.3. If operating incorrectly, repeat the previous steps.
When conversion has been completed for the relevant Gas Type, it is MANDATORY to edit the Rating Plate, with the new Gas Specification.
Once the Gas conversion has been completed, the unit must be leak tested.
Fig.7.
F
G