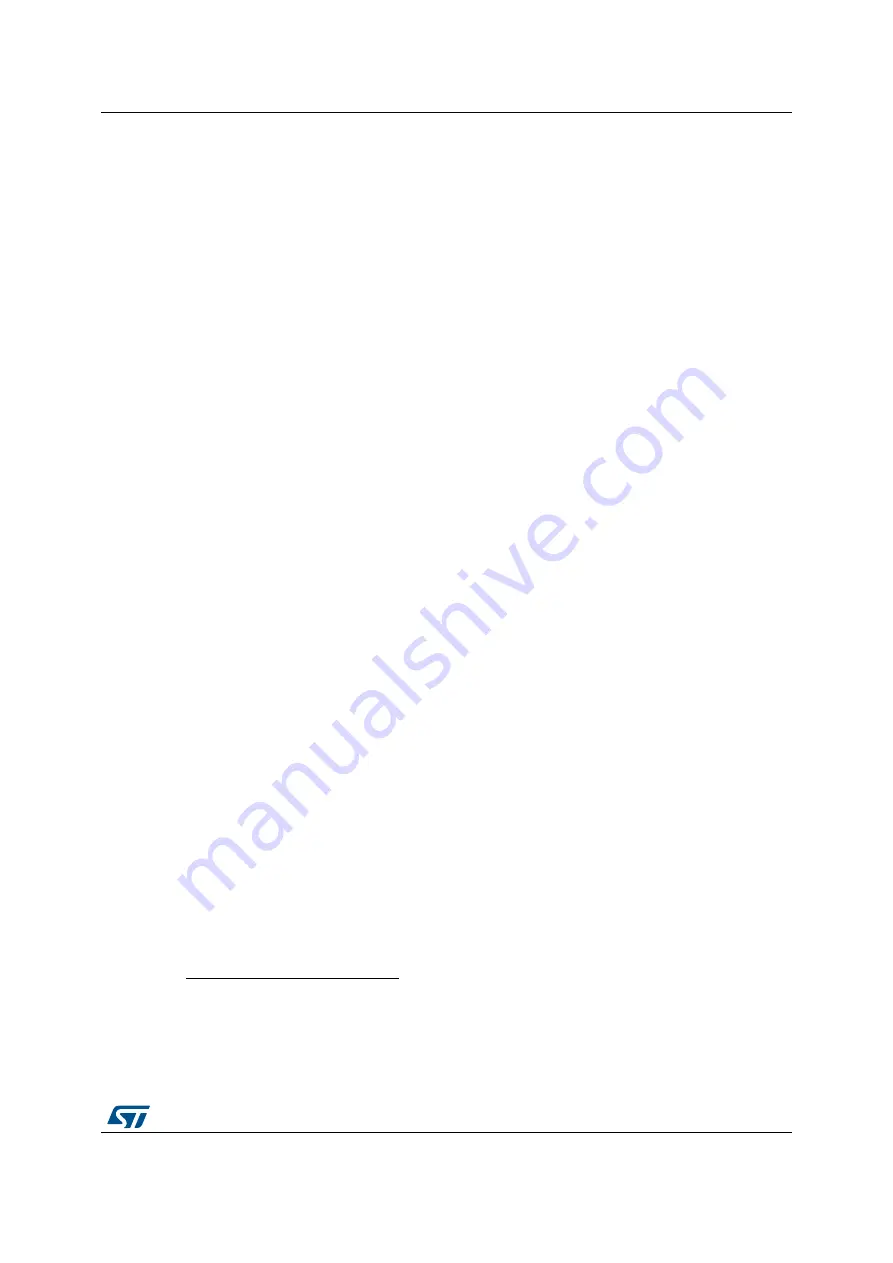
DocID029822 Rev 1
7/23
UM2119
How to use the GUI to configure and test the EVAL-L9907-H
21
D. How to start the MOTOR CONTROLL
1.
STOP all the PWM signals by pressing “STOP PWM” for all 6 channels (L1, L2, L3, H1,
H2 and H3), see Field #5. This action will stop all PWM signals from L9907-H.
2.
Follow the procedure described at point A or B or press one of the two button
“
Automatic Reset 3.3 V
” or “
Automatic Reset 3.3 V
” depending on the Vcc supply
value.
3.
Setup the BLDC motor parameters (polar couples, min and max speed)
4.
Set Kp and Ki values (for example by using a for a 60W BLDC motor set Kp= 10 and
Ki=5)
(a)
5.
Press “Start/Stop Motor” button and the motor will start to run. If the Motor shaft doesn’t
turn it means a fault is present. Stop the Motor Control and reset the fault following the
procedure at section A, point 3 to 5. Restart the motor control
(b)
.
6.
Set the rotation direction: Clockwise or CounterClockwise
7.
Press “Start/Stop Motor” to stop the Motor shaft.
8.
Press the button “STOP” on the top side of the GUI to stop the execution of Labview
code and close the window.
a.
The Kp and Ki constants depend on the BLDC motor characteristics and must be tuned to achieve the best
control
b.
Due to the Start-up procedure developed in the Firmware, depending on the BLDC motor and the BLDC rotor
position, a cross conduction between high-side and low-side Power MOSFET could happen; under this working
a fault is detected.