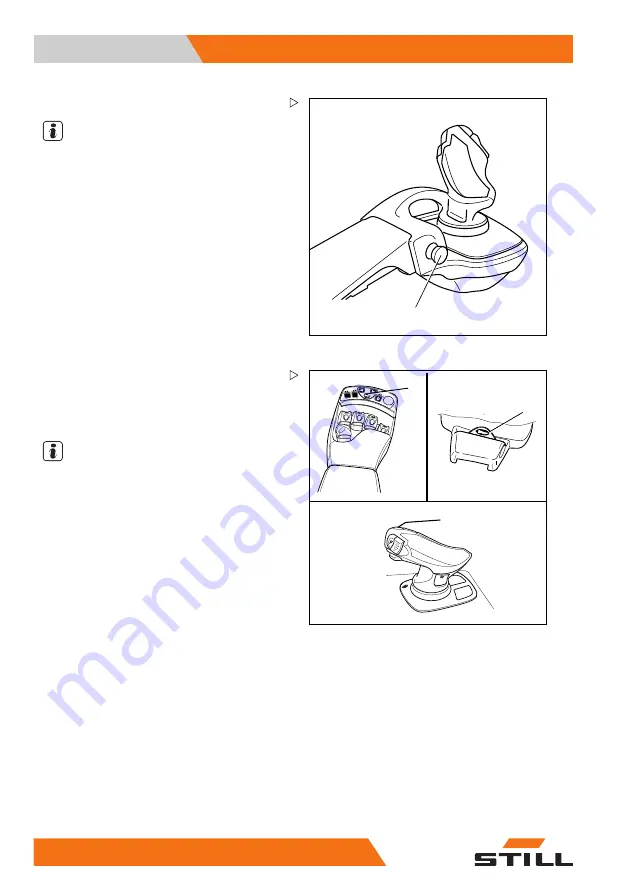
4
Operation
Testing and activities before daily use
6321_003-142
1
Unlocking the emergency off switch
NOTE
Only trucks with a joystick 4Plus (variant) have
an emergency off switch.
– Pull out the emergency off switch (1) until it
unlatches.
F1
F1
F2
F2
7341_003-060
1
1
1
Operating the signal horn
– Push the signal horn button (1).
The signal horn sounds.
NOTE
The signal horn is used to warn people against
imminent danger or to announce your intention
to overtake.
84
57348011800 EN - 11/2018
Summary of Contents for RX70 Series
Page 2: ......
Page 4: ......
Page 13: ...1 Foreword ...
Page 21: ...Foreword 1 Your truck 57348011800 EN 11 2018 9 ...
Page 38: ...1 Foreword Environmental considerations 26 57348011800 EN 11 2018 ...
Page 39: ...2 Safety ...
Page 53: ...Safety 2 Residual risk 57348011800 EN 11 2018 41 ...
Page 71: ...3 Overviews ...
Page 83: ...4 Operation ...
Page 321: ...5 Maintenance ...
Page 328: ...5 Maintenance General maintenance information 316 57348011800 EN 11 2018 ...
Page 330: ...5 Maintenance General maintenance information 318 57348011800 EN 11 2018 ...
Page 334: ...5 Maintenance General maintenance information 322 57348011800 EN 11 2018 ...
Page 378: ...5 Maintenance Remaining ready for operation 366 57348011800 EN 11 2018 ...
Page 379: ...6 1000 hour maintenance annual mainte nance ...
Page 383: ...7 Technical data ...
Page 391: ...Technical data 7 Ergonomic dimensions 57348011800 EN 11 2018 379 ...
Page 394: ...7 Technical data Fuse assignment 382 57348011800 EN 11 2018 ...
Page 404: ......
Page 405: ......
Page 406: ...STILL GmbH 57348011800 EN 11 2018 ...